Method for producing cupronickel alloy round ingot
A production method and alloy technology, applied in the field of production of cupronickel alloy round ingots, can solve the problems of increased factors affecting the quality of round ingots, unfavorable quality control of round ingots, and large consumption of liquid metal covering agents, so as to eliminate structural defects such as pores , stabilize the quality of liquid metal, and improve the effect of ingot quality control
- Summary
- Abstract
- Description
- Claims
- Application Information
AI Technical Summary
Problems solved by technology
Method used
Image
Examples
Embodiment 1
[0026] Production of a cupronickel alloy round ingot with a nickel content of 4.4%-5%. The total amount of alloy is 4000kg, wherein the proportion of new metal is 50%, and the proportion of process returned material is 50%. Add 45% electrolytic copper and 5% electrolytic nickel into the furnace for melting, add 50% process return material after all the materials are melted, and add charcoal on the metal surface. The amount of charcoal is 6kg per ton of alloy . After all the metal materials are completely melted, the temperature of the liquid metal is raised to 1280-1300°C. Use a slag removal tool to clean up all the scum on the surface of the liquid metal. Evenly sprinkle a layer of cryolite on the surface of the liquid metal, and the amount of cryolite added is 4.8kg. Then immediately add the remaining 9kg of charcoal to the surface of the liquid metal, and cover it evenly to ensure that the liquid metal does not leak. Sampling is carried out to analyze the content of che...
Embodiment 2
[0028] Produce a cupronickel alloy round ingot with a nickel content of 10% to 11%, an iron content of 1.5% to 1.8%, and a manganese content of 0.5% to 1%. The total amount of alloy is 4000kg, wherein the proportion of new metal is 50%, and the proportion of process returned material is 50%. Add 43.5% electrolytic copper, 10.75% electrolytic nickel, and 0.75% iron into the furnace for melting. After all the materials are melted, add 50% of the process return material, and add charcoal on the metal surface. The amount of charcoal 6kg per ton of alloy. After all the metal materials are completely melted, the temperature of the liquid metal is raised to 1280-1300°C. Use a slag removal tool to clean up all the scum on the surface of the liquid metal. Add 0.45% electrolytic manganese, and evenly sprinkle a layer of cryolite on the liquid metal surface. The addition amount of cryolite is 4.8kg. Then immediately add the remaining 9kg of charcoal to the surface of the liquid metal...
Embodiment 3
[0030] Produce a cupronickel alloy round ingot with a nickel content of 30% to 31.5%, an iron content of 0.5% to 1%, and a manganese content of 0.5% to 1.2%. The total amount of alloy is 4000kg, wherein the proportion of new metal is 50%, and the proportion of process returned material is 50%. Add 33.5% electrolytic copper, 16% electrolytic nickel, and 0.5% iron into the furnace for melting, add 50% of the process return material after all the materials are melted, and add charcoal on the metal surface. The amount of charcoal 6kg per ton of alloy. After all the metal materials are completely melted, the temperature of the liquid metal is raised to 1280-1300°C. Use a slag removal tool to clean up all the scum on the surface of the liquid metal. Add 0.45% electrolytic manganese, and evenly sprinkle a layer of cryolite on the liquid metal surface. The addition amount of cryolite is 4.8kg. Then immediately add the remaining 9kg of charcoal to the surface of the liquid metal, a...
PUM
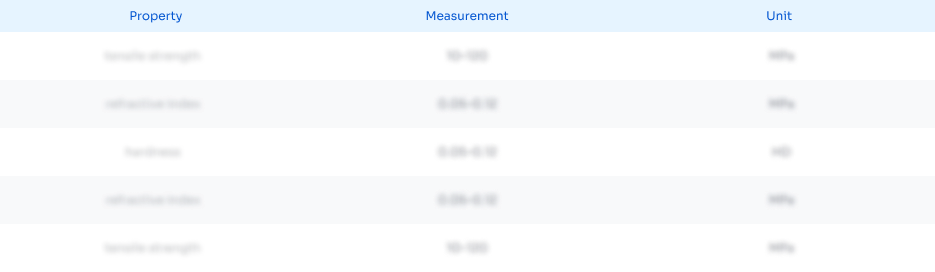
Abstract
Description
Claims
Application Information

- Generate Ideas
- Intellectual Property
- Life Sciences
- Materials
- Tech Scout
- Unparalleled Data Quality
- Higher Quality Content
- 60% Fewer Hallucinations
Browse by: Latest US Patents, China's latest patents, Technical Efficacy Thesaurus, Application Domain, Technology Topic, Popular Technical Reports.
© 2025 PatSnap. All rights reserved.Legal|Privacy policy|Modern Slavery Act Transparency Statement|Sitemap|About US| Contact US: help@patsnap.com