Ultrahigh-pressure high-temperature synthesizing method of second-phase particle simulation material in aluminium alloy
A technology for simulating materials and synthesis methods, which is applied in the field of intermetallic compound preparation, can solve the problems of low measurement accuracy of micro-area electrochemical testing technology, difficult preparation of nano-probes, and large environmental interference, so as to avoid significant changes in chemical composition and atomic The effect of fast diffusion and rapid grain growth
- Summary
- Abstract
- Description
- Claims
- Application Information
AI Technical Summary
Problems solved by technology
Method used
Image
Examples
Embodiment approach
[0018] In the present invention, the most typical precipitated phase MgZn in the 7000 series aluminum alloy widely used in industry is 2 phase (according to the Mg-Zn binary phase diagram, MgZn 2 The melting point of normal pressure is about 600 ℃) as an example, and the ultra-high pressure and high temperature synthesis method is further described in detail. The compaction mold used in the following examples and comparative examples is based on the graphite cover on the artificial diamond six-sided top press in advance. The lumen of the tube is dimensioned and larger than that required for conventional electrochemical test samples.
[0019] testing method:
[0020] Composition analysis was carried out by JSM-6010LA scanning electron microscope (SEM) with energy spectrometer;
[0021] The phase analysis was carried out by Bruker D8 X-ray diffractometer (XRD).
Embodiment 1
[0023] by MgZn 2 The chemical composition of the phase is measured by weighing an appropriate amount of industrially pure Zn powder and pure Mg powder, mixing them evenly, pouring them into the compacting mold, and pressing the powder green body with a size of φ30mm×30mm on a hydraulic press; then, the pressed The blank is pressed into a graphite sleeve with an inner cavity size of φ30mm×40mm, and the two ends are sealed with φ30mm×5mm graphite sheets and assembled into a composite block, which is then assembled in the working chamber of a synthetic diamond six-sided top press. After applying a pressure of 5GPa , heated to about 800°C by turning on the power and kept the temperature for 10 minutes, then kept the pressure, turned off the power and cooled to room temperature, then released the pressure and took out the sample.
[0024] figure 1 For the XRD spectrum of the synthetic sample in Example 1, it can be seen that only MgZn is contained in the sample 2 phase diffractio...
Embodiment 2
[0026] by MgZn 2 The chemical composition of the phase is measured by weighing an appropriate amount of industrially pure Zn powder and pure Mg powder, mixing them evenly, pouring them into the compacting mold, and pressing the powder green body with a size of φ30mm×50mm on a hydraulic press; then, the pressed The biscuit is pressed into the inner cavity of the graphite sleeve and assembled into a synthetic block, which is then assembled in the working chamber of the artificial diamond six-sided top press. After applying a pressure of 1GPa, it is heated to about 650°C, kept for 60 minutes, and then the pressure is maintained. After the power was turned off and cooled to room temperature, the pressure was released and the sample was taken out.
[0027] image 3 The energy spectrum analysis results of the samples synthesized in Example 2, it can be seen that the (Mg+Al+Si) / Zn atomic ratio in the sample is close to 1:2, indicating that the sample only contains MgZn 2 A type of ...
PUM
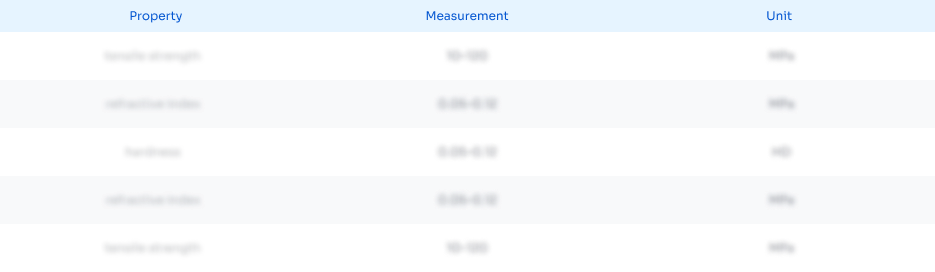
Abstract
Description
Claims
Application Information

- R&D Engineer
- R&D Manager
- IP Professional
- Industry Leading Data Capabilities
- Powerful AI technology
- Patent DNA Extraction
Browse by: Latest US Patents, China's latest patents, Technical Efficacy Thesaurus, Application Domain, Technology Topic, Popular Technical Reports.
© 2024 PatSnap. All rights reserved.Legal|Privacy policy|Modern Slavery Act Transparency Statement|Sitemap|About US| Contact US: help@patsnap.com