Method and system for energy-saving separation of DCB-NMP mixture
A technology of DCB-NMP and separation method, applied in the field of PPS device and resource recovery, which can solve the problems of high cost, unreasonable energy utilization, large amount of heat transfer oil, etc.
- Summary
- Abstract
- Description
- Claims
- Application Information
AI Technical Summary
Problems solved by technology
Method used
Image
Examples
Embodiment 3
[0059] like figure 2 As shown, a DCB-NMP mixture double-effect rectification separation system adopts a high-pressure dehydration tower and a low-pressure dehydration tower in parallel, including a fractionation tower 1, a fractionation tower condenser 2, a phase separation tank 3, and a fractionation tower reboiler 9 , low pressure dehydration tower 4, low pressure dehydration tower condenser 5, first low pressure dehydration tower reboiler 10, second low pressure dehydration tower reboiler 11, high pressure dehydration tower 6, first high pressure dehydration tower reboiler 12, rectification Tower 7, rectifying tower reboiler 14; The tower top gas outlet of described fractionating tower 1 is connected with the inlet of phase-separating tank 3 through fractionating tower condenser 2, and the water phase outlet of phase-separating tank 3 is refluxed with fractionating tower 1 The liquid inlet is connected, the oil phase outlet of the phase separation tank 3 is used to extract...
Embodiment 2
[0066] The DCB-NMP mixture (same as Example 1) is separated and recovered based on the DCB-NMP mixture double-effect rectification separation system of Example 1, including the following steps:
[0067] Step (1), fractionation treatment: the DCB-NMP mixture is sent to fractionation tower 1 (the number of theoretical plates is 52), the operating pressure of the fractionation tower is controlled to be 0.13MPa, the operating temperature is 80°C, and the reflux ratio is 2.1; The tower condenser 2 enters the phase separation tank 2, and the non-condensable gas (H 2 S) Discharge from the top of the tank, absorb H with water or lye 2 S, the oil phase is extracted from the oil phase outlet to obtain DCB with a purity of 99.8%, the DCB yield is 99.55%, and the water phase is discharged from the water phase outlet and refluxed to the fractionation tower;
[0068] Step (2), double-effect rectification dehydration: step (1) the liquid phase extracted from the fractionating tower still is...
Embodiment 4
[0076] The DCB-NMP mixture (same as Example 1) is separated and recovered based on the DCB-NMP mixture double-effect rectification separation system of Example 1, including the following steps:
[0077] Step (1), fractionation treatment: the DCB-NMP mixture is sent to fractionation tower 1 (the number of theoretical plates is 47), the operating pressure of the fractionation tower is controlled to be 0.14MPa, the operating temperature is 90°C, and the reflux ratio is 2.3; the gas phase at the top of the tower is fractionated. The tower condenser 2 enters the phase separation tank 2, and the non-condensable gas (H 2 S) Discharge from the top of the tank, absorb H with water or lye 2 S, the oil phase is extracted from the oil phase outlet to obtain DCB with a purity of 99.8%, the DCB yield is 99.55%, and the water phase is discharged from the water phase outlet and refluxed to the fractionation tower;
[0078] Step (2), double-effect rectification and dehydration: the liquid pha...
PUM
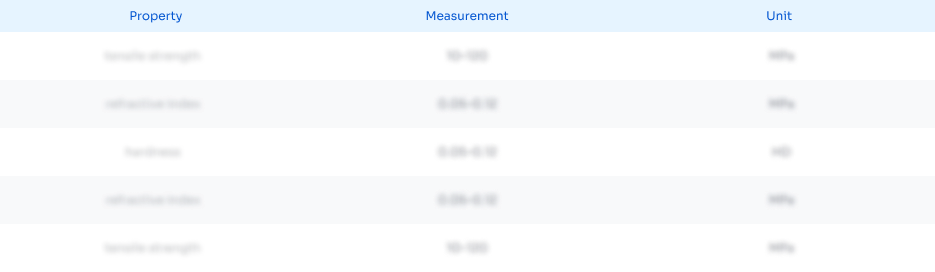
Abstract
Description
Claims
Application Information

- R&D
- Intellectual Property
- Life Sciences
- Materials
- Tech Scout
- Unparalleled Data Quality
- Higher Quality Content
- 60% Fewer Hallucinations
Browse by: Latest US Patents, China's latest patents, Technical Efficacy Thesaurus, Application Domain, Technology Topic, Popular Technical Reports.
© 2025 PatSnap. All rights reserved.Legal|Privacy policy|Modern Slavery Act Transparency Statement|Sitemap|About US| Contact US: help@patsnap.com