Knitted fabric capable of improving flame-retardant performance and preparation method thereof
A technology for knitted fabrics and flame retardant properties, applied in the field of knitted fabrics with improved flame retardant properties and their preparation, can solve problems such as poor flame retardant properties, and achieve the effects of improved flame retardant properties, good toughness, and improved overall performance
- Summary
- Abstract
- Description
- Claims
- Application Information
AI Technical Summary
Problems solved by technology
Method used
Examples
Embodiment 1
[0030] The knitted fabric with improved flame retardancy of this embodiment includes the following raw materials in parts by weight:
[0031] Pretreated bamboo fiber 24 parts, polypropylene fiber 16 parts, pure cotton 12 parts, needle-like wollastonite powder 8 parts, flame retardant reinforcing agent 6 parts, sepiolite fiber 4 parts, sodium silicate 2 parts, hindered phenol 1 part , 4 parts of microporous bamboo charcoal, 1 part of mullite powder.
[0032] The preparation method of the pretreated bamboo fiber in this embodiment is to send the bamboo fiber into boiling water and boil it for 35 minutes, then add isopropyl triisostearate titanate for reflux, reflux for 12 minutes, the reflux temperature is 65 ℃, and then send it to the barrier Soak in the combustion aid for 25 minutes, take it out and dry, and get the pretreated bamboo fiber.
[0033] The flame retardant auxiliary agent of this embodiment is a mixture of ammonium chloride and ammonium bromide in a weight ratio of 3:1....
Embodiment 2
[0042] The knitted fabric with improved flame retardancy of this embodiment includes the following raw materials in parts by weight:
[0043] Pretreated bamboo fiber 30 parts, polypropylene fiber 22 parts, pure cotton 14 parts, needle-like wollastonite powder 12 parts, flame retardant reinforcing agent 10 parts, sepiolite fiber 8 parts, sodium silicate 5 parts, hindered phenol 3 parts , 8 parts of microporous bamboo charcoal, 3 parts of mullite powder.
[0044] The preparation method of the pretreated bamboo fiber in this embodiment is to send the bamboo fiber into boiling water for 45 minutes, then add isopropyl triisostearate titanate for reflux, reflux for 16 minutes, the reflux temperature is 75 ℃, and then send it to the barrier Soak in the combustion aid for 35 minutes, take it out and dry, and get the pretreated bamboo fiber.
[0045] The flame retardant auxiliary agent of this embodiment is a mixture of ammonium chloride and ammonium bromide in a weight ratio of 6:1.
[0046]...
Embodiment 3
[0054] The knitted fabric with improved flame retardancy of this embodiment includes the following raw materials in parts by weight:
[0055] Pretreated 27 parts of bamboo fiber, 18 parts of polypropylene fiber, 13 parts of pure cotton, 10 parts of acicular wollastonite powder, 8 parts of flame retardant reinforcing agent, 6 parts of sepiolite fiber, 3.5 parts of sodium silicate, 2 parts of hindered phenol , 6 parts of microporous bamboo charcoal, 2 parts of mullite powder.
[0056] The preparation method of the pretreated bamboo fiber in this embodiment is to send the bamboo fiber into boiling water for 40 minutes, then add isopropyl triisostearate titanate for reflux, reflux for 14 minutes, the reflux temperature is 70 ℃, and then send it into the barrier Soak in the combustion aid for 30 minutes and take it out to dry to obtain pretreated bamboo fiber.
[0057] The flame retardant auxiliary in this embodiment is a mixture of ammonium chloride and ammonium bromide in a weight rati...
PUM
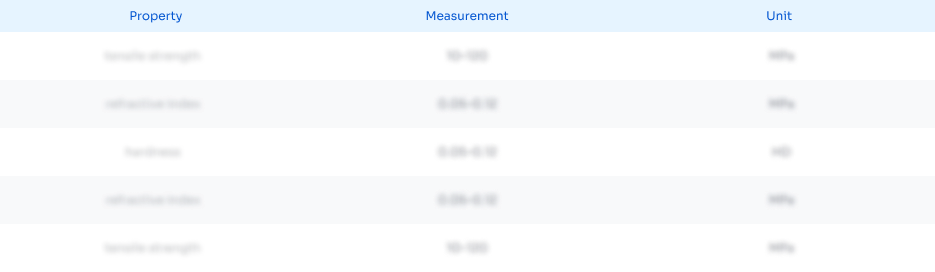
Abstract
Description
Claims
Application Information

- R&D
- Intellectual Property
- Life Sciences
- Materials
- Tech Scout
- Unparalleled Data Quality
- Higher Quality Content
- 60% Fewer Hallucinations
Browse by: Latest US Patents, China's latest patents, Technical Efficacy Thesaurus, Application Domain, Technology Topic, Popular Technical Reports.
© 2025 PatSnap. All rights reserved.Legal|Privacy policy|Modern Slavery Act Transparency Statement|Sitemap|About US| Contact US: help@patsnap.com