Wear-resistant material for casting
A technology of wear-resistant materials and castings, which is applied in the field of wear-resistant materials, can solve the problems of discounted wear-resistant materials, tedious and time-consuming, and limited improvement in the wear-resistant performance of wear-resistant composite materials, so as to improve wear-resistant performance and expand applications range, effect of guaranteed service life
- Summary
- Abstract
- Description
- Claims
- Application Information
AI Technical Summary
Problems solved by technology
Method used
Examples
Embodiment 1
[0015] A wear-resistant material for castings, the material is made of the following components in parts by weight: 10 parts of dextrin powder, 12 parts of polyvinyl alcohol, 12 parts of iron oxide powder, 6 parts of n-butanol, orthophosphoric acid 1 part of sodium, 3 parts of starch paste, 3 parts of lignosulfonic acid, 2 parts of sodium hydroxymethyl cellulose, 2 parts of silica sol, 10 parts of modified graphene, 0.3 parts of iron oxide red powder, 6 parts of hollow glass microspheres , 10 parts of triphenyl phosphite, 10 parts of acrylic modified polyurethane, 10 parts of nano ceramic powder, 2 parts of sodium benzoate, 3 parts of aluminum phosphate, 3 parts of epoxy resin, 2 parts of ethyl acetate, 3 parts of acetylcholine, pentachloro 2 parts of phenol, 2 parts of acetic anhydride, 1 part of p-xylene, 4 parts of copper oxide powder, 3 parts of nano calcium oxide, 2 parts of benzenesulfonic acid, 2 parts of molybdenum disulfide, 2 parts of crystalline silicon oxide, 3 part...
Embodiment 2
[0017] A wear-resistant material for castings, the material is made of the following components in parts by weight: 12 parts of dextrin powder, 14 parts of polyvinyl alcohol, 14 parts of iron oxide powder, 7 parts of n-butanol, orthophosphoric acid 2 parts of sodium, 4 parts of starch paste, 4 parts of lignosulfonic acid, 3 parts of sodium hydroxymethyl cellulose, 4 parts of silica sol, 12 parts of modified graphene, 0.4 parts of iron oxide red powder, 8 parts of hollow glass microspheres , 12 parts of triphenyl phosphite, 15 parts of acrylic modified polyurethane, 12 parts of nano ceramic powder, 4 parts of sodium benzoate, 5 parts of aluminum phosphate, 4 parts of epoxy resin, 4 parts of ethyl acetate, 4 parts of acetylcholine, pentachloro 4 parts of phenol, 4 parts of acetic anhydride, 3 parts of p-xylene, 6 parts of copper oxide powder, 5 parts of nano calcium oxide, 4 parts of benzenesulfonic acid, 4 parts of molybdenum disulfide, 4 parts of crystalline silicon oxide, 5 pa...
Embodiment 3
[0019] A wear-resistant material for castings, the material is made of the following components in parts by weight: 13 parts of dextrin powder, 15 parts of polyvinyl alcohol, 15 parts of iron oxide powder, 8 parts of n-butanol, orthophosphoric acid 3 parts of sodium, 6 parts of starch paste, 6 parts of lignosulfonic acid, 5 parts of sodium hydroxymethyl cellulose, 6 parts of silica sol, 15 parts of modified graphene, 0.6 parts of iron oxide red powder, 9 parts of hollow glass microspheres , 14 parts of triphenyl phosphite, 17 parts of acrylic modified polyurethane, 14 parts of nano ceramic powder, 5 parts of sodium benzoate, 7 parts of aluminum phosphate, 5 parts of epoxy resin, 6 parts of ethyl acetate, 6 parts of acetylcholine, pentachloro 5 parts of phenol, 6 parts of acetic anhydride, 5 parts of p-xylene, 8 parts of copper oxide powder, 7 parts of nano calcium oxide, 5 parts of benzenesulfonic acid, 6 parts of molybdenum disulfide, 5 parts of crystalline silicon oxide, 7 pa...
PUM
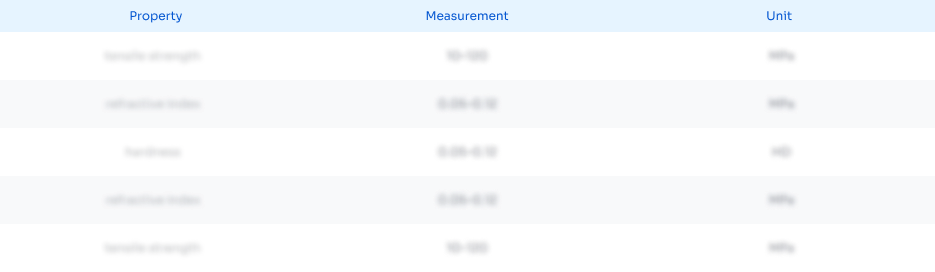
Abstract
Description
Claims
Application Information

- R&D
- Intellectual Property
- Life Sciences
- Materials
- Tech Scout
- Unparalleled Data Quality
- Higher Quality Content
- 60% Fewer Hallucinations
Browse by: Latest US Patents, China's latest patents, Technical Efficacy Thesaurus, Application Domain, Technology Topic, Popular Technical Reports.
© 2025 PatSnap. All rights reserved.Legal|Privacy policy|Modern Slavery Act Transparency Statement|Sitemap|About US| Contact US: help@patsnap.com