Preparation method of epoxy resin wear-resistant composite material
A technology of epoxy resin and composite materials, which is applied in the field of material processing, and can solve problems such as affecting the service life of epoxy resin materials and unsatisfactory wear resistance
- Summary
- Abstract
- Description
- Claims
- Application Information
AI Technical Summary
Problems solved by technology
Method used
Examples
Embodiment 1
[0021] A preparation method of epoxy resin wear-resistant composite material, comprising the following steps:
[0022] (1) Raw material pretreatment:
[0023] a. Wash the SiC particles with clean water to remove the doped lime soil, bake at 200°C to remove the volatile pollutants adsorbed on the surface of the SiC particles, soak in acetone solution after cooling down, and ultrasonically clean twice, each time for 5 minutes, to wash off the SiC particles The non-volatile pollutants remaining on the surface should be dried at 130°C;
[0024] b. Dry the mixer and mold to avoid bringing in moisture;
[0025] (2) Stirring and mixing: Pour E44 type epoxy resin and E51 type epoxy resin into the mixer, stir evenly to obtain mixed epoxy resin, add dibutyl phthalate and keep stirring, dibutyl phthalate The amount of adding is 15% of the mass of the mixed epoxy resin, then add KH-55 organosilane coupling agent and organosilicone oil defoamer, continue stirring for 20min, add the pretr...
Embodiment 2
[0028] A preparation method of epoxy resin wear-resistant composite material, comprising the following steps:
[0029] (1) Raw material pretreatment:
[0030] a. Wash the SiC particles with clean water to remove the doped lime soil, bake at 300°C to remove the volatile pollutants adsorbed on the surface of the SiC particles, soak in acetone solution after cooling down, and ultrasonically clean twice, each time for 8 minutes, to wash off the SiC particles The non-volatile pollutants remaining on the surface should be dried at 150°C;
[0031] b. Dry the mixer and mold to avoid bringing in moisture;
[0032] (2) Stirring and mixing: Pour E44 type epoxy resin and E51 type epoxy resin into the agitator, stir evenly to obtain mixed epoxy resin, add unsaturated polyester resin and keep stirring, the amount of unsaturated polyester resin added is Mix 20% of the mass of epoxy resin, then add KH-55 organosilane coupling agent and organosilicone oil defoamer, keep stirring for 30min, a...
Embodiment 3
[0035] A preparation method of epoxy resin wear-resistant composite material, comprising the following steps:
[0036] (1) Raw material pretreatment:
[0037] a. Wash the SiC particles with clean water to remove the doped lime soil, bake at 220°C to remove the volatile pollutants adsorbed on the surface of the SiC particles, soak in acetone solution after cooling down, and ultrasonically clean twice, each time for 5 minutes, to wash off the SiC particles The remaining non-volatile pollutants on the surface should be dried at 135°C;
[0038] b. Dry the mixer and mold to avoid bringing in moisture;
[0039] (2) Stirring and mixing: Pour E44 type epoxy resin and E51 type epoxy resin into the agitator, stir evenly to obtain mixed epoxy resin, add polyurethane prepolymer and keep stirring, the addition amount of adjacent polyurethane prepolymer is mixing 25% of the mass of epoxy resin, then add KH-55 organosilane coupling agent and organosilicone oil defoamer, keep stirring for 2...
PUM
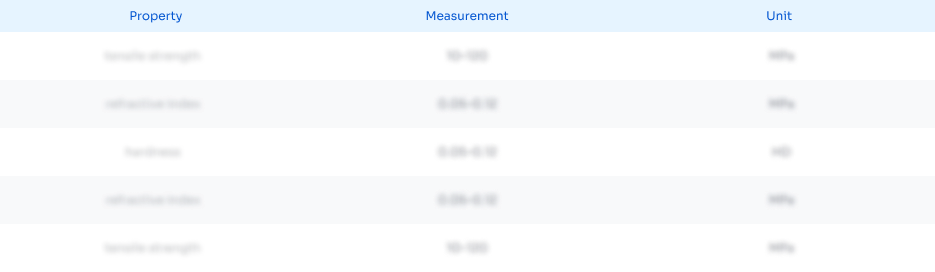
Abstract
Description
Claims
Application Information

- R&D
- Intellectual Property
- Life Sciences
- Materials
- Tech Scout
- Unparalleled Data Quality
- Higher Quality Content
- 60% Fewer Hallucinations
Browse by: Latest US Patents, China's latest patents, Technical Efficacy Thesaurus, Application Domain, Technology Topic, Popular Technical Reports.
© 2025 PatSnap. All rights reserved.Legal|Privacy policy|Modern Slavery Act Transparency Statement|Sitemap|About US| Contact US: help@patsnap.com