A method for harmless treatment of dioxin in waste incineration fly ash
A technology for waste incineration fly ash and harmless treatment, which is applied in the field of comprehensive utilization of solid waste resources, can solve the problems of low efficiency, secondary environmental pollution, and high cost, and achieves the effect of reducing costs and avoiding re-synthesis.
- Summary
- Abstract
- Description
- Claims
- Application Information
AI Technical Summary
Problems solved by technology
Method used
Image
Examples
Embodiment 1
[0028] 30wt% of waste incineration fly ash, 40wt% of waste glass powder, 15wt% of pickling sludge and 15wt% of dolomite powder are uniformly mixed to obtain a mixture, and pressed at 10MPa to obtain a compact. The compact is heated at 1000°C for 60 minutes, the dolomite is decomposed and the glass melt is foamed, and then the temperature is lowered to 500°C and annealed for 60 minutes to obtain foam glass. Then raise the temperature to 800° C. for nucleation and crystallization heat treatment for 30 minutes, then cool down to room temperature with the furnace to obtain a foamed glass-ceramic product. In the process of melting and foaming, chlorine atoms react with calcium oxide and magnesium oxide and solidify in the glass melt, and then solidify in the foamed glass-ceramic after subsequent annealing, nucleation and crystallization, which reduces the dioxin synthesis in the flue gas. chlorine content. The flue gas is subjected to rapid cooling treatment, and the flue gas is c...
Embodiment 2
[0030] 33wt% of waste incineration fly ash, 42wt% of waste glass powder, 12wt% of pickling sludge and 13wt% of dolomite powder are uniformly mixed to obtain a mixture, which is pressed at 15MPa to obtain a compact. The compact was heated at 1010°C for 58 minutes, the dolomite was decomposed and the glass melt was foamed, and then the temperature was lowered to 510°C and annealed for 57 minutes to obtain foam glass. Then raise the temperature to 795° C. for nucleation and crystallization heat treatment for 32 minutes, and then cool to room temperature with the furnace to obtain a foamed glass-ceramic product. During the melting and foaming process, chlorine atoms react with calcium oxide and magnesium oxide and solidify in the glass melt, and then solidify in the foamed glass-ceramics through subsequent annealing, nucleation and crystallization, which reduces the dioxin synthesis in the flue gas. chlorine content. The flue gas is subjected to quenching treatment, and the flue ...
Embodiment 3
[0032] 36wt% of waste incineration fly ash, 44wt% of waste glass powder, 9wt% of pickling sludge and 11wt% of dolomite powder are uniformly mixed to obtain a mixture, which is pressed at 20MPa to obtain a compact. The compact was heated at 1020°C for 56 minutes, the dolomite was decomposed and the glass melt was foamed, and then the temperature was lowered to 520°C and annealed for 54 minutes to obtain foam glass. Then raise the temperature to 790° C. for nucleation and crystallization heat treatment for 34 minutes, and then cool down to room temperature with the furnace to obtain a foamed glass-ceramic product. During the melting and foaming process, chlorine atoms react with calcium oxide and magnesium oxide and solidify in the glass melt, and then solidify in the foamed glass-ceramics through subsequent annealing, nucleation and crystallization, which reduces the dioxin synthesis in the flue gas. chlorine content. The flue gas is subjected to rapid cooling treatment, and t...
PUM
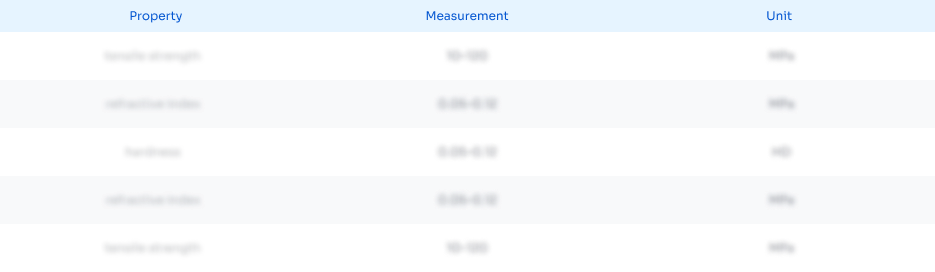
Abstract
Description
Claims
Application Information

- R&D
- Intellectual Property
- Life Sciences
- Materials
- Tech Scout
- Unparalleled Data Quality
- Higher Quality Content
- 60% Fewer Hallucinations
Browse by: Latest US Patents, China's latest patents, Technical Efficacy Thesaurus, Application Domain, Technology Topic, Popular Technical Reports.
© 2025 PatSnap. All rights reserved.Legal|Privacy policy|Modern Slavery Act Transparency Statement|Sitemap|About US| Contact US: help@patsnap.com