Preparation method and product of abs/pvdf alloy by self-assembly in situ
A self-assembly and alloying technology, applied in the field of polymer alloys, can solve problems such as ineffective effects, and achieve the effects of convenient and simple implementation, reduced interfacial tension, and excellent solvent resistance
- Summary
- Abstract
- Description
- Claims
- Application Information
AI Technical Summary
Problems solved by technology
Method used
Image
Examples
Embodiment 1
[0024] After drying polyvinylidene fluoride, styrene-acrylonitrile-butadiene terpolymer, and styrene-acrylonitrile-glycidyl methacrylate terpolymer in a vacuum oven at 80 °C for 24 hours, according to benzene The mass ratio of ethylene-acrylonitrile-butadiene terpolymer, polyvinylidene fluoride, styrene-acrylonitrile-glycidyl methacrylate terpolymer, and polymethyl methacrylate oligomer is 80: The ratio of 20:6:0.6 is mixed at room temperature and then added to the internal mixer. The temperature of the internal mixer is 210°C, the set speed is 50rpm, and the mixing time is 10min.
[0025] The above mixed samples were injected into a micro-injection molding machine (injection cylinder temperature 230°C, mold temperature 80°C) to obtain dumbbell-shaped splines and impact splines, and the impact splines were made into notches. The experimental results are shown in Table 1.
Embodiment 2
[0027] Its operation is the same as above-mentioned embodiment 1, difference is, wherein styrene-acrylonitrile-butadiene terpolymer, polyvinylidene fluoride, styrene-acrylonitrile-glycidyl methacrylate terpolymer, The mass ratio of polymethyl methacrylate oligomers was 80:20:6:1.8, and the mixed samples were prepared according to the same operation method as in Example 1. The test results are shown in Table 1.
Embodiment 3
[0029] After drying polyvinylidene fluoride, styrene-acrylonitrile-butadiene terpolymer, and styrene-acrylonitrile-glycidyl methacrylate terpolymer in a vacuum oven at 80 °C for 24 hours, according to benzene The mass ratio of ethylene-acrylonitrile-butadiene terpolymer, polyvinylidene fluoride, styrene-acrylonitrile-glycidyl methacrylate terpolymer, and polymethyl methacrylate oligomer is 90: The ratio of 5:3:2 is mixed at room temperature and then added to the internal mixer. The temperature of the internal mixer is 200°C, the set speed is 100rpm, and the mixing time is 10min.
[0030] The above mixed samples were injected into a micro-injection molding machine (injection cylinder temperature 230°C, mold temperature 80°C) to obtain dumbbell-shaped splines and impact splines, and the impact splines were made into notches.
PUM
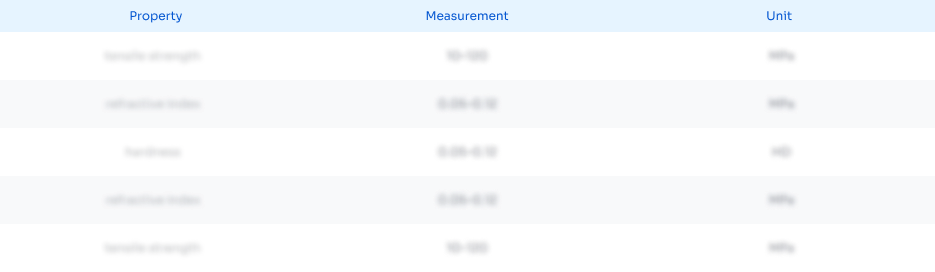
Abstract
Description
Claims
Application Information

- R&D
- Intellectual Property
- Life Sciences
- Materials
- Tech Scout
- Unparalleled Data Quality
- Higher Quality Content
- 60% Fewer Hallucinations
Browse by: Latest US Patents, China's latest patents, Technical Efficacy Thesaurus, Application Domain, Technology Topic, Popular Technical Reports.
© 2025 PatSnap. All rights reserved.Legal|Privacy policy|Modern Slavery Act Transparency Statement|Sitemap|About US| Contact US: help@patsnap.com