High-strength and high-toughness steel for drill rod joint and preparation method thereof
A technology for drill pipe joints and high toughness, which is applied in the field of high-strength and high-toughness steel for drill pipe joints and its preparation. It can solve the problems of not meeting the requirements of drill pipe joints, low strength and impact toughness, etc., and achieve improved tempering resistance. Improvement of stability, strength and toughness, effect of grain refinement
- Summary
- Abstract
- Description
- Claims
- Application Information
AI Technical Summary
Problems solved by technology
Method used
Image
Examples
Embodiment 1
[0019] A high-strength and high-toughness steel for drill pipe joints, the grade is 4137HM, and the element composition contains C: 0.36%, Si: 0.25%, Mn: 0.93%, P: 0.008%, S: 0.003%, Cr: 1.10%, Mo: 0.26%, Ni: 0.08%, Nb: 0.01%, Ti: 0.015%, and the balance is Fe and unavoidable impurities.
[0020] The specific processing procedure is as follows:
[0021] (1) Smelting and refining: the smelting step adopts electric furnace steelmaking, and the refining step adopts LF+VD refining outside the furnace; in the LF refining process, the niobium content in molten steel is made to be 0.01% by adding niobium, and argon is blown and stirred throughout the process, so that the inclusions are fully Floating; the vacuum treatment time of the VD process is 20min, and the vacuum pressure is 0.5mbar; after VD, titanium wire is fed for titanium alloying, and the titanium weight percentage is controlled to be 0.015%;
[0022] (2) Carry out continuous casting and rolling to the molten steel after...
Embodiment 2
[0028] A high-strength and high-toughness steel for drill pipe joints, the grade is 4137HM, and the element composition contains C: 0.38%, Si: 0.30%, Mn: 0.97%, P: 0.010%, S: 0.004%, Cr: 1.20%, Mo: 0.32%, Ni: 0.11%, Nb: 0.03%, Ti: 0.020%, and the balance is Fe and unavoidable impurities.
[0029] The specific processing procedure is as follows:
[0030] (1) Smelting and refining: the smelting step adopts electric furnace steelmaking, and the refining step adopts LF+VD refining outside the furnace; in the LF refining process, niobium content in molten steel is made to be 0.11% by adding niobium, and argon is blown and stirred throughout the process so that the inclusions are fully Floating; the vacuum treatment time of the VD process is 25min, and the vacuum pressure is 0.8mbar; after VD, titanium wire is fed for titanium alloying, and the titanium weight percentage is controlled to 0.020%;
[0031] (2) Carry out continuous casting and rolling to the molten steel after refinin...
Embodiment 3
[0037] A high-strength and high-toughness steel for drill pipe joints, the grade is 4137HM, the element composition contains C: 0.35%, Si: 0.20%, Mn: 1.10%, P: 0.009%, S: 0.002%, Cr: 1.00%, Mo: 0.33%, Ni: 0.12%, Nb: 0.02%, Ti: 0.025%, and the balance is Fe and unavoidable impurities.
[0038] The specific processing procedure is as follows:
[0039](1) Smelting and refining: the smelting step adopts electric furnace steelmaking, and the refining step adopts LF+VD refining outside the furnace; in the LF refining process, the niobium content in molten steel is made to be 0.12% by adding niobium, and argon is blown and stirred throughout the process, so that the inclusions are fully Floating; the vacuum treatment time of VD process is 20min, and the vacuum pressure is 0.5mbar; after VD, titanium wire is fed to carry out titanium alloying, and the content of titanium weight percentage is controlled to 0.025%;
[0040] (2) Carry out continuous casting and rolling to the molten ste...
PUM
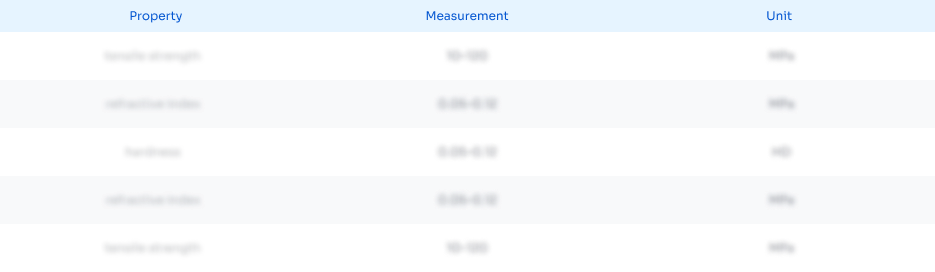
Abstract
Description
Claims
Application Information

- R&D
- Intellectual Property
- Life Sciences
- Materials
- Tech Scout
- Unparalleled Data Quality
- Higher Quality Content
- 60% Fewer Hallucinations
Browse by: Latest US Patents, China's latest patents, Technical Efficacy Thesaurus, Application Domain, Technology Topic, Popular Technical Reports.
© 2025 PatSnap. All rights reserved.Legal|Privacy policy|Modern Slavery Act Transparency Statement|Sitemap|About US| Contact US: help@patsnap.com