Preparation method and application of porous molybdenum phosphide/carbon fiber composite material
A composite material, molybdenum phosphide technology, applied in the direction of phosphide, fiber chemical characteristics, electrochemical generator, etc., can solve the problems of corrosive waste acid, consumption of active components, consumption of template agent, etc., to improve conductivity , good magnification performance, simple operation
- Summary
- Abstract
- Description
- Claims
- Application Information
AI Technical Summary
Problems solved by technology
Method used
Image
Examples
Embodiment 1
[0038] (1) Mix 1 mL of 70% phytic acid solution with 9 mL of DMF, add 0.5 g of phosphomolybdic acid and 0.5 mL of pyrrole and continue to stir, then add 1.2 g of polyvinylpyrrolidone, and stir fully to form a uniform spinning solution.
[0039] (2) Fill the spinning solution in step (1) into a syringe. The composite fiber membrane is prepared by electrospinning with an electrospinning device. Among them, the aluminum foil-wrapped cylinder is used as the receiver, the negative high voltage is -2kV, the positive high voltage is 12kV, the receiving distance is 15cm, the relative humidity is 50%, and the ambient temperature is 50°C.
[0040] (3) Place the composite fiber membrane obtained in step (2) in a tube furnace, heat up to 800° C. at a rate of 2° C. / min under an argon atmosphere and keep it warm for 2 hours. After natural cooling, porous molybdenum phosphide / Carbon fiber composite material.
[0041] The SEM figure of the porous molybdenum phosphide / carbon fiber composite...
Embodiment 2
[0044] (1) Mix 1.5mL of 70% phytic acid solution with 8.5mL of DMF, add 0.5g of phosphomolybdic acid and 0.5mL of pyrrole and continue to stir, then add 1.2g of polyvinylpyrrolidone, and fully stir to form a uniform spinning solution.
[0045] (2) Fill the spinning solution in the step (1) into a syringe, and perform electrostatic spinning with an electrostatic spinning device to obtain a composite fiber membrane. Among them, the aluminum foil-wrapped cylinder is used as the receiver, the negative high voltage is -2kV, the positive high voltage is 12kV, the receiving distance is 15cm, the relative humidity is 50%, and the ambient temperature is 50°C.
[0046](3) Place the composite fiber membrane obtained in step (2) in a tube furnace, raise the temperature to 700°C at a rate of 2°C / min under nitrogen atmosphere and keep it warm for 1h, and obtain porous molybdenum phosphide / carbon fiber after natural cooling composite material.
[0047] The prepared porous molybdenum phosphi...
Embodiment 3
[0049] (1) Mix 1 mL of 70% phytic acid solution with 9 mL of DMF, add 0.5 g of phosphomolybdic acid and 1.5 mL of pyrrole and continue to stir, then add 1.2 g of polyvinylpyrrolidone, and stir fully to form a uniform spinning solution.
[0050] (2) Fill the spinning solution in the step (1) into a syringe, and perform electrostatic spinning with an electrostatic spinning device to obtain a composite fiber membrane. Among them, the aluminum foil-wrapped cylinder is used as the receiver, the negative high voltage is -2kV, the positive high voltage is 10kV; the receiving distance is 15cm; the relative humidity is 45%, and the ambient temperature is 55°C.
[0051] (3) The composite fiber membrane obtained in step (2) is placed in a tube furnace, under Ar / H 2 Atmosphere (volume ratio Ar:H 2 =0.95:0.05), the temperature was raised to 800°C at a rate of 2°C / min and held for 2 hours, and the porous molybdenum phosphide / carbon fiber composite material was obtained after natural coolin...
PUM
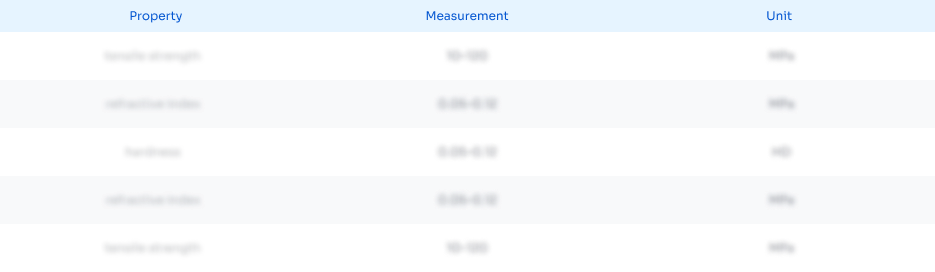
Abstract
Description
Claims
Application Information

- R&D Engineer
- R&D Manager
- IP Professional
- Industry Leading Data Capabilities
- Powerful AI technology
- Patent DNA Extraction
Browse by: Latest US Patents, China's latest patents, Technical Efficacy Thesaurus, Application Domain, Technology Topic, Popular Technical Reports.
© 2024 PatSnap. All rights reserved.Legal|Privacy policy|Modern Slavery Act Transparency Statement|Sitemap|About US| Contact US: help@patsnap.com