Method for recycling germanium from high-silicon-content optical fiber production waste
A technology for producing waste and optical fibers, applied in the direction of improving process efficiency, can solve the problems of inability to leaching, high silicon content in the leaching solution, and high production costs, and achieve the effects of avoiding hazards, high-efficiency recycling, and low-cost
- Summary
- Abstract
- Description
- Claims
- Application Information
AI Technical Summary
Problems solved by technology
Method used
Examples
Embodiment
[0017] Embodiment: A method for recovering germanium from waste material of high-silicon-containing optical fiber production, including the following steps:
[0018] Step 1. Grind the high-silicon fiber production waste (bottom slag and scum) to more than 100 meshes, destroying the crystalline silicon structure and the phenomenon of silicon-coated germanium;
[0019] Step 2. Add sodium sulfide or sulfur powder to the grinding material of step 1 according to S / Ge=1.2-1.3, mix evenly, and granulate into a diameter of 1-5mm;
[0020] Step 3. Add the granular raw material of step 2 to a microwave oven, a fuming furnace, a rotary kiln, and other sulfidation volatilization furnaces, and control the sulfidation volatilization temperature of 800-1000°C for germanium sulfidation volatilization;
[0021] Step 4. Perform oxidation roasting of the sulfide volatilized fume in step 3, and control the oxidation roasting temperature to be 300-500°C. In this step, care should be taken to prevent german...
example 1
[0024] Example 1. The furnace bottom slag produced by an enterprise producing optical fiber contains 96.5% silica and 2.78% germanium. It is ground to 120 mesh first, and then sodium sulfide is added according to S / Ge=1.2, mixed uniformly and granulated into diameter 2mm. Put it in a microwave oven for vulcanization and volatilization. The operating conditions of the microwave oven are microwave radiation frequency 2.4GHz, power 500W, furnace temperature 850℃, time 20 minutes, and vulcanized volatile fumes mainly contain 29.1% germanium, 18.3% sulfur, 9.2% silica, and volatile residue contains dioxide Silicon is 94.5%, germanium is 0.18%, and germanium volatilization rate is 92.3%.
example 2
[0025] Example 2. The bottom slag and scum mixture of an optical fiber production furnace contains 95.2% silicon dioxide and 3.1% germanium. After grinding to 250 mesh, add sulfur powder according to S / Ge=1.25, mix and granulate to a diameter of 3.5mm. The sulfide volatilization furnace in the laboratory uses electric heating to perform vulcanization and volatilization. The temperature in the furnace is controlled to 1000°C for 2 hours. The sulfurized dust contains 27.8% germanium, 16.5% sulfur, 15.8% silica, and 0.31 germanium in the slag. %. The germanium volatilization rate is 90%.
[0026] Example 3. Use the sulfurized volatile fumes of Example 1 to oxidize and roast in a microwave oven, add an oxidizer (hydrogen peroxide) to 110% of the oxygen required for the total sulfur content in the raw materials, mix uniformly, and place in a microwave oven to control the microwave power 300-500W, temperature 350℃± 10°C, time 10 minutes. The sulfur content in the roasted product is r...
PUM
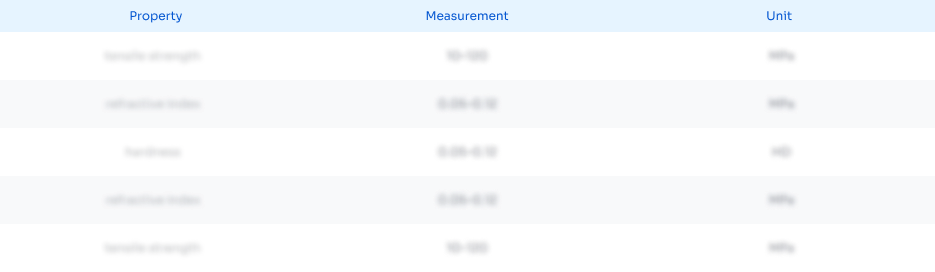
Abstract
Description
Claims
Application Information

- R&D
- Intellectual Property
- Life Sciences
- Materials
- Tech Scout
- Unparalleled Data Quality
- Higher Quality Content
- 60% Fewer Hallucinations
Browse by: Latest US Patents, China's latest patents, Technical Efficacy Thesaurus, Application Domain, Technology Topic, Popular Technical Reports.
© 2025 PatSnap. All rights reserved.Legal|Privacy policy|Modern Slavery Act Transparency Statement|Sitemap|About US| Contact US: help@patsnap.com