A highly heat-resistant corrosion-resistant coating sealing agent
A sealing agent, high heat-resistant technology, applied in the direction of coating, surface reaction electrolytic coating, electrolytic coating, etc., can solve the problems of poor high temperature and thermal corrosion resistance, reduce surface tension, improve high temperature resistance, strengthen sealing The effect of the blocking effect
- Summary
- Abstract
- Description
- Claims
- Application Information
AI Technical Summary
Problems solved by technology
Method used
Examples
preparation example Construction
[0034] The preparation method of composite sealing base material, comprises the steps:
[0035] (1) At 70-85°C, mix basalt and hydrochloric acid solution with a mass fraction of 12% according to the mass ratio of 1:12-20, keep it warm at 400-700r / min for 1-3h, filter while it is hot, and collect the filter residue according to the mass ratio 1:10~15, add periodic acid solution with a concentration of 1mol / L and mix, keep warm at 80~90°C for 45~60min, cool naturally to room temperature, filter, collect the filter cake and wash it with water for 2~4 times, then move to an oven at 65°C Dry at ~80°C for 3~5h, collect the dried matter, and take 15~30 parts of dried matter, 2~5 parts of vinyltriethoxysilane, and 3~7 parts of hexadecyltrimethyl bromide Ammonium chloride and 6-10 parts of absolute ethanol are ground in a mortar for 3-5 hours, and the abrasive is collected;
[0036] (2) In parts by weight, take 30~40 parts of abrasive, 17~23 parts of polyvinyl alcohol, 15~20 parts of ...
Embodiment 1
[0040] Additives: At 30°C, take fatty alcohol polyoxyethylene ether and mix it with triethanolamine at a mass ratio of 3:1 for 30 minutes to obtain a mixture. Take the mixture and add hydroxyethyl cellulose and epoxy resin at a mass ratio of 10:1:2 for mixing. Additives are obtained.
[0041] Reagent A: Mix sodium metaaluminate, urea, and water in a mass ratio of 1:2:30 to obtain reagent A.
[0042] Reagent B: In parts by weight, take 5 parts of magnesium nitrate, 2 parts of aluminum nitrate, 6 parts of zinc nitrate, and 150 parts of water and mix to obtain a mixed salt solution. Take the mixed salt solution and add carbonamide to mix at a mass ratio of 20:1. That is, reagent B is obtained.
[0043] Auxiliary agent: Mix potassium thiocyanate and sodium citrate at a mass ratio of 3:1 to obtain the auxiliary agent.
[0044] Dispersant: Mix vinyl bis stearic acid amide and polyacrylamide at a mass ratio of 2:1 to obtain a dispersant.
[0045] Defoamer: mix polyoxypropyl polyox...
Embodiment 2
[0053] Additives: At 40°C, take fatty alcohol polyoxyethylene ether and mix it with triethanolamine at a mass ratio of 7:1 for 60 minutes to obtain a mixture. Take the mixture and mix it with hydroxyethyl cellulose and epoxy resin at a mass ratio of 10:1:5. Additives are obtained.
[0054] Reagent A: Mix sodium metaaluminate, urea, and water at a mass ratio of 1:4:50 to obtain reagent A.
[0055] Reagent B: In parts by weight, take 8 parts of magnesium nitrate, 5 parts of aluminum nitrate, 10 parts of zinc nitrate, and 200 parts of water and mix to obtain a mixed salt solution. Take the mixed salt solution and add carbonamide to mix at a mass ratio of 30:1. That is, reagent B is obtained.
[0056] Auxiliary: Mix potassium thiocyanate and sodium citrate at a mass ratio of 6:1 to obtain the auxiliary.
[0057] Dispersant: Mix vinyl bis stearic acid amide and polyacrylamide at a mass ratio of 5:1 to obtain a dispersant.
[0058] Defoaming agent: Mix polyoxypropyl polyoxyethyl ...
PUM
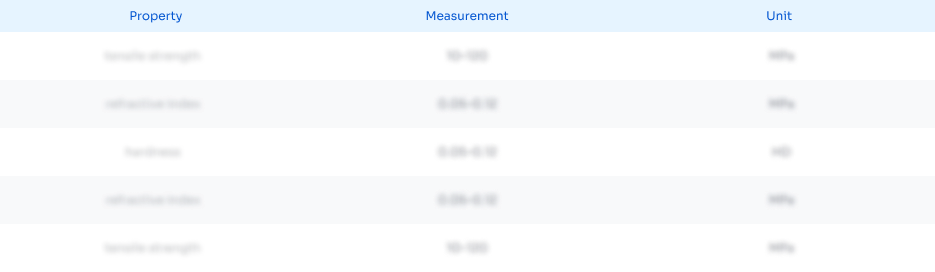
Abstract
Description
Claims
Application Information

- R&D
- Intellectual Property
- Life Sciences
- Materials
- Tech Scout
- Unparalleled Data Quality
- Higher Quality Content
- 60% Fewer Hallucinations
Browse by: Latest US Patents, China's latest patents, Technical Efficacy Thesaurus, Application Domain, Technology Topic, Popular Technical Reports.
© 2025 PatSnap. All rights reserved.Legal|Privacy policy|Modern Slavery Act Transparency Statement|Sitemap|About US| Contact US: help@patsnap.com