Method for producing particle board from chrome-containing leather shavings
A technology of particle board and chrome leather shavings, which is applied in the field of chromium-containing leather shavings to make particle boards, can solve the problems of inability to realize resource utilization of chromium-containing leather shavings, market capacity limitations, etc., and increase benzene rings, carbon sources, and processing costs Low, easy to collect effect
- Summary
- Abstract
- Description
- Claims
- Application Information
AI Technical Summary
Problems solved by technology
Method used
Image
Examples
preparation example 1
[0038] (1) Mix 60g of blue leather shavings, 1g of oxalic acid and 90g of water evenly, stir at 35°C for 1h; then adjust the pH to 4, add 0.4g of sodium citrate dihydrate, stir for 30min, and dry the obtained blue chrome shavings Dry;
[0039] (2), all the blue leather shavings of step (1), polyurethane glue 700w13.2g, nitrogen-phosphorus flame retardant 2g, nitrile rubber toughening agent 1g, sodium p-vinylbenzenesulfonate toughening synergist 0.2g , flame retardant synthetic fatliquoring agent 5g, water expansion inhibitor 0.9g, n-butyl benzoic acid 0.7g, water-based transparent waterproofing agent WP01 0.2g (Hangzhou Ruijiang New Material Technology Co., Ltd.) mixed evenly, and placed at room temperature for 30min , put it on a 4mm thick mold, the pressure of the flat vulcanizing machine is 10Mpa, the temperature is 90°C, heat and pressurize in the flat vulcanizing machine, the processing time is 30min, the obtained plate is placed in a constant temperature and humidity box...
preparation example 2
[0045] (1) Mix 60g of blue leather shavings, 3g of oxalic acid and 90g of water evenly, stir at 40°C for 2h; then adjust the pH to 4.5, add 0.7g of sodium citrate dihydrate, stir for 60min, and dry the obtained blue chrome shavings Dry;
[0046] (2), all blue leather shavings of step (1), universal glue 899 (Guangdong Gujia Industrial Co., Ltd.) 21.1g, nitrogen-phosphorus flame retardant 8g, polyvinyl butyral toughening agent 3g, malonic acid ring (sub- ) isopropyl ester toughening synergist 0.5g, flame retardant synthetic fatliquoring agent 7g, water swelling inhibitor 2.1g, trimethylolpropane 2.5g, water-based transparent waterproofing agent WP01 is 0.6g (Hangzhou Ruijiang New Material Technology Co., Ltd.) mixed evenly, placed at room temperature for 60 minutes, put it on a 4mm thick mold, the pressure of the flat vulcanizer is 12Mpa, the temperature is 100°C, heated and pressurized in the flat vulcanizer, the processing time is 60min, and the obtained plate is placed in I...
preparation example 3
[0052] (1) Mix 60g of blue leather shavings, 2g of oxalic acid and 90g of water evenly, and stir at 40°C for 1.5h; then adjust the pH to 4, add 0.55g of sodium citrate dihydrate, stir for 45min, and mix the obtained blue chrome shavings drying;
[0053] (2), all the blue leather scraps in step (1), polyurethane glue 700w17.2g, nitrogen phosphorus flame retardant 5g, polyvinyl butyral toughening agent 2g, 3,4-dimethylaniline toughening synergist 0.35g, 6g of flame-retardant synthetic fatliquoring agent, 1.5g of water swelling inhibitor, 1.6g of cinnamic amide, 0.4g of water-based transparent waterproofing agent WP01 (Hangzhou Ruijiang New Material Technology Co., Ltd.), mix well, and place at room temperature for 45min. Put it on a 4mm thick mold, the pressure of the flat vulcanizer is 11Mpa, the temperature is 95°C, heat and pressurize in the flat vulcanizer, the processing time is 45min, put the obtained plate in a constant temperature and humidity box for 48h, control the te...
PUM
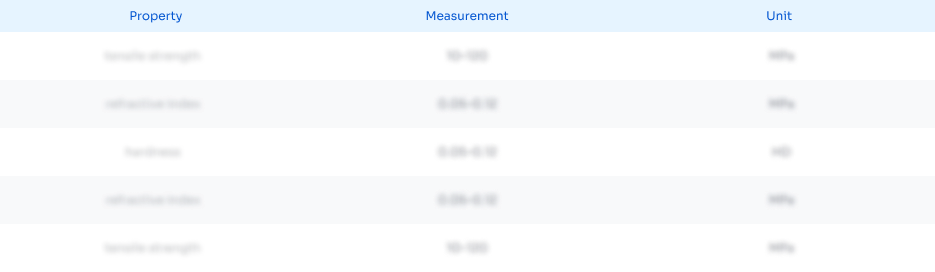
Abstract
Description
Claims
Application Information

- R&D
- Intellectual Property
- Life Sciences
- Materials
- Tech Scout
- Unparalleled Data Quality
- Higher Quality Content
- 60% Fewer Hallucinations
Browse by: Latest US Patents, China's latest patents, Technical Efficacy Thesaurus, Application Domain, Technology Topic, Popular Technical Reports.
© 2025 PatSnap. All rights reserved.Legal|Privacy policy|Modern Slavery Act Transparency Statement|Sitemap|About US| Contact US: help@patsnap.com