A twist-extrusion composite strong-plastic forming method and process device
A process device and combined technology, applied in the field of metal plastic processing, can solve the problems of difficult to form high-performance plate/cylinder components, and achieve the effect of avoiding grain growth and large plastic deformation.
- Summary
- Abstract
- Description
- Claims
- Application Information
AI Technical Summary
Problems solved by technology
Method used
Image
Examples
example 1
[0030] Example 1: A torsion-extrusion combined strong-plastic forming method and process device for a magnesium alloy cylindrical part are described in detail in conjunction with the accompanying drawings.
[0031] Such as figure 1 As shown, in the twisting-extrusion combined strong-plastic forming process device for a magnesium alloy cylindrical part, the extruded blank is cylindrical, such as image 3 shown. The steps to use the forming process device are:
[0032] The first step: fix the upper mold seat cover 6, the punch 9 and the backing plate 7 on the upper template 8 by bolts;
[0033] Step 2: Fix the upper template 8 to the slider of the hydraulic press, and fix the lower template 2 to the workbench of the hydraulic press;
[0034] The third step: install the rolling bearing 3 in the groove of the lower template 2;
[0035] Step 4: Fix the lower die 4 on the lower template 2;
[0036] Step 5: Install the rotating head 1 on the rolling bearing 3, and place it in th...
example 2
[0043] Example 2: Combine Figure 6 To illustrate this embodiment, in the twisting-extrusion compound strong-plastic forming process device for magnesium alloy plate-shaped parts, the extruded blank is a square block, such as Figure 7 shown. The combined die of this example is composed of an upper die 5 and a lower die 4; the combined die is fixed on the lower template 2 through the lower mold seat cover 12, and when the blank 10 is extruded, the extrusion speed is V 2 , the rotational speed of the rotating head is W 2 , the metal at the lower end of the billet 10 is subjected to the torsional shearing action of the rotary head 1, and can obtain a fine-grained structure. As the extrusion deformation continues, the metal begins to flow along the concave mold cavity to both sides, forming a plate 13, as Figure 8 shown.
example 3
[0044] Example 3: In the seventh step of this example, the blank 10 is aluminum and its alloys, titanium and its alloys, and a light metal material that is difficult to deform and has better plasticity.
[0045] It should be noted that the specific type of components with complex features depends mainly on the cavity characteristics of the combined die.
PUM
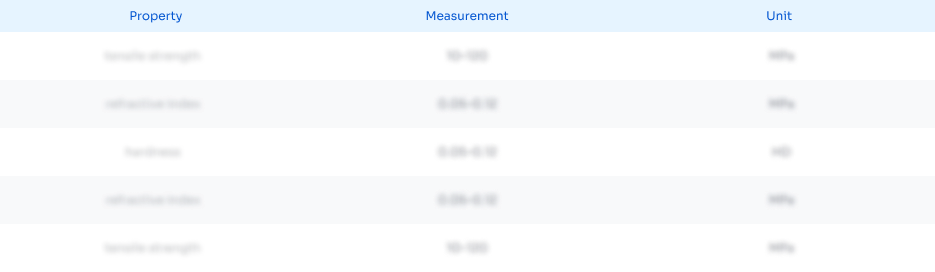
Abstract
Description
Claims
Application Information

- R&D
- Intellectual Property
- Life Sciences
- Materials
- Tech Scout
- Unparalleled Data Quality
- Higher Quality Content
- 60% Fewer Hallucinations
Browse by: Latest US Patents, China's latest patents, Technical Efficacy Thesaurus, Application Domain, Technology Topic, Popular Technical Reports.
© 2025 PatSnap. All rights reserved.Legal|Privacy policy|Modern Slavery Act Transparency Statement|Sitemap|About US| Contact US: help@patsnap.com