Aluminum alloy smelting process
A technology of aluminum alloy and smelting tools, which is applied in the field of aluminum alloy smelting, can solve problems such as ambiguity and affecting production efficiency, and achieve the effects of reducing adverse effects and improving mechanical properties and corrosion resistance
- Summary
- Abstract
- Description
- Claims
- Application Information
AI Technical Summary
Problems solved by technology
Method used
Image
Examples
Embodiment Construction
[0019] The following examples can enable those skilled in the art to understand the present invention more comprehensively, but the present invention is not limited to the scope of the described examples.
[0020] An aluminum alloy smelting process has the following steps:
[0021] S1: Aluminum alloy smelting tool preparation: clean the oxide skin and debris on the surface of the ladle, overflow pipe and spoon used in the smelting process, and evenly spread it on the surface of the ladle, overflow pipe and spoon Apply paint.
[0022] S2: Cleaning of the crucible: Clean and remove the dross and oxide layer on the surface of the crucible that needs to melt aluminum alloy, heat the crucible to 250°C-300°C, and then evenly spray paint on the inner wall of the crucible.
[0023] S3: Aluminum ingot treatment: remove the aluminum rust, oil stain and dust on the surface of the aluminum ingot for later use.
[0024] S4: Melting of aluminum ingots: Add the processed aluminum ingots an...
PUM
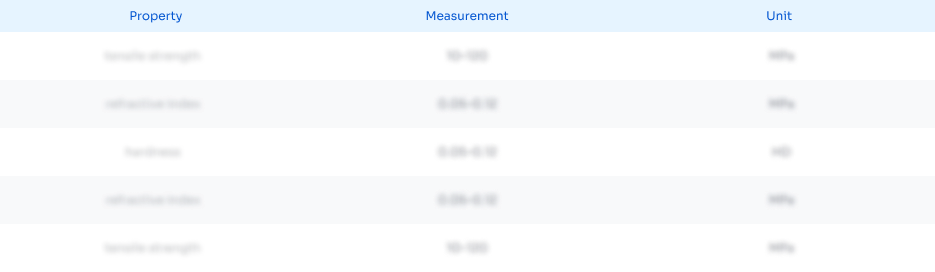
Abstract
Description
Claims
Application Information

- Generate Ideas
- Intellectual Property
- Life Sciences
- Materials
- Tech Scout
- Unparalleled Data Quality
- Higher Quality Content
- 60% Fewer Hallucinations
Browse by: Latest US Patents, China's latest patents, Technical Efficacy Thesaurus, Application Domain, Technology Topic, Popular Technical Reports.
© 2025 PatSnap. All rights reserved.Legal|Privacy policy|Modern Slavery Act Transparency Statement|Sitemap|About US| Contact US: help@patsnap.com