A method for improving intergranular corrosion performance of al-cu-mg aluminum alloys
An al-cu-mg, intergranular corrosion technology, which is applied in the field of improving the intergranular corrosion performance of Al-Cu-Mg aluminum alloys, can solve the complex soaking process, long time period, and lack of influence rules on the intergranular corrosion performance of alloys and other problems, to achieve the effects of reducing quenching sensitivity, good operability, saving heat treatment energy consumption and production cost
- Summary
- Abstract
- Description
- Claims
- Application Information
AI Technical Summary
Problems solved by technology
Method used
Image
Examples
Embodiment 1
[0033] The composition of aluminum alloy is calculated by mass percentage: Cu4.0wt.%, Mg1.4wt.%, Mn0.5wt.%, Ti<0.1wt.%, Fe≤0.2wt.%, Si≤0.1wt.%, the balance for Al. Semi-continuous casting into flat ingots with a thickness of 45mm.
[0034] The process for homogenizing the aluminum alloy includes: heating the aluminum alloy from room temperature to 465° C. at a heating rate of 50° C. / h for 6 hours, and then cooling in air. After the ingot is soaked, hot rolling, cold rolling, intermediate annealing, solid solution and natural aging treatment are carried out to prepare plates. Before ingot hot rolling, preheat at a heating rate of 460°C / 3h, roll a 6-7mm thick plate from 40mm thickness, pass reduction 2-5mm, and control the hot rolling exit temperature above 300°C. The hot-rolled sheet is sequentially subjected to recrystallization annealing at 410°C / 45min, cold-rolled and thinned to 2mm, and then stress-relief annealed at 280°C / 60min. After the plate is subjected to high-temp...
Embodiment 2
[0036] The composition of aluminum alloy is calculated by mass percentage: Cu4.0wt.%, Mg1.4wt.%, Mn0.5wt.%, Ti<0.1wt.%, Fe≤0.2wt.%, Si≤0.1wt.%, the balance for Al. Semi-continuous casting into flat ingots with a thickness of 45mm.
[0037] The alloy is homogenized by the low-temperature short-time homogenization heat treatment system of the method of the present invention, and after the ingot is soaked, it is subjected to hot rolling, cold rolling, intermediate annealing, solid solution and natural aging treatment to prepare plates. The specific process is as follows: from room temperature to 475°C at an average heating rate of 50°C / h for 6 hours, then air cooling. Before ingot hot rolling, preheat at 460°C / 3h, roll a 6-7mm thick plate from 40mm thickness, pass reduction 2-5mm, and control the hot rolling exit temperature above 300°C. The hot-rolled sheet was subjected to recrystallization annealing at 410°C / 45min. Afterwards, cold rolling is carried out to reduce the thick...
Embodiment 3
[0039] The composition of aluminum alloy is calculated by mass percentage: Cu4.0wt.%, Mg1.4wt.%, Mn0.5wt.%, Ti<0.1wt.%, Fe≤0.2wt.%, Si≤0.1wt.%, the balance for Al. Semi-continuous casting into flat ingots with a thickness of 45mm.
[0040]The alloy is homogenized by the low-temperature short-time homogenization heat treatment system of the method of the present invention, and after the ingot is soaked, it is subjected to hot rolling, cold rolling, intermediate annealing, solid solution and natural aging treatment to prepare plates. The specific process is as follows: from room temperature to 485°C at an average temperature increase rate of 50°C / h for 6 hours and then air cooling. Before ingot hot rolling, preheat at 460°C / 3h, roll a 6-7mm thick plate from 40mm thickness, pass reduction 2-5mm, and control the hot rolling exit temperature above 300°C. The hot-rolled sheet was subjected to recrystallization annealing at 410°C / 45min. Afterwards, cold rolling is carried out to r...
PUM
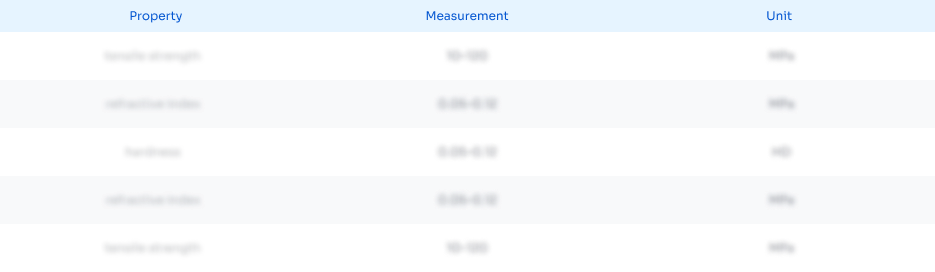
Abstract
Description
Claims
Application Information

- R&D Engineer
- R&D Manager
- IP Professional
- Industry Leading Data Capabilities
- Powerful AI technology
- Patent DNA Extraction
Browse by: Latest US Patents, China's latest patents, Technical Efficacy Thesaurus, Application Domain, Technology Topic, Popular Technical Reports.
© 2024 PatSnap. All rights reserved.Legal|Privacy policy|Modern Slavery Act Transparency Statement|Sitemap|About US| Contact US: help@patsnap.com