Local heat treatment method for primary and secondary heating, regulating and controlling residual stress
A technology of local heat treatment and residual stress, applied in the field of heat treatment, can solve the problems of stress corrosion cracking of welded joints, uneven microstructure of welded joints, and difficulty in eliminating residual stress of welding, etc., to reduce labor intensity, easy operation, and reduce construction. effect of cycles
- Summary
- Abstract
- Description
- Claims
- Application Information
AI Technical Summary
Problems solved by technology
Method used
Image
Examples
Embodiment example 1
[0083] Such as Figure 1~3 , a super-large pressure vessel has a cylinder thickness of 50mm and a diameter of 40m. The reinforcing plate is a "circular" reinforcing plate with a thickness of 120mm and a diameter of about 4.2m. The width of the main heating belt is 600mm, the distance between the main and auxiliary heating belts is 400mm, the width of the auxiliary heating belt is 400mm, and the maximum temperature of the auxiliary heating is 500°C. Numerical simulation is carried out according to the heat treatment conditions and related inputs. Only the main heating method, that is, "bull's eye" heating, is used to obtain the stress cloud distribution after the heating is completed as follows: figure 2 shown. Depend on figure 2 It can be seen that a large compressive stress is generated on the top and bottom of the reinforcing plate, and the distance from the weld seam is about 600mm. On this basis, the local heat treatment method of primary and secondary cooperative he...
Embodiment example 2
[0085] Such as figure 1 , establish an axisymmetric model, the size of the closed weld of the cylinder is φ20000×50×92000, V-shaped groove, a total of 60 welds. The width of the main heating belt is 400mm, the distance between the main and auxiliary heating is 300mm, the width of the auxiliary heating belt is 300mm, and the holding temperature of the auxiliary heating is 300°C. Welding and heat treatment process analysis of body closing welds is carried out by using numerical simulation method. The local heat treatment method of primary and secondary heating is adopted. Output the axial and hoop stress distribution of the P1 path near the inner wall weld of the closing weld of the cylinder, as shown in the figure. Figure 4 (a) The ordinate indicates the axial stress along the P1 path of the inner wall of the closed weld of the cylinder, and the abscissa indicates 30mm from both sides of the weld; Figure 4 The ordinate in (b) represents the hoop stress along the P1 path of...
PUM
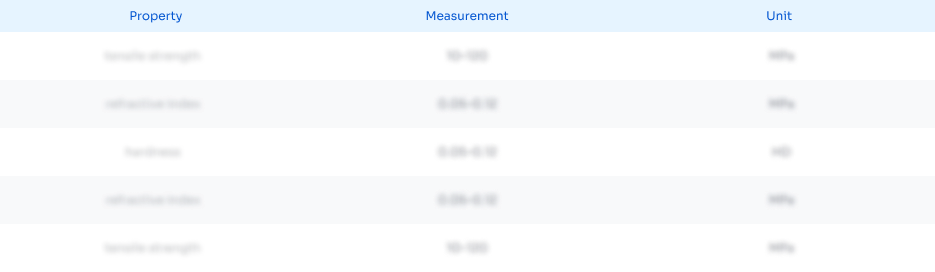
Abstract
Description
Claims
Application Information

- Generate Ideas
- Intellectual Property
- Life Sciences
- Materials
- Tech Scout
- Unparalleled Data Quality
- Higher Quality Content
- 60% Fewer Hallucinations
Browse by: Latest US Patents, China's latest patents, Technical Efficacy Thesaurus, Application Domain, Technology Topic, Popular Technical Reports.
© 2025 PatSnap. All rights reserved.Legal|Privacy policy|Modern Slavery Act Transparency Statement|Sitemap|About US| Contact US: help@patsnap.com