Heat treatment method of high-hardness and high-impact-toughness alloy material
A heat treatment method and technology of alloy materials, which are applied in the field of heat treatment of alloy materials with high hardness and high impact toughness, can solve the problems that it is difficult to meet the technical index requirements of high-quality hobs and the service life of hobs is not long, so as to achieve good toughness and prolong The effect of service life and high hardness
- Summary
- Abstract
- Description
- Claims
- Application Information
AI Technical Summary
Problems solved by technology
Method used
Image
Examples
Embodiment 1
[0024] Example 1. A heat treatment method for high-hardness and high-impact-toughness alloy materials. After austenitizing the material, it is put into quenching oil for quenching treatment; Put the material into water or oil at room temperature and cool down.
[0025] Specifically, the austenitizing treatment is: keeping the material at a holding temperature of 900-1000° C. for 30-60 minutes. This treatment not only ensures that the alloying elements in the material are fully dissolved, but also does not cause the grains to grow.
[0026] Specifically, the holding temperature during the austenitizing treatment is 950°C.
[0027] Specifically, the quenching treatment is: keeping the temperature in quenching oil at 50-150° C. for 15-40 seconds at a constant temperature. This treatment can partially transform the austenite in the material, so that the structure after the quenching treatment is quenched martensite + about 10% metastable austenite.
[0028] Specifically, the q...
PUM
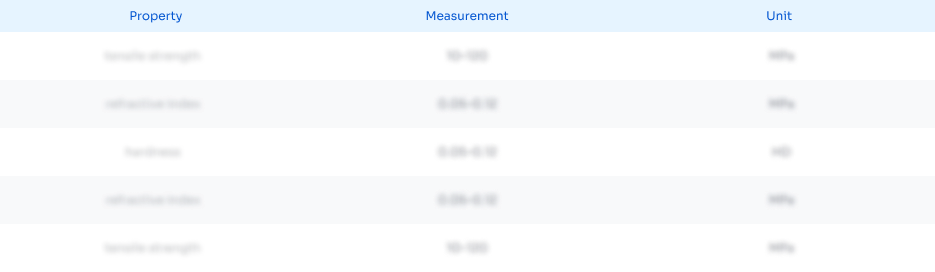
Abstract
Description
Claims
Application Information

- R&D
- Intellectual Property
- Life Sciences
- Materials
- Tech Scout
- Unparalleled Data Quality
- Higher Quality Content
- 60% Fewer Hallucinations
Browse by: Latest US Patents, China's latest patents, Technical Efficacy Thesaurus, Application Domain, Technology Topic, Popular Technical Reports.
© 2025 PatSnap. All rights reserved.Legal|Privacy policy|Modern Slavery Act Transparency Statement|Sitemap|About US| Contact US: help@patsnap.com