A strontium zirconate-based composite ceramic thermal barrier coating material with low thermal conductivity and high phase stability, its preparation method and application
A technology of composite ceramic and thermal barrier coating, applied in the field of thermal barrier coating, can solve problems such as unfavorable materials of thermal barrier coating ceramic layer, and achieve the effects of low price, low thermal conductivity and inhibiting phase transformation
- Summary
- Abstract
- Description
- Claims
- Application Information
AI Technical Summary
Problems solved by technology
Method used
Image
Examples
Embodiment 1
[0031] Preparation SR 0.9 (Zr 0.9 YB 0.05 GD 0.05 ) O 2.85 Ceramic powder (ie: a is GD, x = 0.9)
[0032] SRCO 3 , Zro 2 YB 2 O 3 GD 2 O 3 The powder is raw material, and the quality of each component accounts for the total mass of the material: SRCO, respectively. 3 : 50.57%, Zro 2 : 42.23%, YB 2 O 3 : 3.75%, GD 2 O 3 : 3.45%.
[0033] Weigh the above raw materials, grind in the mortar, the medium is anhydrous ethanol (ethanol is easy to volatilize, there is no need to dry after the grinding, if it is dried with deionized water, after drying, it is necessary to grind again.). Then calcine at 1400 ° C for 24 h, resulting in SR 0.9 (Zr 0.9 YB 0.05 GD 0.05 ) O 2.85 B - zirconate - based composite ceramic thermal barrier coating material.
[0034] The above zirconium-based composite ceramic thermal barrier layer material powder was placed in an agate mortar to grind 1 h, and the amount of a mold was placed in a mold having a diameter of 15 mm, and the molded ceramic green body was pr...
Embodiment 2
[0037] Preparation SR 0.8 (Zr 0.9 YB 0.05 GD 0.05 ) O 2.75 Ceramic powder (ie: a is GD, x = 0.8)
[0038] SRCO 3 , Zro 2 YB 2 O 3 GD 2 O 3 The powder is raw material, and the quality of each component accounts for the total mass of the material: SRCO, respectively. 3 : 47.63%, Zro 2 : 44.74%, YB 2 O 3 : 3.97%, GD 2 O 3 : 3.66%.
[0039] Weigh the above raw materials, grind in the mortar, the medium is anhydrous ethanol, then calcined at 1400 ° C for 24 h, resulting in SR 0.8 (Zr 0.9 YB 0.05 GD 0.05 ) O 2.75 B - zirconate - based composite ceramic thermal barrier coating material.
[0040] The above zirconium-based composite ceramic thermal barrier layer material powder was placed in an agate mortar to grind 1 h, and the amount of a mold was placed in a mold having a diameter of 15 mm, and the molded ceramic green body was pre-compressed at a pressure of 20 MPa. At 30 MPa pressure, the water and the like are subjected to the obtained ceramic blank volume in the high temperature fur...
Embodiment 3
[0043] Preparation SR 0.7 (Zr 0.9 YB 0.05 GD 0.05 ) O 2.65 Ceramic powder (ie: a is GD, x = 0.7)
[0044] SRCO 3 , Zro 2 YB 2 O 3 GD 2 O 3 The powder is raw material, and the quality of each component accounts for the total mass of the material: SRCO, respectively. 3 : 44.32%, Zro 2 : 47.57%, YB 2 O 3 : 4.22%, GD 2 O 3 : 3.89%.
[0045] Weigh the above raw materials, grind in the mortar, the medium is anhydrous ethanol, then calcined at 1400 ° C for 24 h, resulting in SR 0.7 (Zr 0.9 YB 0.05 GD 0.05 ) O 2.65 B - zirconate - based composite ceramic thermal barrier coating material.
[0046] The above zirconium-based composite ceramic thermal barrier layer material powder was placed in an agate mortar to grind 1 h, and the amount of a mold was placed in a mold having a diameter of 15 mm, and the molded ceramic green body was pre-compressed at a pressure of 20 MPa. At 30 MPa pressure, the water and the like are subjected to the obtained ceramic blank volume in the high temperature fur...
PUM
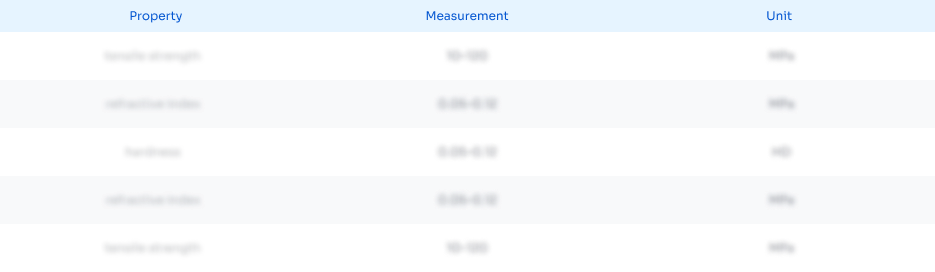
Abstract
Description
Claims
Application Information

- Generate Ideas
- Intellectual Property
- Life Sciences
- Materials
- Tech Scout
- Unparalleled Data Quality
- Higher Quality Content
- 60% Fewer Hallucinations
Browse by: Latest US Patents, China's latest patents, Technical Efficacy Thesaurus, Application Domain, Technology Topic, Popular Technical Reports.
© 2025 PatSnap. All rights reserved.Legal|Privacy policy|Modern Slavery Act Transparency Statement|Sitemap|About US| Contact US: help@patsnap.com