Method for preparing high-performance cementing material from modified calcium-magnesium phosphate rock tailings
A technology of phosphate rock tailings and cementitious materials, which is applied in cement production, flotation, solid separation, etc., and can solve problems such as restricting the development of enterprises, geological disasters of tailings ponds, high costs of tailings pond construction and operation management, etc. , to achieve the effect of reducing inventory pressure, increasing consumption, and good social and ecological environmental protection benefits
- Summary
- Abstract
- Description
- Claims
- Application Information
AI Technical Summary
Problems solved by technology
Method used
Image
Examples
Embodiment 1
[0014] (1) After washing, separating, and demedicating the phosphorous tailings sample, separate out the slime below 20 μm (the slime below 20 μm is called raw material 1) and the slime above 20 μm, and the yield of +20 μm is 85%, and it is dried for use ;
[0015] (2) For the part above 20 μm, adopt the technological process of first flotation magnesium (one coarse one fine one sweep) and then flotation phosphorus (one rough one fine) to divide the phosphorus tailings into three parts: magnesium-calcium component, Phosphorous component, silicon component (silicon component is the raw material 2); the selected magnesium-calcium component and phosphorus component are used for other purposes, and the silicon component is combined with some magnesium-calcium products and ultra-fine-grained phosphorus tail The ore is used in the preparation of phosphorous tailings-based cementitious materials. Among them, magnesium roughing agent system: sulfuric acid 6000g / t, collector TG 1500g / ...
Embodiment 2
[0032] Phosphorus tailings are treated by water analysis method, and the yield of +20μm is 80%. The flotation test is carried out on this product, and the technological process is to first flotation magnesium (one rough, one fine, one sweep) and then flotation phosphorus (one rough, one fine). Among them, magnesium roughing agent system: sulfuric acid 7000g / t, collector TG 2000g / t; magnesium selective agent system: collector TG 800g / t; magnesium sweeping agent system: sulfuric acid 800g / t, collector TG600g / t t. Phosphorus roughing agent system: sodium carbonate 10000g / t, collector TP 2500g / t; phosphorus sweeping agent system: sodium carbonate 1000g / t. The calcium and magnesium component yield was 60%, the MgO grade was 26.4%, and the CaO grade was 38.04%; the phosphorus component yield was 8%, and the P 2 o 5 The grade is 19.8%; the silicon component yield is 32%. The magnesium-calcium component was calcined at 900°C for 1.5h, then hydrated and refined, and the lower-purity...
Embodiment 3
[0046] The prepared cementitious material and ISO standard sand are mixed evenly in a cement mortar mixer according to the cement mortar ratio of 1:3, and then put into the mold. Three sets of tests are done for each formula, and then placed in a constant temperature and humidity curing box for curing. time. Determination of relative strength performance at a certain age.
[0047] Table 12 P1, P2 cementitious material flexural compressive strength
[0048]
PUM
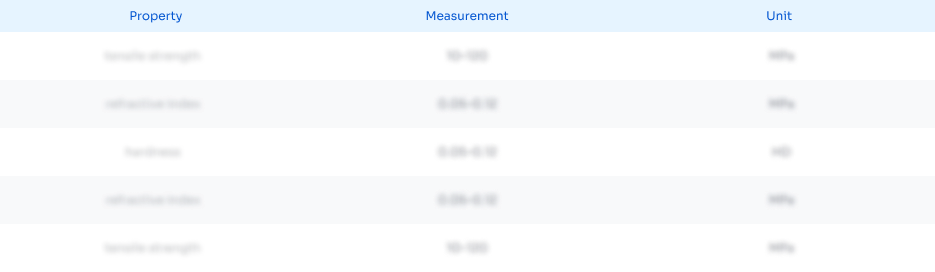
Abstract
Description
Claims
Application Information

- R&D Engineer
- R&D Manager
- IP Professional
- Industry Leading Data Capabilities
- Powerful AI technology
- Patent DNA Extraction
Browse by: Latest US Patents, China's latest patents, Technical Efficacy Thesaurus, Application Domain, Technology Topic, Popular Technical Reports.
© 2024 PatSnap. All rights reserved.Legal|Privacy policy|Modern Slavery Act Transparency Statement|Sitemap|About US| Contact US: help@patsnap.com