Wet-process groove type black silicon texturing method
A grooved, black silicon technology that can be used in final product manufacturing, sustainable manufacturing/processing, semiconductor/solid-state device manufacturing, etc., to solve problems such as uneven texture of crystalline silicon wafers
- Summary
- Abstract
- Description
- Claims
- Application Information
AI Technical Summary
Problems solved by technology
Method used
Examples
Embodiment Construction
[0020] In order to make the technical means, creative features, goals and effects achieved by the present invention easy to understand, the present invention will be further described below in conjunction with specific embodiments.
[0021] The additive BT20-A, additive BT20-B and additive BT20-C involved in the present invention are polycrystalline black silicon texturing auxiliary products, which are directly purchased from Shichuang Company, and the specific models are BT20-A, BT20-B and BT20-C.
[0022] A method for making wet-process trough-type black silicon texture, comprising the steps of:
[0023] Step 1. Treat the surface of the crystalline silicon wafer to remove the line marks on the surface of the crystalline silicon wafer, specifically: put the crystalline silicon wafer into the first-level treatment tank, remove the line marks on the surface of the silicon wafer, and obtain the first-level crystalline silicon with a smooth surface Tablets; wherein, the circulat...
PUM
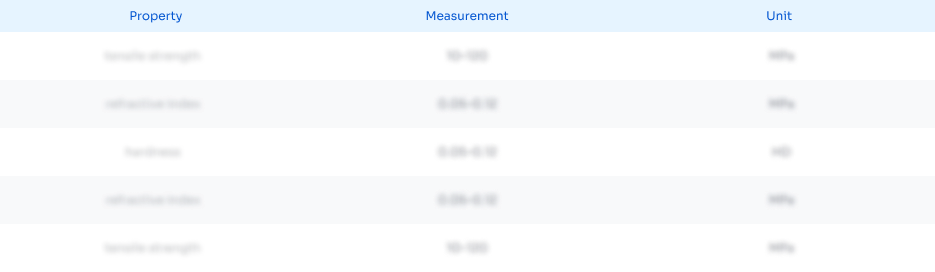
Abstract
Description
Claims
Application Information

- R&D
- Intellectual Property
- Life Sciences
- Materials
- Tech Scout
- Unparalleled Data Quality
- Higher Quality Content
- 60% Fewer Hallucinations
Browse by: Latest US Patents, China's latest patents, Technical Efficacy Thesaurus, Application Domain, Technology Topic, Popular Technical Reports.
© 2025 PatSnap. All rights reserved.Legal|Privacy policy|Modern Slavery Act Transparency Statement|Sitemap|About US| Contact US: help@patsnap.com