Method for electrolytically extracting rare earth through liquid cathode molten salt and preparing lead rare earth alloy
A molten salt electrolysis, liquid cathode technology, applied in the electrolysis process, electrolysis components, electrodes and other directions, can solve the problems of large energy consumption and burning loss, difficult separation of dysprosium in alloys, etc., and achieve the effect of improving the extraction rate of rare earth
- Summary
- Abstract
- Description
- Claims
- Application Information
AI Technical Summary
Problems solved by technology
Method used
Image
Examples
Embodiment 1
[0035] 38g lithium chloride, 45g potassium chloride, 1.8g dysprosium chloride (DyCl 3 ) and put into an alumina crucible. Put the crucible into an electrolytic cell filled with high-purity argon, and put a small crucible containing 20g of lead ingot into an alumina crucible, as shown in the diagram of the device figure 1 shown. Raise the temperature to 500°C and keep it warm for 2 hours to ensure that the molten salt and the lead ingot melt evenly. After the heat preservation is over, silver / silver chloride is used as a reference electrode, graphite rod is used as an auxiliary electrode, W and liquid lead are respectively used as working electrodes, and molten salt is inserted to connect to an electrochemical workstation for cyclic voltammetry, as shown in figure 2 shown. Depolarization values of about 0.66 V were obtained by measuring the redox peaks of Dy on W and liquid lead electrodes. Using liquid lead as the cathode, a tungsten wire covered with an alumina tube is...
Embodiment 2
[0039] 38g lithium chloride, 45g potassium chloride, 1.8g dysprosium chloride (DyCl 3 ) and put into an alumina crucible. Put the crucible into an electrolytic cell filled with high-purity argon, and put a small crucible containing 20g of lead ingot into an alumina crucible. Raise the temperature to 500°C and keep it warm for 2 hours to ensure that the molten salt and the lead ingot melt evenly. After the heat preservation, silver / silver chloride was used as reference electrode, graphite rod was used as auxiliary electrode, W and liquid lead were respectively used as working electrodes, and molten salt was inserted into the electrochemical workstation for cyclic voltammetry. Depolarization values were obtained by measuring the redox peaks of dysprosium on W and liquid lead electrodes. The liquid lead is used as the cathode, and a tungsten wire covered with an alumina tube is inserted into the liquid lead as a wire, and constant potential electrolysis is performed according...
Embodiment 3
[0043] 38g lithium chloride, 45g potassium chloride, 1.8g holmium chloride (HoCl 3 ) and put into an alumina crucible. Put the crucible into an electrolytic cell filled with high-purity argon, and put a small crucible containing 20g of lead ingot into an alumina crucible. Raise the temperature to 500°C and keep it warm for 2 hours to ensure that the molten salt and the lead ingot melt evenly. After the heat preservation is over, silver / silver chloride is used as a reference electrode, graphite rod is used as an auxiliary electrode, W and liquid lead are respectively used as working electrodes, and molten salt is inserted to connect to an electrochemical workstation for cyclic voltammetry, as shown in figure 2 shown. Depolarization values were obtained by measuring the redox peaks of Ho on W and liquid lead electrodes. The liquid lead is used as the cathode, and a tungsten wire covered with an alumina tube is inserted into the liquid lead as a wire, and constant potential...
PUM
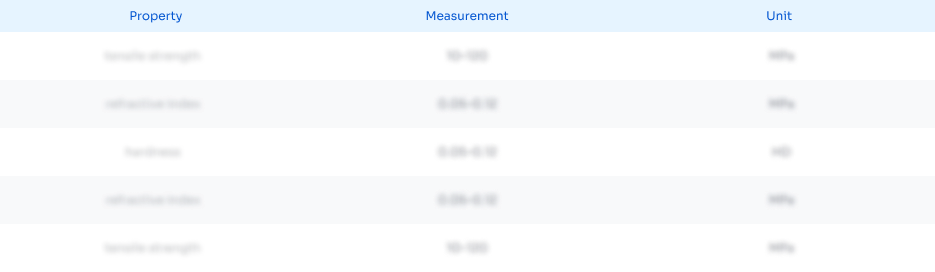
Abstract
Description
Claims
Application Information

- R&D Engineer
- R&D Manager
- IP Professional
- Industry Leading Data Capabilities
- Powerful AI technology
- Patent DNA Extraction
Browse by: Latest US Patents, China's latest patents, Technical Efficacy Thesaurus, Application Domain, Technology Topic, Popular Technical Reports.
© 2024 PatSnap. All rights reserved.Legal|Privacy policy|Modern Slavery Act Transparency Statement|Sitemap|About US| Contact US: help@patsnap.com