Hydrogenation method of C4 unsaturated hydrocarbon
A technology of unsaturated and hydrogenation catalysts, which is applied in the field of hydrogenation of C4 unsaturated hydrocarbons, can solve the problems of reduced utilization of catalyst active components, decreased catalyst activity, increased production costs, etc., to achieve long-term stable operation and reduce Production amount and the effect of improving hydrogenation activity
- Summary
- Abstract
- Description
- Claims
- Application Information
AI Technical Summary
Problems solved by technology
Method used
Image
Examples
Embodiment 1
[0026] (1) Preparation of silica-alumina composition 1
[0027] 1. Preparation of nickel-containing magnesium aluminate LaMgAl 11 o 19 The process is as follows:
[0028] Take 7.8 grams of basic magnesium carbonate, 25 grams of lanthanum carbonate and 70.5 grams of aluminum hydroxide, mix well, add deionized water to form a highly dispersed suspension, then add 8 grams of nickel nitrate, spray dry, and dry at 140 ° C for 5 hours. and placed in an air atmosphere at 1300° C. for 4 hours and then ball milled for 18 hours to obtain nickel-containing magnesium lanthanum aluminate powder. The nickel-containing magnesium-lanthanum aluminate powder is added with water, and the highly dispersed nickel-containing magnesium-lanthanum aluminate slurry is obtained after ultrasonic vibration.
[0029] 2. Preparation of silica-alumina composition
[0030] Take 140g of pseudo-boehmite and 22g of scallop powder, mix evenly, add dilute nitric acid, then add 20g of sodium polyacrylate nitric...
Embodiment 2
[0034] (1) Preparation of silica-alumina composition 2
[0035] The preparation of nickel-containing magnesium lanthanum aluminate is the same as in Example 1, the preparation of the silica-alumina composition is the same as in Example 1, and 70% of pseudo-boehmite is mixed evenly with celadon powder, and the pore-enlarging agent 1 is polyvinyl alcohol. The added amount accounts for 22% of the mass of the added alumina, and the added amount of the pore expander 2 chitosan accounts for 5% of the added mass of the alumina and silicon oxide. The silica-alumina composition contains 4.9wt% silica and 6.5wt% nickel-containing magnesium lanthanum aluminate.
[0036] (2) Preparation of catalyst
[0037] The preparation method of the catalyst was the same as that in Example 1. The polyacrylic acid and the silica-alumina composition powder were mixed uniformly in a ratio of 1.8:1 by volume. The composition of the catalyst was shown in Table 1.
Embodiment 3
[0039] (1) Preparation of silica-alumina composition 3
[0040] The preparation of nickel-containing magnesium lanthanum aluminate is the same as in Example 1, the preparation of the silica-alumina composition is the same as in Example 1, and 65% of pseudo-boehmite is mixed evenly with squat powder, and the pore-enlarging agent 1 is polyacrylate The added amount accounts for 17% of the mass of the added alumina, and the added amount of the pore-enlarging agent 2 methylcellulose accounts for 3.7% of the added mass of the alumina and silicon oxide. The silica-alumina composition contained 6.2 wt% of silica and 7.8 wt% of nickel-containing magnesium lanthanum aluminate.
[0041] (2) Preparation of catalyst
[0042] The preparation method of catalyst 3 was the same as that in Example 1. Sodium polyacrylate was added to dilute nitric acid and mixed evenly with the silica-alumina composition powder at a volume ratio of 1.5:1. The composition of the catalyst was shown in Table 1.
PUM
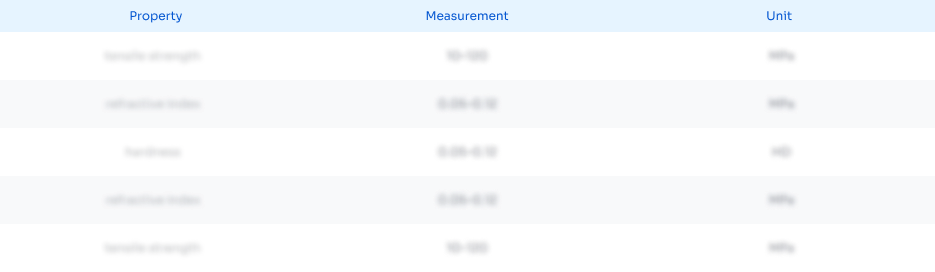
Abstract
Description
Claims
Application Information

- R&D Engineer
- R&D Manager
- IP Professional
- Industry Leading Data Capabilities
- Powerful AI technology
- Patent DNA Extraction
Browse by: Latest US Patents, China's latest patents, Technical Efficacy Thesaurus, Application Domain, Technology Topic, Popular Technical Reports.
© 2024 PatSnap. All rights reserved.Legal|Privacy policy|Modern Slavery Act Transparency Statement|Sitemap|About US| Contact US: help@patsnap.com