High-temperature corrosion prediction and service life evaluation method for boiler water wall
A technology for high-temperature corrosion and life assessment, applied in combustion methods, weather resistance/light resistance/corrosion resistance, measuring devices, etc. Accuracy, assessing the effect of accurate results
- Summary
- Abstract
- Description
- Claims
- Application Information
AI Technical Summary
Problems solved by technology
Method used
Image
Examples
specific Embodiment 1
[0026] to combine figure 1 , the present invention proposes a method for predicting high temperature corrosion of boiler water wall and evaluating its life, comprising the following steps:
[0027] Step 1. Establish and simplify the high temperature corrosion reaction model of the water wall, determine the main chemical reactions of the corrosion reaction and the main factors affecting the reaction rate.
[0028] Step 2, according to the reaction model established in step 1, combined with the reaction mechanism of the corrosion reaction, determine H 2 Diffusion rate and chemical reaction rate of S at the reaction interface.
[0029] Step 3, calculate the change of metal thickness during the corrosion process by the principle of conservation, and establish the functional relationship between the physical quantity of corrosion and time.
[0030] Step 4, according to the safe operation requirements of the water wall of the power plant boiler, establish the corrosion life evalua...
specific Embodiment 2
[0073] For a 630MW supercritical four-corner tangential circle coal-fired boiler, according to the measured data of its benchmark working conditions, H in the corrosive atmosphere 2 The concentration of S gas is selected as 180mg / Nm 3 , 120mg / Nm 3 , 60mg / Nm 3 ; The temperature of the wall surface of the water-cooled wall is selected from the temperature of the pipe wall under full-load operation, and its value is 723K; the initial thickness of the metal of the water-cooled wall is 0.0075m.
[0074] Substituting the above parameters, the functional relationship expression of the average metal corrosion rate X and time t can be obtained:
[0075] t=2.41×10 7 x 2 +0.418×10 7 X C o =180mg / Nm 3
[0076] t=3.61×10 7 x 2 +0.628×10 7 X C o =120mg / Nm 3
[0077] t=7.23×10 7 x 2 +1.26×10 7 X C o =60mg / Nm 3
[0078] At the same time, combined with the relevant provisions of boiler design specifications and supervision regulations, for conservative considerations, the m...
PUM
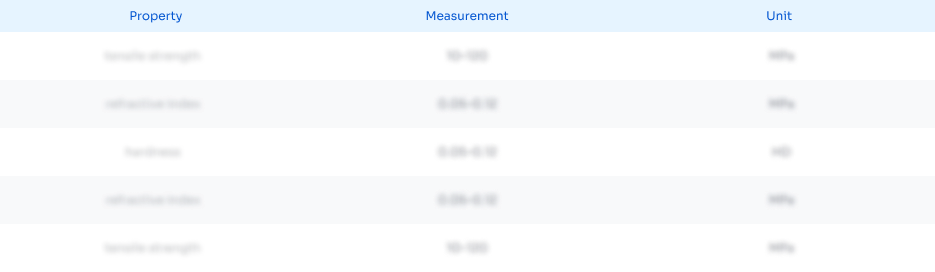
Abstract
Description
Claims
Application Information

- R&D
- Intellectual Property
- Life Sciences
- Materials
- Tech Scout
- Unparalleled Data Quality
- Higher Quality Content
- 60% Fewer Hallucinations
Browse by: Latest US Patents, China's latest patents, Technical Efficacy Thesaurus, Application Domain, Technology Topic, Popular Technical Reports.
© 2025 PatSnap. All rights reserved.Legal|Privacy policy|Modern Slavery Act Transparency Statement|Sitemap|About US| Contact US: help@patsnap.com