Method for preparing waterproof emulsion of thermosetting composite polystyrene foam insulation board
A technology of polystyrene foam and waterproof emulsion, applied in the direction of adhesive types, adhesive additives, ester copolymer adhesives, etc., can solve the problems of poor thermal insulation and sound absorption effects, and the inability to improve the thermal insulation effect of board gaps, etc., to achieve The effect of improving the thermal insulation effect
- Summary
- Abstract
- Description
- Claims
- Application Information
AI Technical Summary
Problems solved by technology
Method used
Image
Examples
Embodiment 1
[0021] A method for preparing a thermosetting composite polystyrene foam insulation board waterproof emulsion, said preparation method comprising the steps of:
[0022] (1) Weighing of raw materials, weighing of raw materials according to weight ratio, the weight ratio of each raw material when weighing is 35-37 parts of acrylic emulsion, 26 parts of polyvinyl alcohol, 25 parts of resin coating glue PBA, ethyl acetate 10-12 parts of grease, 13-16 parts of ethylene-vinyl acetate copolymer, 6-8 parts of light calcium powder, 5-8 parts of expanded perlite, 4-5 parts of calcium silicate;
[0023] (2) Mix some raw materials, put the acrylic emulsion, polyvinyl alcohol, resin coating glue PBA, ethyl acetate, ethylene-vinyl acetate copolymer and light calcium powder weighed in step (1) into the reaction kettle, The reaction kettle heats the input raw materials to keep the internal temperature of the reaction kettle at 60-75°C, then the reaction kettle mixes the raw materials, after s...
Embodiment 2
[0035] A method for preparing a thermosetting composite polystyrene foam insulation board waterproof emulsion, said preparation method comprising the steps of:
[0036] (1) Weighing of raw materials, weighing of raw materials according to weight ratio, the weight ratio of each raw material when weighing is 35-37 parts of acrylic emulsion, 20-26 parts of polyvinyl alcohol, 18-25 parts of resin coating glue PBA 10-12 parts of ethyl acetate, 16 parts of ethylene-vinyl acetate copolymer, 6-8 parts of light calcium powder, 5-8 parts of expanded perlite, 4-5 parts of calcium silicate;
[0037] (2) Mix some raw materials, put the acrylic emulsion, polyvinyl alcohol, resin coating glue PBA, ethyl acetate, ethylene-vinyl acetate copolymer and light calcium powder weighed in step (1) into the reaction kettle, The reaction kettle heats the input raw materials to keep the internal temperature of the reaction kettle at 60-75°C, then the reaction kettle mixes the raw materials, after stirri...
PUM
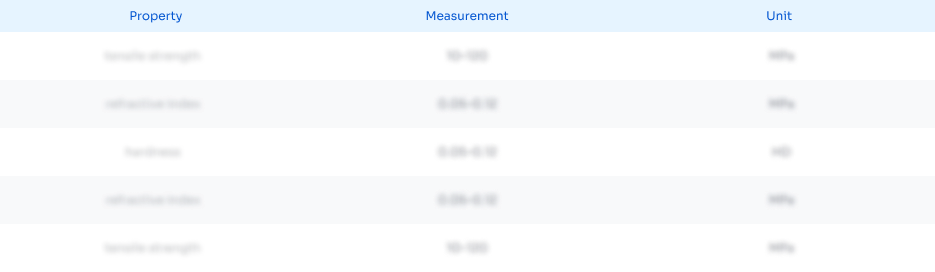
Abstract
Description
Claims
Application Information

- R&D Engineer
- R&D Manager
- IP Professional
- Industry Leading Data Capabilities
- Powerful AI technology
- Patent DNA Extraction
Browse by: Latest US Patents, China's latest patents, Technical Efficacy Thesaurus, Application Domain, Technology Topic, Popular Technical Reports.
© 2024 PatSnap. All rights reserved.Legal|Privacy policy|Modern Slavery Act Transparency Statement|Sitemap|About US| Contact US: help@patsnap.com