Method for preparing grating with submicron structure
A sub-micron and grating technology, which is applied in the field of preparation of sub-micron structured gratings, to achieve the effects of improving diffraction efficiency, good grating uniformity, and high pattern accuracy
- Summary
- Abstract
- Description
- Claims
- Application Information
AI Technical Summary
Problems solved by technology
Method used
Image
Examples
preparation example Construction
[0037] The present invention provides a method for preparing a submicron structure grating, which includes the following steps:
[0038] (1) After spin-coating an electron beam resist on a silicon wafer, perform electron beam exposure to obtain an electron beam resist layer;
[0039] Among them, the beam current of electron beam exposure is 1nA~20nA; the dose of electron beam exposure is 100μC / cm 2 ~300μC / cm 2 ;
[0040] (2) Use the electron beam resist layer as a mask to perform dry etching to prepare a nanoimprint template;
[0041] Among them, the dry etching gas in step (2) includes SF 6 And C 4 F 8 ;SF 6 The air flow is 4sccm~20sccm; C 4 F 8 The gas flow rate is 4sccm~20sccm; the cavity pressure of dry etching is 4mTorr~25mTorr; the radio frequency power is: 10W-50W; the inductive coupling power is 100W~1500W;
[0042] (3) Transfer the sub-micron structure on the nanoimprint template to the thermally cured transparent soft film, and spin-coat the UV-curable imprint glue on the subs...
Embodiment
[0055] Such as figure 1 As shown, this embodiment provides a method for preparing a sub-micron structure grating, including the following steps:
[0056] Step 1: Take a 430 micron thick 2-inch p-type For silicon wafers with crystal orientation, after conventional wet cleaning, the electron beam resist ARP6200.09 is spin-coated on the silicon wafer, see Figure 2(a) to obtain the electron beam resist;
[0057] Step 2: Perform electron beam exposure on the electron beam resist, the exposure dose is 240μC / cm 2 , The current is 15nA; after the exposure is completed, develop with MIBK for 40s and fix with isopropanol for 70s. See Figure 2(b) to obtain the electron beam resist layer;
[0058] Step 3: Use the electron beam resist layer exposed by the electron beam as the mask of the silicon wafer, and use ICP etching to prepare the nanoimprint template, see Figure 2(c);
[0059] Among them, the etching parameters are: SF 6 The flow rate is 12sccm; C 4 F 8 The flow rate is 12sccm; the radio fr...
PUM
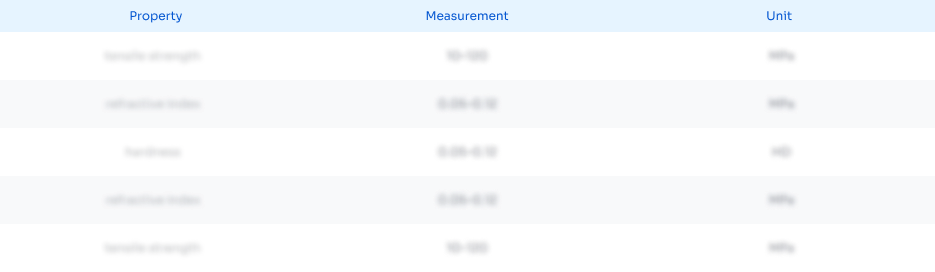
Abstract
Description
Claims
Application Information

- R&D
- Intellectual Property
- Life Sciences
- Materials
- Tech Scout
- Unparalleled Data Quality
- Higher Quality Content
- 60% Fewer Hallucinations
Browse by: Latest US Patents, China's latest patents, Technical Efficacy Thesaurus, Application Domain, Technology Topic, Popular Technical Reports.
© 2025 PatSnap. All rights reserved.Legal|Privacy policy|Modern Slavery Act Transparency Statement|Sitemap|About US| Contact US: help@patsnap.com