Large 3D printing support material and preparation method thereof
A supporting material and 3D printing technology, applied in the field of 3D printing materials, can solve the problems of unfavorable economic and environmental protection for the promotion and use of large-scale 3D printing parts, unfavorable mass use, and increased printing costs, so as to achieve low strength and toughness and increase adhesion performance, the effect of reducing the use of materials
- Summary
- Abstract
- Description
- Claims
- Application Information
AI Technical Summary
Problems solved by technology
Method used
Image
Examples
specific Embodiment
[0024] A large-scale 3D printing support material provided by the present invention includes the following components in mass percentage:
[0025]
[0026]
[0027] The sum of the mass percentages of each component in the calcium carbonate filler masterbatch and the polyolefin or olefin elastomer material is 100%.
[0028] In some limited embodiments, one or any combination of the following options may be selected:
[0029] The calcium carbonate filling masterbatch is processed by mixing 1500-mesh calcium carbonate powder and PP carrier, and 2000-mesh calcium carbonate powder and LDPE carrier.
[0030] The thermoplastic elastomer is selected from one or more of TPV, TPE, and TPO, and its proportion is 10-30%.
[0031] The foaming agent is azodicarbonamide AC, one or more selected from AC-1600, AC-1601, AC-1500W, and AC-1900; its proportion is 0.1-5%.
[0032] The surface modifying agent is selected from one of maleic anhydride grafted ethylene-octene copolymer and rosi...
Embodiment 1
[0043] Supporting material, including the following components in mass percentage: 1500 mesh calcium carbonate powder plus PE carrier 78% filler masterbatch, 20% TPV, 1% AC-1900 foaming agent, 0.5% DOP , 0.5% antioxidant, the preparation method of this support material is as follows:
[0044]Put the 1500-mesh calcium carbonate powder and the filled masterbatch of PE carrier in a constant temperature drying oven at 80°C for 2 hours. Weigh 39.5KG of filler masterbatch, TPV10KG, 0.5KG of AC-1900 foaming agent, 0.25KG of PE wax, and 0.25KG of antioxidant; then mix in a high-speed mixer for 10 minutes. The uniformly mixed material is added to the hopper of the twin-screw extruder, and the temperature of each section is controlled at: Zone 1: 130°C; Zone 2: 150°C; Zone 3: 160°C; Zone 4: 170°C; Zone 5: 180°C ; Zone 6: 190°C; Zone 7: 200°C; Zone 8: 200°C; Head temperature: 190°C, screw speed 250r / min, the support material was obtained by melt blending extrusion, cooling, water coolin...
Embodiment 2
[0046] Supporting material, including the following components in mass percentage: 2000 mesh calcium carbonate powder plus 78% filler masterbatch of PP carrier, 20% TPO, 1% AC-1900 foaming agent, 0.5% DOP , 0.5% antioxidant. The preparation method of this supporting material is as follows:
[0047] Put the 2000-mesh calcium carbonate powder plus the PP carrier filling masterbatch in a constant temperature drying oven at 80°C for 2h. Weigh 39.5KG of filler masterbatch, 10KG of PE, 0.5KG of AC-1600 foaming agent, 0.25KG of PE wax, and 0.25KG of antioxidant; then mix in a high-speed mixer for 10 minutes. The mixed military printed material is added to the hopper of the twin-screw extruder, and the temperature of each section is controlled at: Zone 1: 130 °C; Zone 2: 150 °C; Zone 3: 160 °C; Zone 4: 170 °C; Zone 5: 180 °C; Zone: 190°C; Zone 7: 200°C; Zone 8: 200°C; Head temperature: 190°C, screw speed 250r / min, the support material was obtained by melt blending extrusion, cooling...
PUM
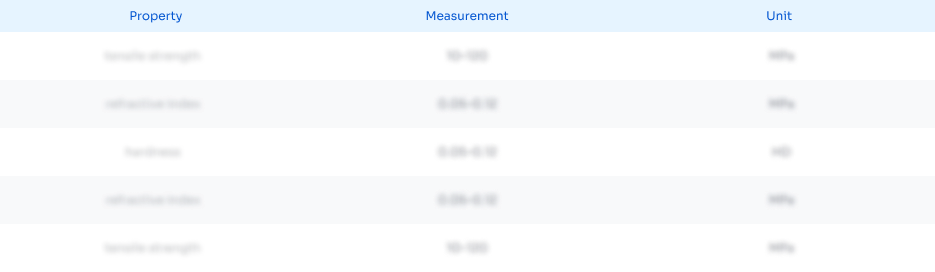
Abstract
Description
Claims
Application Information

- R&D
- Intellectual Property
- Life Sciences
- Materials
- Tech Scout
- Unparalleled Data Quality
- Higher Quality Content
- 60% Fewer Hallucinations
Browse by: Latest US Patents, China's latest patents, Technical Efficacy Thesaurus, Application Domain, Technology Topic, Popular Technical Reports.
© 2025 PatSnap. All rights reserved.Legal|Privacy policy|Modern Slavery Act Transparency Statement|Sitemap|About US| Contact US: help@patsnap.com