High-carbon high-chromium stainless steel and processing method thereof
A high-carbon, high-chromium, processing method technology, applied in the field of stainless steel processing, can solve the problems of affecting the service life of the product, the narrow deformation temperature range, and the uneven temperature of the steel ingot, so as to simplify the production process, reduce the production cost, and increase the billet rate Effect
- Summary
- Abstract
- Description
- Claims
- Application Information
AI Technical Summary
Problems solved by technology
Method used
Examples
preparation example Construction
[0037] In the present application, the method for preparing the high-carbon and high-chromium stainless steel ingot can adopt conventional methods in the art. For example, it may include: primary smelting of raw and auxiliary materials such as scrap steel and alloys in an electric furnace to obtain molten steel, tapping the molten steel into a ladle, performing pre-deoxidation alloying and carburization on the molten steel during the tapping process, and then Alloy fine-tuning and temperature adjustment are carried out in the refining furnace, and then vacuum refining is carried out, and the obtained molten steel is cast into shape, so that in the obtained steel ingot of high-carbon and high-chromium stainless steel, the content of carbon is 0.90-1.20wt%, and the content of chromium is 17.00-19.00 wt%; the content of carbon and chromium in the high-carbon and high-chromium stainless steel ingot can be adjusted by controlling the amount of carburizing agent and alloy added in th...
Embodiment 1
[0052] The present embodiment provides a kind of high-carbon high-chromium stainless steel processing method, and it specifically comprises the following steps:
[0053] S11. The electric furnace molten steel prepared by the VOD refining furnace is poured, and the steel ingot is delivered with a mold and a cap at the 90th minute after the pouring is completed. The steel ingot is a 9Cr18MoV steel ingot, and its ingot shape is a 3.35-ton rectangular ingot. The loading time of furnace steel ingots is controlled at 45 minutes, and the ingots are directly transported by car; the transportation time of steel ingots is controlled within 15 minutes.
[0054] S12. The steel ingot is removed from the cap and mold, furnace is loaded and heated in sequence, and the total time of the cap removal and furnace load process is controlled to be 35 minutes. After the furnace is installed and before the heating is implemented, the surface temperature of the steel ingot is between 800-880 ° C. Dur...
Embodiment 2
[0058] The present embodiment provides a kind of high-carbon high-chromium stainless steel 9Cr18Mo steel red feeding and blooming method, which specifically includes the following steps:
[0059] S21. The electric furnace molten steel prepared by the VOD refining furnace is poured, and the steel ingot is delivered with a mold and a cap after 90 minutes from the completion of the pouring. The steel ingot is a 9Cr18Mo steel ingot, and its ingot shape is a 3.35-ton rectangular ingot. The loading time of each furnace of ingots in the pit is controlled to 45 minutes, and the ingots are directly transported by car; the transportation time of steel ingots is controlled within 15 minutes.
[0060] S22, the steel ingot is removed from the cap and demoulding, furnace charging and heating in sequence, and the total time of the cap removal and demoulding process and the furnace charging process is controlled to be 35 minutes. After the furnace charging is implemented and before the heating...
PUM
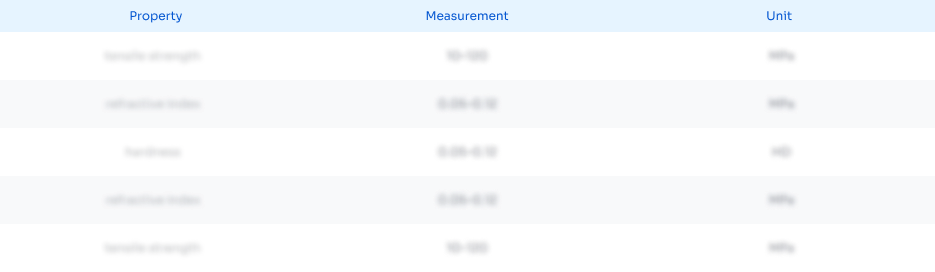
Abstract
Description
Claims
Application Information

- Generate Ideas
- Intellectual Property
- Life Sciences
- Materials
- Tech Scout
- Unparalleled Data Quality
- Higher Quality Content
- 60% Fewer Hallucinations
Browse by: Latest US Patents, China's latest patents, Technical Efficacy Thesaurus, Application Domain, Technology Topic, Popular Technical Reports.
© 2025 PatSnap. All rights reserved.Legal|Privacy policy|Modern Slavery Act Transparency Statement|Sitemap|About US| Contact US: help@patsnap.com