Batch preparation method of ultra-nano diamond coated cutting tool with high finish and complex shape
A diamond coating, high finish technology, applied in metal material coating process, coating, gaseous chemical plating and other directions, can solve the problem that the surface finish of the tool cannot meet the requirements of machining accuracy and tool life, and the surface roughness of the diamond coating High problems, to achieve the effect of low surface roughness, improved machining accuracy and tool life, and high machining accuracy
- Summary
- Abstract
- Description
- Claims
- Application Information
AI Technical Summary
Problems solved by technology
Method used
Image
Examples
Embodiment 1
[0046] 105 cemented carbide milling cutters for graphite processing (blade diameter 4mm, blade length 20mm, shank diameter 4mm, total length 75mm) were pretreated, that is, "potassium permanganate solution was oxidized for 20 minutes to roughen the surface of the cemented carbide, The mixed solution of concentrated hydrochloric acid and hydrogen peroxide is etched for 30 seconds to remove cobalt from the surface of the cemented carbide, placed in a suspension of nano-sized diamond micropowder to uniformly plant crystals on the surface of the tool, and placed in acetone for ultrasonic cleaning. Then, place the pretreated 105 milling cutters in the reaction chamber of the HFCVD equipment, figure 1 Schematic diagram of the layout of hot wires for high-gloss ultra-nano-diamond film-coated tools prepared in batches for HFCVD, where methane and hydrogen are fed in. The flow rates of methane and hydrogen are 160sccm and 800sccm respectively, the air pressure is 800Pa, the number of ho...
Embodiment 2
[0048] 140 tungsten carbide micro-drills (blade diameter 0.3mm, blade length 8mm, shank diameter 3.175mm, total length 38mm) for the processing of printed circuit boards (PCB) were pretreated, that is, "potassium permanganate solution was oxidized for 10 minutes to make Roughen the surface of the cemented carbide, etch with a mixed solution of concentrated hydrochloric acid and hydrogen peroxide for 8 seconds to remove cobalt from the surface of the cemented carbide, place it in a suspension of nano-sized diamond micropowder and perform ultrasonic oscillation on the surface of the tool, and place it in acetone for ultrasonication Cleaning" process. Then, 140 PCB micro-drills after pretreatment were placed in the reaction chamber of the HFCVD equipment, and two gas paths were set up, 300 sccm pure hydrogen gas was passed into one gas path, and 250 sccm carrying hydrogen gas was passed into the other gas path. Introduce the mixture of acetone and trimethyl borate in the bubble b...
Embodiment 3
[0050] 90 cemented carbide milling cutters for graphite processing (blade diameter 6mm, blade length 15mm, shank diameter 6mm, total length 50mm) were pretreated, that is, "potassium permanganate solution was oxidized for 20 minutes to roughen the surface of the cemented carbide, The mixed solution of concentrated hydrochloric acid and hydrogen peroxide is etched for 30 seconds to remove cobalt from the surface of the cemented carbide, placed in a suspension of nano-sized diamond micropowder to uniformly plant crystals on the surface of the tool, and placed in acetone for ultrasonic cleaning. Then, 80 graphite milling cutters after pretreatment were placed in the reaction chamber of the HFCVD equipment. 0mm, two channels of gas (methane and hydrogen) are introduced. The deposition is divided into 4 stages: the first stage is the nucleation stage, the methane flow rate is 40sccm, the hydrogen flow rate is 900sccm, the air pressure is 1100Pa, and the time is 30min; the second st...
PUM
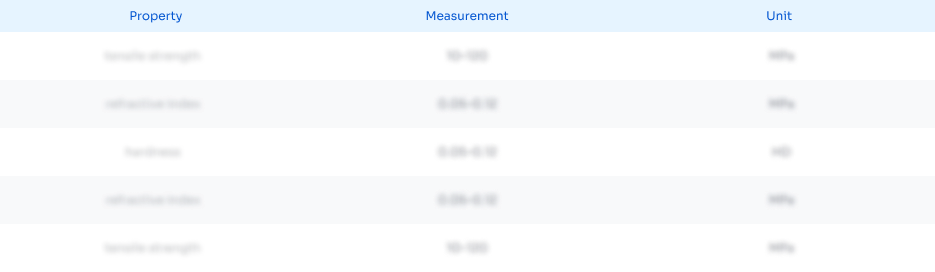
Abstract
Description
Claims
Application Information

- Generate Ideas
- Intellectual Property
- Life Sciences
- Materials
- Tech Scout
- Unparalleled Data Quality
- Higher Quality Content
- 60% Fewer Hallucinations
Browse by: Latest US Patents, China's latest patents, Technical Efficacy Thesaurus, Application Domain, Technology Topic, Popular Technical Reports.
© 2025 PatSnap. All rights reserved.Legal|Privacy policy|Modern Slavery Act Transparency Statement|Sitemap|About US| Contact US: help@patsnap.com