Multifunctional super-hydrophobic surface preparation method based on foam finishing technology
A super-hydrophobic surface and foam finishing technology, which is applied in the field of multi-functional super-hydrophobic surface preparation, can solve the problems of endangering the personal safety of environmental workers, difficulty in ensuring hydrophobicity, and low production efficiency, so as to prevent external liquid pollution and realize large-scale Industrialization, the effect of less liquid carry rate
- Summary
- Abstract
- Description
- Claims
- Application Information
AI Technical Summary
Problems solved by technology
Method used
Image
Examples
Embodiment 1
[0043] 1) Preparation of hydrophobic finishing solution: Add 0.6 g of polydimethylsiloxane and 0.06 g of supporting curing agent into deionized water, ultrasonically vibrate and stir vigorously, then add 0.1 g of sodium lauryl sulfate and 0.04 g of dodecyl alcohol, continue to add 0.6 g of fumed silica nanoparticles, and stir vigorously under the action of ultrasonic oscillation to obtain a hydrophobic finishing solution;
[0044] 2) Applying foam to finish the fabric: Stir the hydrophobic finishing solution prepared above with a stirrer at 2500 r / min for 180 s until it foams, apply the hydrophobic foam to the polyester fabric and dry it in an oven at 150 °C for 120 min. The result is a long-lasting, multifunctional superhydrophobic fabric.
[0045] The surface structure of the treated polyester fabric was observed through a scanning electron microscope, and the scanning electron microscope photos are as follows: figure 1 shown. Lay the polyester fabric flat, add deionized w...
Embodiment 2
[0048] 1) Preparation of hydrophobic finishing solution: Add 1.5 g of polydimethylsiloxane and 0.15 g of supporting curing agent into deionized water, ultrasonically oscillate and stir vigorously, then add 0.3 g of sodium lauryl sulfate and 0.1 g of dodecanol, then add 1.5 g of fumed silica nanoparticles, and continue to stir vigorously under the action of ultrasonic oscillation to obtain a hydrophobic finishing solution;
[0049] 2) Apply foam to finish the fabric: Stir the hydrophobic finishing solution prepared above with a stirrer at 2000 r / min for 240 s until it foams, apply the hydrophobic foam to the polyester fabric, and control the amount of hydrophobic foam to make the polyester fabric One side is finished with hydrophobic foam, and the other side retains its original wettability as much as possible. Put the finished fabric above into an oven at 150°C to dry for 100 min, thus obtaining a long-lasting hydrophilic / hydrophobic Janus fabric surface.
[0050] Lay the sur...
Embodiment 3
[0053] 1) Preparation of hydrophobic finishing solution: Add 1.2 g of polydimethylsiloxane and 0.15 g of supporting curing agent into deionized water, ultrasonically oscillate and stir vigorously, then add 0.2 g of sodium lauryl sulfate and 0.12 g of dodecyl alcohol, then added 0.8 g of fumed silica nanoparticles, and continued to stir vigorously under the action of ultrasonic oscillation to obtain a hydrophobic finishing solution. Divide the hydrophobic finishing solution into two parts, A and B, add the blue dye methylene blue to A, and add the red dye erythrosin B sodium salt to B.
[0054] 2) Applying foam to finish the fabric: the two dyed hydrophobic finishing solutions prepared above were stirred with a stirrer at a speed of 2500r / min for 120 s until foaming, and a small amount of blue foam produced in A was applied to one side of the thick cotton cloth , put it in a 150°C oven to dry for 5 minutes, take it out, and then coat a small amount of red foam produced in B on ...
PUM
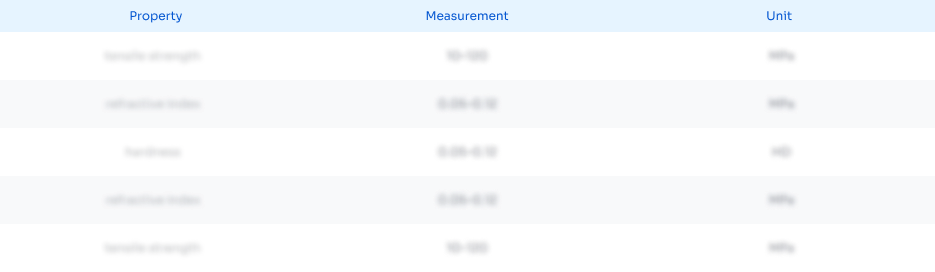
Abstract
Description
Claims
Application Information

- Generate Ideas
- Intellectual Property
- Life Sciences
- Materials
- Tech Scout
- Unparalleled Data Quality
- Higher Quality Content
- 60% Fewer Hallucinations
Browse by: Latest US Patents, China's latest patents, Technical Efficacy Thesaurus, Application Domain, Technology Topic, Popular Technical Reports.
© 2025 PatSnap. All rights reserved.Legal|Privacy policy|Modern Slavery Act Transparency Statement|Sitemap|About US| Contact US: help@patsnap.com