Environment-friendly solvent-free polyurethane synthetic leather and manufacturing method thereof
A solvent-free polyurethane and synthetic leather technology, applied in textiles and papermaking, can solve problems such as low peel strength, poor adhesion, and easy separation
- Summary
- Abstract
- Description
- Claims
- Application Information
AI Technical Summary
Problems solved by technology
Method used
Image
Examples
Embodiment 1
[0026] Embodiment 1 environment-friendly solvent-free polyurethane synthetic leather and preparation method thereof
[0027] Environmentally friendly solvent-free polyurethane synthetic leather, including base fabric, water-based surface layer, water-based adhesive layer and solvent-free AB material foaming layer: The water-based adhesive layer is mainly composed of the following components by weight. Water-based polyurethane adhesive layer slurry mixing Prepared: 1000 parts of water-based polyurethane emulsion, 100 parts of water-based polyurethane crosslinking agent and 60 parts of water-based color paste; the solvent-free AB material foaming layer is mainly composed of the following parts by weight AB material foaming layer slurry is prepared by mixing Preparation: 800 parts of mixed polyol, 30 parts of organic metal catalyst, 90 parts of organic amine catalyst, 2000 parts of filler and 1500 parts of isocyanate.
[0028] When preparing the water-based surface layer, it is p...
Embodiment 2
[0036] Embodiment 2 environment-friendly solvent-free polyurethane synthetic leather and preparation method thereof
[0037]Environmentally friendly solvent-free polyurethane synthetic leather, including base fabric, water-based surface layer, water-based adhesive layer and solvent-free AB material foaming layer: The water-based adhesive layer is mainly composed of the following components by weight. Water-based polyurethane adhesive layer slurry mixing Prepared: 800 parts of water-based polyurethane emulsion, 80 parts of water-based polyurethane crosslinking agent and 50 parts of water-based color paste; the solvent-free AB material foam layer is mainly prepared by mixing the AB material foam layer slurry composed of the following parts by weight Preparation: 800 parts of mixed polyol, 30 parts of organic metal catalyst, 90 parts of organic amine catalyst, 2000 parts of filler and 1500 parts of isocyanate.
[0038] When preparing the water-based surface layer, it is preferred...
Embodiment 3
[0046] Embodiment 3 environment-friendly solvent-free polyurethane synthetic leather and preparation method thereof
[0047] Environmentally friendly solvent-free polyurethane synthetic leather, including base fabric, water-based surface layer, water-based adhesive layer and solvent-free AB material foaming layer: The water-based adhesive layer is mainly composed of the following components by weight. Water-based polyurethane adhesive layer slurry mixing Prepared: 800 parts of water-based polyurethane emulsion, 80 parts of water-based polyurethane crosslinking agent and 50 parts of water-based color paste; the solvent-free AB material foam layer is mainly prepared by mixing the AB material foam layer slurry composed of the following parts by weight Preparation: 800 parts of mixed polyol, 30 parts of organic metal catalyst, 90 parts of organic amine catalyst, 2000 parts of filler and 1500 parts of isocyanate.
[0048] When preparing the water-based surface layer, it is preferre...
PUM
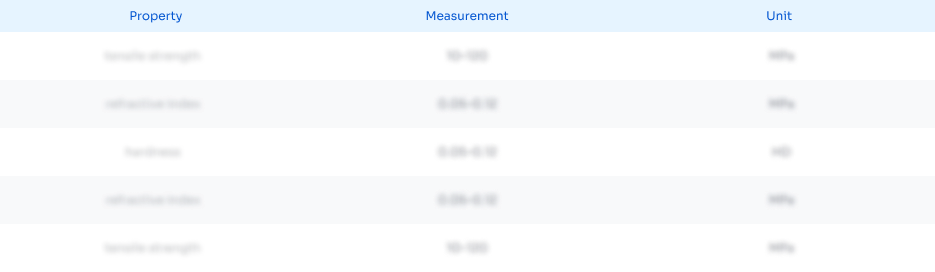
Abstract
Description
Claims
Application Information

- R&D Engineer
- R&D Manager
- IP Professional
- Industry Leading Data Capabilities
- Powerful AI technology
- Patent DNA Extraction
Browse by: Latest US Patents, China's latest patents, Technical Efficacy Thesaurus, Application Domain, Technology Topic, Popular Technical Reports.
© 2024 PatSnap. All rights reserved.Legal|Privacy policy|Modern Slavery Act Transparency Statement|Sitemap|About US| Contact US: help@patsnap.com