Strong-basicity graphene composite ion exchange resin material and preparation method thereof
A composite technology of ion exchange resin and graphene, applied in the direction of ion exchange, anion exchange, organic anion exchanger, etc., can solve the problems of limited performance improvement of composite materials, uneven dispersion of graphene, easy agglomeration, etc., and achieve good scattered effect
- Summary
- Abstract
- Description
- Claims
- Application Information
AI Technical Summary
Problems solved by technology
Method used
Image
Examples
Embodiment 1
[0067] Graphene oxide was prepared by the Hummers method, ultrasonically dispersed into 200ml of 1mg / ml aqueous dispersion, 1mmol / L sodium hydroxide solution was added to adjust the pH to 10, 0.4g tetrabutylammonium bromide and 2.0g p-chloride were added Methyl styrene was stirred and reacted in an oil bath at 98°C for 3h. After the reaction is complete, cool to room temperature, add 200ml of chloroform and shake well, then let stand to separate the organic phase and filter to remove insoluble matter. After the mixed solution was concentrated to 10ml, the graphene-p-methylstyrene compound was obtained after washing with ethanol and drying.
[0068] Dissolve 1.3g of polyvinyl alcohol in 130ml of deionized aqueous solution, and disperse evenly by ultrasonic. Take 62.5g of p-chloromethylstyrene, 5.8g of divinylbenzene, 0.9g of benzoyl peroxide and 0.81g of graphene-p-methylstyrene compound, ultrasonically disperse for 30min and then let it stand for 1h, uniform black dispersion ...
Embodiment 2
[0072] Graphene oxide was prepared by the Hummers method, ultrasonically dispersed into 200ml of 1mg / ml aqueous dispersion, 1mmol / L sodium hydroxide solution was added to adjust the pH to 10, 0.4g tetrabutylammonium bromide and 2.0g p-chloride were added Methyl styrene was stirred and reacted in an oil bath at 98°C for 3h. After the reaction is complete, cool down to room temperature, add 200ml of carbon tetrachloride to shake well, then stand still to separate the organic phase and filter to remove insoluble matter. After the mixed solution was concentrated to 10ml, the graphene-p-methylstyrene compound was obtained after washing with ethanol and drying.
[0073] Dissolve 1.3g of polyvinyl alcohol in 130ml of deionized aqueous solution, and disperse evenly by ultrasonic. Take 60.6g of p-chloromethylstyrene, 5.9g of divinylbenzene, 1.1g of benzoyl peroxide and 2.4g of graphene-p-methylstyrene compound, ultrasonically disperse for 30min and then let it stand for 1h, uniform bl...
Embodiment 3
[0077] Graphene oxide was prepared by the Hummers method, ultrasonically dispersed into 200ml of 1mg / ml aqueous dispersion, 1mmol / L sodium hydroxide solution was added to adjust the pH to 10, 0.4g tetrabutylammonium bromide and 2.0g p-chloride were added Methyl styrene was stirred and reacted in an oil bath at 98°C for 3h. After the reaction is complete, cool to room temperature, add 200ml of chloroform and shake well, then let stand to separate the organic phase and filter to remove insoluble matter. After the mixed solution was concentrated to 10ml, the graphene-p-methylstyrene compound was obtained after washing with ethanol and drying.
[0078] Dissolve 1.3g of gelatin in 130ml of deionized water, and disperse evenly by ultrasonic. Take 59.5g of p-chloromethylstyrene, 5.4g of divinylbenzene, 1g of benzoyl peroxide and 4.1g of graphene-p-methylstyrene compound, ultrasonically disperse for 30min and then let it stand for 1h, a uniform black dispersion can be seen No precip...
PUM
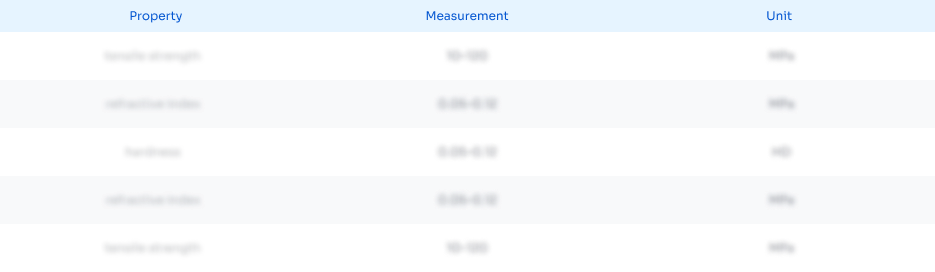
Abstract
Description
Claims
Application Information

- R&D Engineer
- R&D Manager
- IP Professional
- Industry Leading Data Capabilities
- Powerful AI technology
- Patent DNA Extraction
Browse by: Latest US Patents, China's latest patents, Technical Efficacy Thesaurus, Application Domain, Technology Topic, Popular Technical Reports.
© 2024 PatSnap. All rights reserved.Legal|Privacy policy|Modern Slavery Act Transparency Statement|Sitemap|About US| Contact US: help@patsnap.com