Sulfurized polythiol-rich lithium-sulfur battery cathode composite material and preparation method thereof
A composite material and lithium-sulfur battery technology, applied in the field of composite materials, can solve the problems of further improvement of discharge specific capacity, low ion and electronic conductivity, volume change of active electrode, etc., to reduce experimental cost and process complexity, The effect of increasing the attachment point and increasing the sulfur loading capacity
- Summary
- Abstract
- Description
- Claims
- Application Information
AI Technical Summary
Problems solved by technology
Method used
Image
Examples
Embodiment 1
[0026] (1) Preparation of graphene oxide: prepare a sulfuric acid / phosphoric acid mixture with a volume ratio of 9:1, control the temperature at 35-40 degrees Celsius, slowly add a mixture of 3.0 grams of graphite flakes and 18.0 grams of potassium permanganate to the prepared In the acid solution, stir for 12 hours; cool the reaction to room temperature, add 9 ml of hydrogen peroxide to make the solution turn yellow; centrifuge for 3 minutes, add 400 ml of ethanol, 200 ml of concentrated hydrochloric acid and 200 ml of water; after several times of centrifugation, finally measure the pH value 6-7, close to neutral, wash and add water before each centrifugation, and put the final concentrated colloid into the container for use;
[0027] (2) 20 milliliters of graphene oxide obtained in step (1) are added to a round-bottomed flask containing magnetons, 50 milliliters of deionized water is added, and then 0.5 gram of L-cysteine hydrochloride is added to dissolve completely Fina...
Embodiment 2
[0031] (1) Preparation of graphene oxide: prepare a sulfuric acid / phosphoric acid mixture with a volume ratio of 9:1, control the temperature at 35-40 degrees Celsius, and slowly add a mixture of 1.0 grams of graphite flakes and 10.0 grams of potassium permanganate to the prepared In the acid solution, stir for 10 hours; cool the reaction to room temperature, add 3 ml of hydrogen peroxide to make the solution turn yellow; centrifuge for 2 minutes, add 200 ml of ethanol, 140 ml of concentrated hydrochloric acid and 140 ml of water; after several times of centrifugation, finally measure the pH value 6-7, close to neutral, wash and add water before each centrifugation, and put the final concentrated colloid into the container for use;
[0032] (2) Add 10 milliliters of graphene oxide obtained in step (1) into a round-bottomed flask containing magnetons, add 35 milliliters of deionized water, then add 0.2 gram of L-cysteine hydrochloride, and dissolve completely Finally, adjust ...
Embodiment 3
[0035] (1) Preparation of graphene oxide: prepare a sulfuric acid / phosphoric acid mixture with a volume ratio of 9:1, control the temperature at 35-40 degrees Celsius, slowly add a mixture of 2.0 grams of graphite flakes and 12.0 grams of potassium permanganate to the prepared In the acid solution, stir for 8 hours; cool the reaction to room temperature, add 6 ml of hydrogen peroxide to make the solution turn yellow; centrifuge for 1 minute, add 300 ml of ethanol, 100 ml of concentrated hydrochloric acid and 100 ml of water; after several times of centrifugation, finally measure the pH value 6-7, close to neutral, wash and add water before each centrifugation, and put the final concentrated colloid into the container for use;
[0036] (2) Add 5 milliliters of graphene oxide obtained in step (1) into a round-bottomed flask containing magnetons, add 20 milliliters of deionized water, then add 0.3 gram of L-cysteine hydrochloride, and dissolve completely Finally, adjust the pH ...
PUM
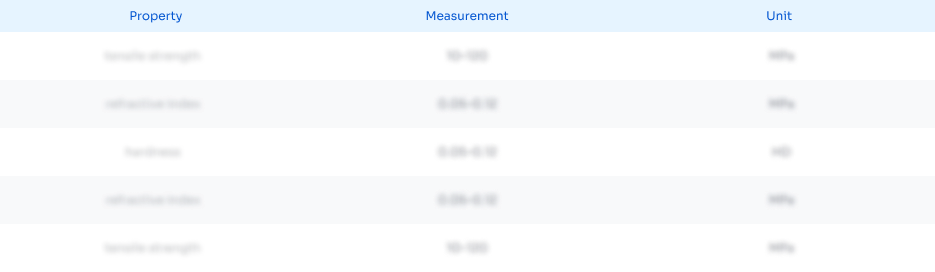
Abstract
Description
Claims
Application Information

- Generate Ideas
- Intellectual Property
- Life Sciences
- Materials
- Tech Scout
- Unparalleled Data Quality
- Higher Quality Content
- 60% Fewer Hallucinations
Browse by: Latest US Patents, China's latest patents, Technical Efficacy Thesaurus, Application Domain, Technology Topic, Popular Technical Reports.
© 2025 PatSnap. All rights reserved.Legal|Privacy policy|Modern Slavery Act Transparency Statement|Sitemap|About US| Contact US: help@patsnap.com