A method for recovering valuable metals from an alloy containing iron, cobalt and copper
A valuable metal and alloy technology, applied in the direction of improving process efficiency, can solve the problems of high requirements for refractory materials, high smelting operating temperature, and large output of smelting slag, so as to reduce smelting temperature, improve process economic benefits and economic benefits. outstanding effect
- Summary
- Abstract
- Description
- Claims
- Application Information
AI Technical Summary
Problems solved by technology
Method used
Examples
Embodiment 1
[0036] A method for recovering valuable metals from an alloy containing iron, cobalt and copper, comprising the steps of:
[0037] (1) 500kg matte and 500kg iron-cobalt-copper-containing alloy (copper-cobalt white alloy, the mass content of main components are respectively Co 38.87%, Fe 32.45%, Cu 13.45%, Si 10.15%) are added in the converter;
[0038] (2) Control the smelting temperature in the converter to 1300°C, and blow oxygen-enriched air (oxygen concentration 60%) into the converter to make the materials in the converter react in an oxidizing atmosphere to produce blister copper, cobalt-containing slag and smoke gas;
[0039] (3) Separation of blister copper and cobalt-containing slag, the main composition of cobalt-containing slag is: Fe 39.34%, Co 2.83%, SiO 2 25.68%, the recovery rate of cobalt in the cobalt slag is 98.65%, and the cobalt is recovered by acid leaching. When the cobalt slag is acid leached, the acid dosage is 1.1 times of the theoretical amount, the ...
Embodiment 2
[0042] A method for recovering valuable metals from an alloy containing iron, cobalt and copper, comprising the steps of:
[0043] (1) 400kg matte, 100kg copper-nickel matte, 100kg scrap copper and 400kg iron-cobalt-copper alloy (composed of copper-cobalt white alloy and waste lithium-ion battery reduction smelting alloy, the mass ratio of the two is 1:1 , mixed alloy components Co 15.87%, Fe20.05%, Cu 15.45%, Si 15.16%, Mn 15.78%) were added to the converter;
[0044] (2) Control the smelting temperature in the converter to 1300°C, blow a mixed gas of oxygen, air and carbon dioxide into the converter, so that the materials in the converter react in an oxidative atmosphere, and produce blister copper, cobalt-containing slag and flue gas ;
[0045] (3) Separation of blister copper and cobalt-containing slag, the main composition of cobalt-containing slag is: Fe 28.34%, Co 8.83%, Mn12.00%, SiO 2 22.68%, the recovery rate of cobalt in cobalt slag is 95.65%, and the cobalt is re...
Embodiment 3
[0048] A method for recovering valuable metals from an alloy containing iron, cobalt and copper, comprising the steps of:
[0049] (1) 400kg matte, 100kg copper-nickel matte, 100kg scrap copper and 400kg iron-cobalt-copper alloy (composed of copper-cobalt white alloy and waste lithium-ion battery reduction smelting alloy, the mass ratio of the two is 1:1 , mixed alloy components Co 15.87%, Fe20.05%, Cu 15.45%, Si 15.16%, Mn 15.78%) were added to the converter;
[0050] (2) Control the smelting temperature in the converter to be 1200°C, blow a mixed gas of oxygen, air and carbon dioxide into the converter, and add limestone at the same time, the mass ratio of limestone to the alloy containing iron, cobalt and copper is 0.15, so that the materials in the converter React in an oxidative atmosphere to produce blister copper, cobalt-containing slag and flue gas;
[0051] (3) Separation of blister copper and cobalt-containing slag, the main composition of cobalt-containing slag is:...
PUM
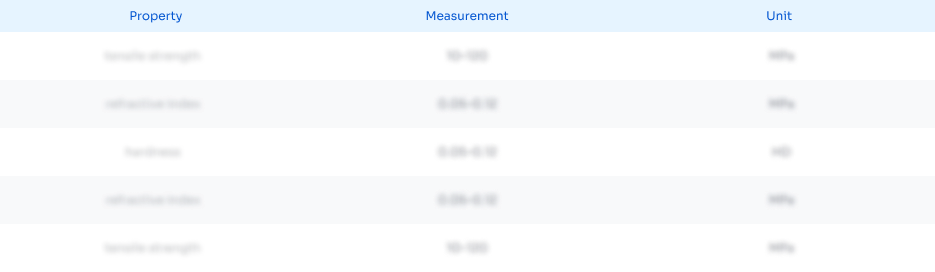
Abstract
Description
Claims
Application Information

- R&D
- Intellectual Property
- Life Sciences
- Materials
- Tech Scout
- Unparalleled Data Quality
- Higher Quality Content
- 60% Fewer Hallucinations
Browse by: Latest US Patents, China's latest patents, Technical Efficacy Thesaurus, Application Domain, Technology Topic, Popular Technical Reports.
© 2025 PatSnap. All rights reserved.Legal|Privacy policy|Modern Slavery Act Transparency Statement|Sitemap|About US| Contact US: help@patsnap.com