Recycling method of valuable metal from copper-cobalt white alloy
A technology of valuable metals and recycling methods, applied in the direction of improving process efficiency, etc., can solve the problems of high melting point of cobalt white alloy, high requirements for refractory materials, high smelting operation temperature, etc., to achieve lower smelting temperature, small amount of slagging agent, The effect of improving the economic efficiency of the process
- Summary
- Abstract
- Description
- Claims
- Application Information
AI Technical Summary
Problems solved by technology
Method used
Examples
Embodiment 1
[0035] A method for recovering valuable metals in copper-cobalt white alloys, comprising the steps of:
[0036] (1) 500kg matte and 500kg copper-cobalt white alloy (the mass content of the main components are respectively Co 38.87%, Fe32.45%, Cu 13.45%, Si 10.15%) are added in the converter;
[0037] (2) Control the smelting temperature in the converter to 1350°C, blow oxygen-enriched air (oxygen concentration 60%) into the converter, so that the materials in the converter react in an oxidative atmosphere, and produce blister copper, cobalt-containing slag and smoke gas;
[0038](3) Separation of blister copper and cobalt-containing slag, the main composition of cobalt-containing slag is: Fe 39.34%, Co 2.83%, SiO 2 25.68%, the recovery rate of cobalt in the cobalt slag is 98.65%, and the cobalt is recovered by acid leaching. When the cobalt slag is acid leached, the acid dosage is 1.1 times of the theoretical amount, the leaching temperature is 70°C, the leaching time is 5h, ...
Embodiment 2
[0041] A method for recovering valuable metals in copper-cobalt white alloys, comprising the steps of:
[0042] (1) Add 400kg matte, 100kg copper-nickel matte, 100kg scrap copper and 400kg copper-cobalt white alloy (mass content of main components are respectively Co 25.87%, Fe 40.05%, Cu 15.45%, Si 15.16%) into the converter;
[0043] (2) Control the smelting temperature in the converter to be 1310°C, blow a mixed gas of oxygen, air and carbon dioxide into the converter, and add slagging agent (limestone) at the same time, the mass ratio of limestone to cobalt white alloy is 0.25, so that the The materials are reacted in an oxidative atmosphere to produce blister copper, cobalt-containing slag and flue gas;
[0044] (3) Separation of blister copper and cobalt-containing slag, the main composition of cobalt-containing slag is: Fe 33.34%, Co 5.83%, SiO 2 22.68%, CaO 10.23%, the recovery rate of cobalt in cobalt slag is 95.65%, the cobalt is recovered by acid leaching method, ...
Embodiment 3
[0047] A method for recovering valuable metals in copper-cobalt white alloys, comprising the steps of:
[0048] (1) Add 600kg of copper-nickel matte, 200kg of scrap copper and 200kg of copper-cobalt white alloy (mass content of main components are respectively Co 33.83%, Fe 37.10%, Cu 16.88%, Si 5%) into the converter;
[0049] (2) Control the smelting temperature in the converter to 1240°C, blow a mixed gas of oxygen and air into the converter, and add a slagging agent (mass ratio of limestone to dolomite 1:1), and the mass of the slagging agent and copper-cobalt white alloy The ratio is 0.15. Make the materials in the converter react in an oxidizing atmosphere to produce blister copper, cobalt-containing slag and flue gas;
[0050] (3) Separation of blister copper and cobalt-containing slag, the main composition of cobalt-containing slag is: Fe 23.18%, Co 12.75%, SiO 2 14.68%, CaO 15.36%, the recovery rate of cobalt in cobalt slag is 90.23%, and the cobalt recovery rate is...
PUM
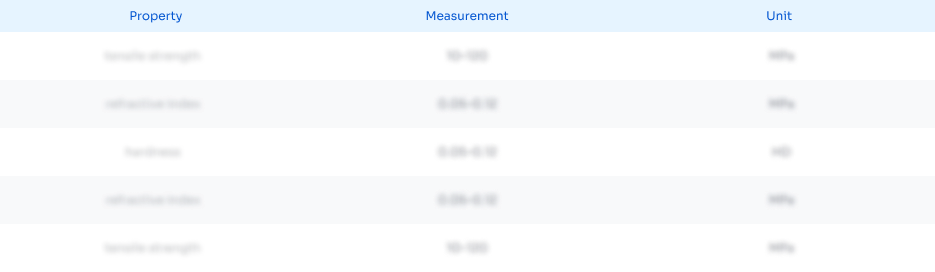
Abstract
Description
Claims
Application Information

- R&D
- Intellectual Property
- Life Sciences
- Materials
- Tech Scout
- Unparalleled Data Quality
- Higher Quality Content
- 60% Fewer Hallucinations
Browse by: Latest US Patents, China's latest patents, Technical Efficacy Thesaurus, Application Domain, Technology Topic, Popular Technical Reports.
© 2025 PatSnap. All rights reserved.Legal|Privacy policy|Modern Slavery Act Transparency Statement|Sitemap|About US| Contact US: help@patsnap.com