High-precision closed-forging technology for forge piece
A high-precision, forging technology, applied in the field of forging processing, can solve problems such as imperfect control of production factors, unsatisfactory product precision control, and large product machining allowances, so as to save mold material consumption, reduce product size problems, and reduce materials. The effect of consumption
- Summary
- Abstract
- Description
- Claims
- Application Information
AI Technical Summary
Problems solved by technology
Method used
Image
Examples
Embodiment 1
[0034] A closed forging process for high-precision forgings, comprising the following process steps:
[0035] 1) Cutting: According to the process requirements, the raw materials are cut to length, and the qualified materials are selected for use;
[0036] 2) Heating: using an intermediate frequency electric furnace, sending the qualified materials in step 1) into the burner for heating at one time to obtain hot materials;
[0037] 3) Roughing: send the hot material to the roughing station of the mechanical pressure forging machine for roughing treatment to obtain roughed parts;
[0038] 4) Forming: send the pier rough piece to the forming station of the mechanical pressure forging machine, perform forming treatment, and obtain the intermediate product of forging with holes;
[0039] 5) Punching: Send the intermediate forging with holes to the punching station of the mechanical press punching machine for punching to obtain the finished forging with round holes.
Embodiment 2
[0041] A forming die applied to the above-mentioned closed forging process of high-precision forgings, such as Figures 1 to 3 As shown, it includes an upper template 1, a lower template 2, a die cavity 3, a lower ejection cylinder 4, a punch assembly 5, a mold assembly 6, and a release aid assembly 7. The punch assembly 5 includes a punch 51 and a sleeve The punch sleeve 52 outside the punch 51, the mold assembly 6 includes a mold 61, a mold sleeve 62 sleeved outside the mold 61, and a pad 63 adapted to the bottom of the inner cavity of the mold 61, and the release aid assembly 7 includes a cross arm 71 , the large load 72 that is sleeved outside the cross arm 71, the vertical suspension 73 that is slidably connected with the large load 72, and the upper ejection cylinder 74 that is connected with the large load 72.
Embodiment 3
[0043] Provide example based on embodiment 1, embodiment 2, as follows:
[0044] 1) Blanking: This process has high requirements on the weight control of raw material blanking, because the follow-up mold has no flash design, and hot die forging is a kind of forging equipment with a bottom dead point. Too much blanking weight exceeding the specified value will lead to If the equipment is boring, the mold and equipment may be damaged. If the weight of the blank is too small or too much, the product will not be filled in the mold and the product will be scrapped. Therefore, the outer diameter of the raw material round steel needs to be inspected, and the error of the outer diameter of the same production batch should be within ±0.3mm, otherwise the weight of the subsequent blanking is likely to be out of tolerance. The blanking equipment adopts CNC circular saw, which can precisely control the length of the blanking to ensure the weight of the blanking, and can ensure that the tw...
PUM
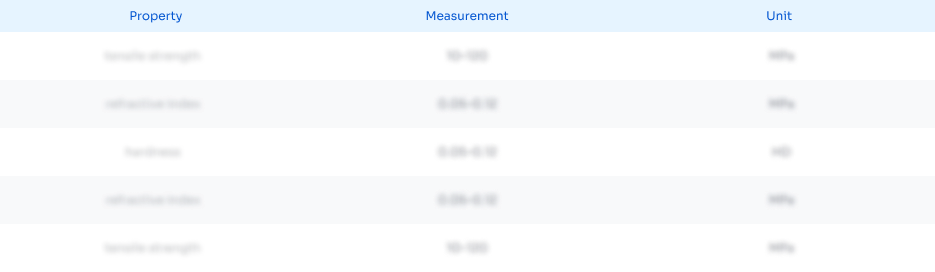
Abstract
Description
Claims
Application Information

- Generate Ideas
- Intellectual Property
- Life Sciences
- Materials
- Tech Scout
- Unparalleled Data Quality
- Higher Quality Content
- 60% Fewer Hallucinations
Browse by: Latest US Patents, China's latest patents, Technical Efficacy Thesaurus, Application Domain, Technology Topic, Popular Technical Reports.
© 2025 PatSnap. All rights reserved.Legal|Privacy policy|Modern Slavery Act Transparency Statement|Sitemap|About US| Contact US: help@patsnap.com