Efficient ultra-precise shear thickening and chemical synergy polishing method
An ultra-precision and high-efficiency technology, applied in the direction of grinding/polishing equipment, polishing compositions containing abrasives, manufacturing tools, etc., can solve the problems of unguaranteed processing, difficult part size and geometric shape accuracy, small range of processed materials, etc. problems, to achieve the effect of improving the certainty of removal, reducing the surface metamorphic layer, and improving the processing efficiency
- Summary
- Abstract
- Description
- Claims
- Application Information
AI Technical Summary
Problems solved by technology
Method used
Image
Examples
Embodiment 1
[0040] Such as figure 1 , figure 2 As shown, when the present invention is used for processing size: length * width * height 30mm * 30mm * 6mm silicon nitride material plane workpiece, its processing steps are as follows:
[0041] 1) The workpiece is fixed on the polishing fixed plate 31 of the implementation equipment, and three workpieces and their polishing processing system 29 are clamped at the same time, which is conducive to improving production efficiency.
[0042] 2) Configure high-efficiency shear thickening-chemical synergistic polishing fluid, and prepare the following components by mass percentage: polishing abrasive diamond (or SiO 2 , SiC) 15%, shear thickening reinforcement phase 25%, water 50% and green chemical environmental protection substances 10%; first, the polishing abrasive grains and shear thickening reinforcement phase are fully mixed in the mixer for 12 hours, then, Add the mixture of SiC and shear thickening enhancement phase to water, and stir ...
Embodiment 2
[0048] Such as image 3 As shown, when the present invention is used for processing dimension parameter and is: diameter 40mm, when the optical glass material concave surface workpiece of focal length 100mm, its operation steps are as follows:
[0049] 1) Fix the workpiece on the polishing fixed plate 31 of the implementation equipment, and clamp two workpieces and their polishing processing system 29 at the same time, which is beneficial to improve production efficiency.
[0050] 2) Configure high-efficiency shear thickening-chemical synergistic polishing fluid, prepare the following mass percentages of polishing micropowder cerium oxide 20%, shear thickening reinforcement phase 30%, water 45% and green chemical environmental protection substances 5%; first cerium oxide Mix well with the shear thickening enhancement phase in a mixer for 12 hours, then add the mixture of cerium oxide and shear thickening enhancement into water, and stir for a certain period of time to a unifor...
Embodiment 3
[0056] Such as Figure 4 As shown, when the present invention is used to process the convex optical glass with a diameter of 30mm and a focal length of 80mm, the steps are as follows:
[0057] 1) The workpiece is fixed on the polishing fixed plate 31 of the implementation equipment, and three workpieces and their polishing processing system 29 are clamped at the same time, which is conducive to improving production efficiency.
[0058] 2) Configure high-efficiency shear thickening-chemical synergistic polishing fluid, and prepare the following mass percentage of polishing micropowder Al 2 o 310%, shear thickening reinforcement phase 25%, water 39% and green chemical environmental protection substances 26%; Al 2 o 3 Mix well with the shear thickening enhancement phase in a mixer for 12 hours, then add the mixture into water and stir for a certain period of time until it reaches a uniform state, then mix in green chemical environmental protection substances at 25°C to make a ...
PUM
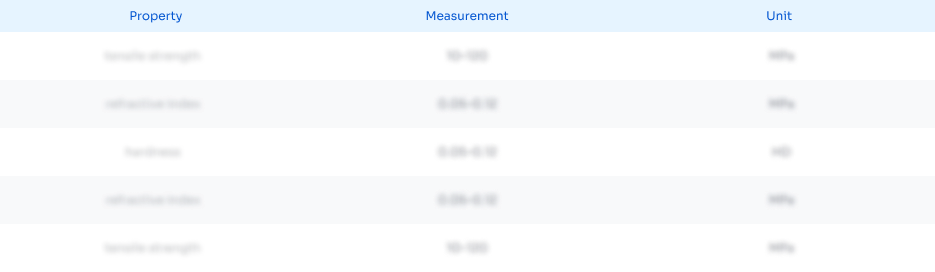
Abstract
Description
Claims
Application Information

- R&D Engineer
- R&D Manager
- IP Professional
- Industry Leading Data Capabilities
- Powerful AI technology
- Patent DNA Extraction
Browse by: Latest US Patents, China's latest patents, Technical Efficacy Thesaurus, Application Domain, Technology Topic, Popular Technical Reports.
© 2024 PatSnap. All rights reserved.Legal|Privacy policy|Modern Slavery Act Transparency Statement|Sitemap|About US| Contact US: help@patsnap.com