A kind of rubber powder modified asphalt mastic macadam mixture and preparation method thereof
A technology of modified asphalt and mastic, applied in the direction of climate sustainability, sustainable waste treatment, solid waste management, etc., can solve the problems of poor road quality, insufficient bonding strength, short service life, etc., and achieve good road quality , the surface roughness is improved, and the effect of reducing dissipation
- Summary
- Abstract
- Description
- Claims
- Application Information
AI Technical Summary
Problems solved by technology
Method used
Examples
Embodiment 1
[0042] A rubber powder modified asphalt prepared through the following steps:
[0043] S1. Weigh the following materials by weight: 10 parts of 10-30 mesh waste bias tire rubber powder, 0.6 part of pentaerythritol tetramercaptoacetate, 60 parts of 90# road petroleum asphalt, slow-cracking and slow-setting cationic asphalt emulsifier BH- 1 part of MM, 3 parts of rosin glyceride;
[0044] S2. Completely immerse the waste tire rubber powder in water, add potassium ferrate with 1% of the total weight of water, keep stirring and soaking at a speed of 20 rpm at 30°C for 1 hour, and then grind the obtained 30-80 mesh particles under wet conditions shape substance;
[0045] S3, melt 90# road petroleum asphalt at 140-150°C, heat up to 170-190°C, add pre-heated rosin glyceride, stir evenly, add the granular substance obtained in step S2, and Stir at 180-190°C for 1 hour to prepare waste rubber powder composite modified asphalt with high fatigue resistance and crack resistance.
Embodiment 2
[0047] A rubber powder modified asphalt prepared through the following steps:
[0048] S1, take the following materials by weight: 10 parts of 10-30 mesh waste bias tire rubber powder, 0.6 part of pentaerythritol tetramercaptoacetate, 60 parts of 130# road petroleum asphalt, 3 parts of rosin glyceride;
[0049] S2. Completely immerse the waste bias tire rubber powder in water, add potassium ferrate with 1% of the total weight of water, and keep stirring and soaking at a speed of 20 rpm at 30°C for 1 hour, then grind the obtained 30-80% under wet conditions. Particulate matter of interest;
[0050] S3, melt 130# road petroleum asphalt at 140-150°C, heat up to 170-190°C, add rosin glycerides that are preheated to liquid state, stir well, add pentaerythritol tetramercaptoacetate and step S2 The obtained granular material was stirred at 180-190° C. for 1 hour to obtain rubber powder modified asphalt.
Embodiment 3
[0052] A rubber powder modified asphalt prepared through the following steps:
[0053] S1, weigh the following materials by weight: 30 parts of 10-30 mesh waste radial tire rubber powder, 0.6 part of pentaerythritol tetramercapto butyrate, 90 parts of 70# road petroleum asphalt, 4 parts of isobutyl stearate;
[0054] S2. Completely immerse the waste radial tire rubber powder in water, add potassium ferrate of 1% of the total weight of water, and keep stirring and soaking at a speed of 30rpm at 25°C for 0.5h, then grind the obtained 30-80% under wet conditions. Particulate matter of interest;
[0055] S3, melt 70# road petroleum asphalt at 140-150°C, heat up to 170-190°C, add isobutyl stearate preheated to liquid state, stir well, add pentaerythritol tetramercaptobutyrate and the granular substance obtained in step S2, and stirred at 180-190° C. for 2 hours to obtain rubber powder modified asphalt.
PUM
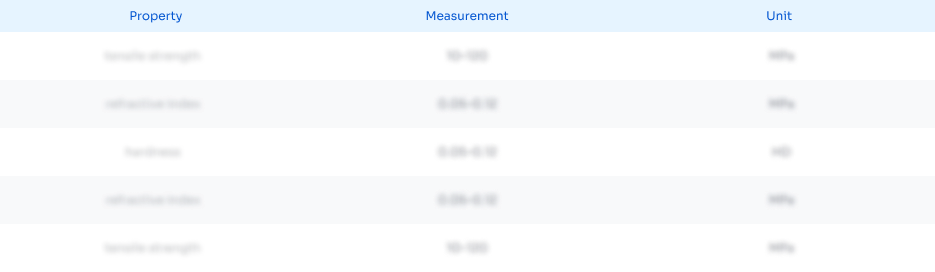
Abstract
Description
Claims
Application Information

- R&D Engineer
- R&D Manager
- IP Professional
- Industry Leading Data Capabilities
- Powerful AI technology
- Patent DNA Extraction
Browse by: Latest US Patents, China's latest patents, Technical Efficacy Thesaurus, Application Domain, Technology Topic, Popular Technical Reports.
© 2024 PatSnap. All rights reserved.Legal|Privacy policy|Modern Slavery Act Transparency Statement|Sitemap|About US| Contact US: help@patsnap.com