Flue gas desulfurizing and denitrifying technology in thermal power plant
A technology for desulfurization and denitrification and thermal power plants, which is applied in the field of flue gas desulfurization and denitrification process in thermal power plants. It can solve the problems that cannot meet the needs of the market, the flue gas desulfurization and denitrification process is complicated, and the desulfurization and denitrification efficiency are general. It achieves good chemical adsorption and powerful The effect of adsorption force and prolonging the active time
- Summary
- Abstract
- Description
- Claims
- Application Information
AI Technical Summary
Problems solved by technology
Method used
Image
Examples
Embodiment 1
[0022] A thermal power plant flue gas desulfurization and denitration process includes the following steps:
[0023] (1) Cool the original flue gas to 95.5°C, and then pass the cooled flue gas into activated carbon at room temperature for primary filtration treatment to obtain primary filtered flue gas;
[0024] (2) Continue to pass the first-stage filtered flue gas obtained above into the steel slag composite system to obtain the second-stage filtered flue gas; the temperature of the steel slag composite system is 30℃, the humidity is 25%, and the first-stage filtered flue gas inflow rate is 0.8 m³ / h;
[0025] In parts by weight, steel slag 42, vermiculite powder 10, montmorillonite 11, and illite powder 4 are uniformly mixed together, then ground, and passed through an 800-mesh sieve to obtain a mixed powder. The mixed powder is added to the ethanol solution. Add 2.5% melamine of its mass to the ethanol solution, heat to 55°C, stir at 250r / min for 45min, then prepare a sodium bica...
Embodiment 2
[0029] A thermal power plant flue gas desulfurization and denitration process includes the following steps:
[0030] (1) Cool the original flue gas to 97°C, and then pass the cooled flue gas into activated carbon at room temperature for primary filtration treatment to obtain primary filtered flue gas;
[0031] (2) Continue to pass the first-level filtered flue gas obtained above into the steel slag composite system to obtain the second-level filtered flue gas; the temperature of the steel slag composite system is 32℃, the humidity is 30%, and the first-level filtered flue gas flow rate is 0.8 m³ / h;
[0032] In parts by weight, steel slag 45, vermiculite powder 14, montmorillonite 15, and illite powder 6 are uniformly mixed together, then ground and passed through an 800-mesh sieve to obtain a mixed powder. The mixed powder is added to the ethanol solution. Add 3% melamine by mass to the ethanol solution, heat to 55°C, stir at 250r / min for 45min, then prepare a sodium bicarbonate sol...
Embodiment 3
[0037] A thermal power plant flue gas desulfurization and denitration process includes the following steps:
[0038] (1) Cool the original flue gas to 96°C, and then pass the cooled flue gas into activated carbon at room temperature for primary filtration treatment to obtain primary filtered flue gas;
[0039] (2) Continue to pass the first-stage filtered flue gas obtained above into the steel slag composite system to obtain the second-stage filtered flue gas; the temperature of the steel slag composite system is 31℃, the humidity is 28%, and the first-stage filtered flue gas flow rate is 0.8 m³ / h;
[0040] The steel slag 43, the vermiculite powder 12, the montmorillonite 13, and the illite powder 5 are uniformly mixed together in parts by weight, then ground, and passed through an 800-mesh sieve to obtain a mixed powder. The mixed powder is added to the ethanol solution. Add 2.8% melamine by mass to the ethanol solution, heat to 55°C, stir at 250r / min for 45min, then prepare a sodi...
PUM
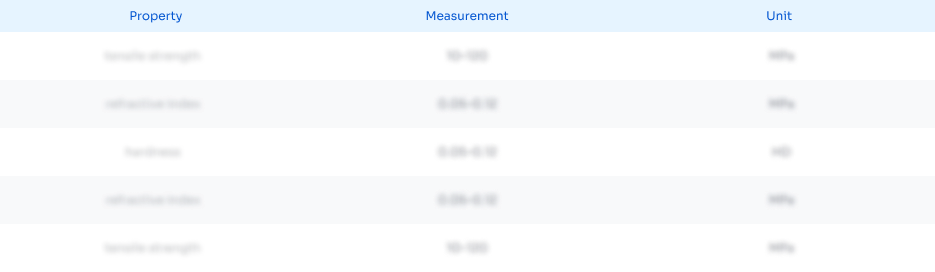
Abstract
Description
Claims
Application Information

- Generate Ideas
- Intellectual Property
- Life Sciences
- Materials
- Tech Scout
- Unparalleled Data Quality
- Higher Quality Content
- 60% Fewer Hallucinations
Browse by: Latest US Patents, China's latest patents, Technical Efficacy Thesaurus, Application Domain, Technology Topic, Popular Technical Reports.
© 2025 PatSnap. All rights reserved.Legal|Privacy policy|Modern Slavery Act Transparency Statement|Sitemap|About US| Contact US: help@patsnap.com