Preparation method of anode material compounding three-dimensional porous silicon doped titanium source with carbon
A three-dimensional porous, negative electrode material technology, applied in the direction of negative electrode, battery electrode, active material electrode, etc., can solve the problem that the volume expansion effect of silicon cannot be effectively eliminated, and achieve improved cycle stability, high specific capacity, and stable discharge voltage Effect
- Summary
- Abstract
- Description
- Claims
- Application Information
AI Technical Summary
Problems solved by technology
Method used
Examples
Embodiment 1
[0025] Mix aluminum powder: silicon dioxide uniformly according to the mass ratio of 4:1, put it into a high-temperature carbonization furnace, pass through a protective atmosphere (argon / nitrogen), heat at 600°C for 5 hours, and immerse the obtained sample in hydrogen first Fluoric acid solution (50wt%) for 12 hours, then washed with ethanol and distilled water for 4 times, and finally vacuum-dried at 80°C for 12 hours to obtain porous silicon; Add porous silicon and absolute ethanol, then add butyl titanate and grind for 2 hours to obtain a nano-slurry; ③The obtained nano-mixed slurry is spray-dried at an inlet temperature of 250°C and an outlet temperature of 90°C to obtain a precursor; ④The obtained precursor is baked at 500°C for 2 hours in a nitrogen protective atmosphere, and then cooled to room temperature; ⑤Through the dried material through a 250-mesh sieve, use the organic gas acetylene containing hydrocarbons as the carbon source, and nitrogen as the protective atmo...
Embodiment 2
[0027] Mix aluminum powder: silicon dioxide evenly according to the mass ratio of 1:1, then put it into a high-temperature carbonization furnace, pass through a protective atmosphere (argon / nitrogen), heat at 700°C for 7 hours, and first immerse the obtained sample in hydrogen Fluoric acid solution (50wt%) for 12 hours, then washed with ethanol and distilled water for 4 times, and finally vacuum-dried at 80°C for 12 hours to obtain porous silicon; ② Pass porous silicon through a 250-mesh sieve and add Porous silicon and absolute ethanol were added to grind for 5 hours to obtain a nano-slurry; ③The obtained nano-mixed slurry was spray-dried at an inlet temperature of 250°C and an outlet temperature of 90°C to obtain a precursor; ④Obtained The precursor of the precursor is under a nitrogen protective atmosphere, the calcination temperature is 650 ° C, the time is 4.5 hours, and cooled to room temperature; ⑤ Pass the dried material through a 250-mesh sieve, use the organic gas ace...
Embodiment 3
[0029] Aluminum powder: silicon dioxide is mixed evenly according to the mass ratio of 2:1, put into a high-temperature carbonization furnace, pass through a protective atmosphere (argon / nitrogen), heat at 700°C for 7 hours, and first immerse the obtained sample in hydrogen fluoride acid solution (50wt%) for 12 hours, then washed with ethanol and distilled water for 4 times, and finally vacuum-dried at 80°C for 12 hours to obtain porous silicon; Silicon and absolute ethanol, and then added butyl titanate to grind for 6 hours to obtain a nano-slurry; ③The obtained nano-mixed slurry was spray-dried at an inlet temperature of 350°C and an outlet temperature of 90°C to obtain a precursor; ④The obtained Precursors were baked at 900°C for 7 hours in a nitrogen protective atmosphere, and cooled to room temperature; ⑤ Pass the dried material through a 250-mesh sieve, use the organic gas acetylene containing hydrocarbons as the carbon source, and nitrogen as the protective atmosphere, a...
PUM
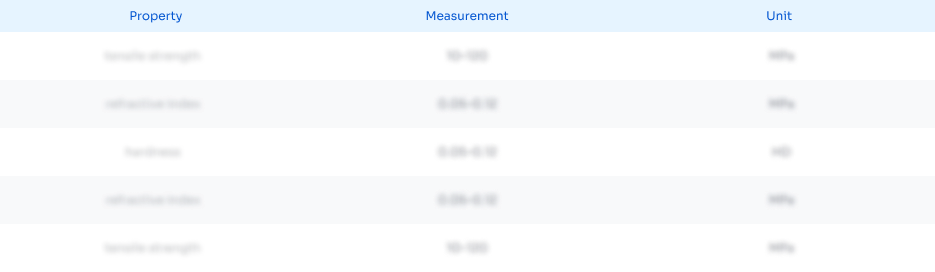
Abstract
Description
Claims
Application Information

- R&D
- Intellectual Property
- Life Sciences
- Materials
- Tech Scout
- Unparalleled Data Quality
- Higher Quality Content
- 60% Fewer Hallucinations
Browse by: Latest US Patents, China's latest patents, Technical Efficacy Thesaurus, Application Domain, Technology Topic, Popular Technical Reports.
© 2025 PatSnap. All rights reserved.Legal|Privacy policy|Modern Slavery Act Transparency Statement|Sitemap|About US| Contact US: help@patsnap.com