Method and device for manufacturing fully drawn yarn/pre-oriented yarn stranding composite yarn by one-step process
A technology of full-drawn yarn and pre-oriented yarn, which is applied in the direction of spinneret assembly, filament generation, textiles and papermaking, etc. The long production cycle of stretched/pre-oriented yarn plied composite yarn and the inability to improve the competitiveness of production enterprises have achieved the effects of eliminating quality defects, increasing output and production efficiency, and reliable product quality
- Summary
- Abstract
- Description
- Claims
- Application Information
AI Technical Summary
Problems solved by technology
Method used
Image
Examples
Embodiment Construction
[0029] As shown in Figure 4, this one-step method of manufacturing full-drawn yarn / pre-oriented yarn plied composite yarn can use the existing FDY filament equipment, which is a domestic double metering pump with 16 spinneret structures. The spinneret has a structure of two bundles of filaments on one plate, and 16 spinnerettes in 8 components of two metering pumps co-extrude 32 bundles of filaments. A pair of cold godet rollers are added to the FDY filament equipment, and 16 network equipment and winding devices are installed after the cold godet rollers and hot guide rollers. The two heat guide rolls are a combination structure of a large-diameter roll and a small-diameter roll. The large-diameter roll is a high-speed heating roll, and the small-diameter roll is a high-speed splitting roll. The two heat guide rolls are respectively arranged in an incubator.
[0030] Using the above-mentioned FDY filament modification equipment, the 16 bundles of filaments behind the spinning...
PUM
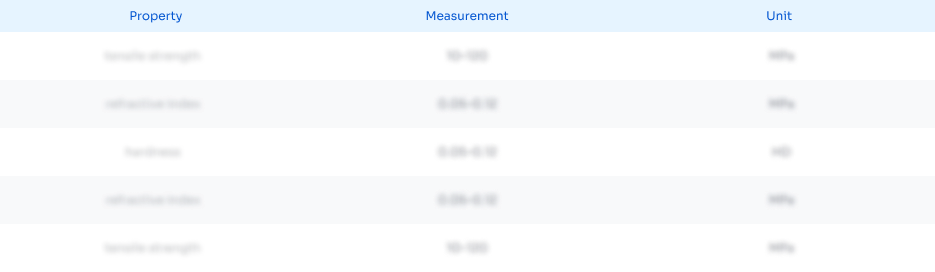
Abstract
Description
Claims
Application Information

- R&D
- Intellectual Property
- Life Sciences
- Materials
- Tech Scout
- Unparalleled Data Quality
- Higher Quality Content
- 60% Fewer Hallucinations
Browse by: Latest US Patents, China's latest patents, Technical Efficacy Thesaurus, Application Domain, Technology Topic, Popular Technical Reports.
© 2025 PatSnap. All rights reserved.Legal|Privacy policy|Modern Slavery Act Transparency Statement|Sitemap|About US| Contact US: help@patsnap.com