Anti-shelling and easy-to-fill casting sand
A casting mold and uniform mixing technology, which is applied in the field of foundry sand, can solve problems such as shelling and easy core penetration, and achieve the effect of eliminating shelling, reducing the tendency of shelling, and improving the hardening rate
- Summary
- Abstract
- Description
- Claims
- Application Information
AI Technical Summary
Problems solved by technology
Method used
Image
Examples
Embodiment 1
[0015] An anti-shelling and easy-filling foundry sand, which is made of the following raw materials in parts by weight: talcum powder 13, fly ash 24, apatite powder 5, zeolite 19, forsterite fine powder 15-3728, dialkyl di Zinc thiophosphate 2, silicon potassium fluoride 5, geopolymer prepolymer 3, organic bentonite 9, sodium tripolyphosphate 3, polyvinyl butyral 4, clay 180, additives 19; said additives Made from the following raw materials in equivalent parts by weight: magnesium hydroxide 5.6, polysilicon solid waste 8.5, carbon black 1.5, cashew nut shell liquid 0.7, phenolic resin 2.3, benzoxazine resin 1.6, syrup 2.3, xanthan gum 1.2, ethanol 1 part, acrylic acid emulsion 0.8; the preparation method of adding additives is as follows: mix magnesium hydroxide, polysilicon solid waste, and carbon black, perform ball milling, pass through a 150-mesh sieve, add ethanol and acrylic acid emulsion, stir evenly, and then add phenolic resin , stir evenly, granulate, the particle s...
Embodiment 2
[0022] An anti-shelling and easy-filling foundry sand, made of the following raw materials in parts by weight: talcum powder 15, fly ash 26, apatite powder 7, zeolite 28, forsterite fine powder 26, dialkyl dithio Zinc phosphate 2.5, silicon potassium fluoride 7, geopolymer prepolymer 4, organic bentonite 13, sodium tripolyphosphate 4, polyvinyl butyral 5, clay 190, additive 18; the additive consists of the following Made from raw materials in equivalent parts by weight: 6.3 parts of magnesium hydroxide, 9.3 parts of polycrystalline silicon solid waste, 2 parts of carbon black, 1 part of cashew nut shell liquid, 3.2 parts of phenolic resin, 1.8 parts of benzoxazine resin, 2 parts of syrup, 1.4 parts of xanthan gum, and 2.3 parts of ethanol , acrylic acid emulsion 1.3; the preparation method of adding additives is: mix magnesium hydroxide, polycrystalline silicon solid waste, carbon black, carry out ball milling, cross 150 mesh sieves, add ethanol and acrylic acid emulsion, stir ...
PUM
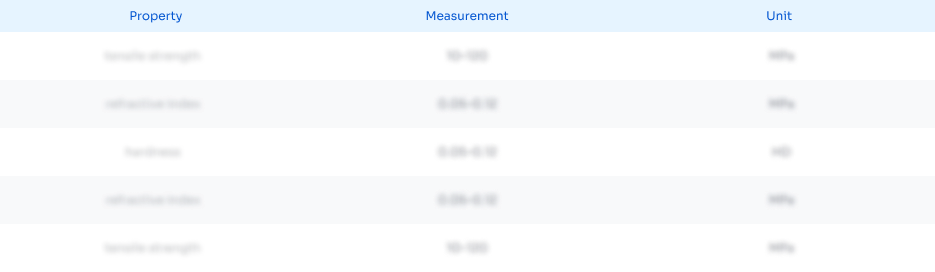
Abstract
Description
Claims
Application Information

- R&D
- Intellectual Property
- Life Sciences
- Materials
- Tech Scout
- Unparalleled Data Quality
- Higher Quality Content
- 60% Fewer Hallucinations
Browse by: Latest US Patents, China's latest patents, Technical Efficacy Thesaurus, Application Domain, Technology Topic, Popular Technical Reports.
© 2025 PatSnap. All rights reserved.Legal|Privacy policy|Modern Slavery Act Transparency Statement|Sitemap|About US| Contact US: help@patsnap.com