Preparation method of high-intensity and high-impact-resistance polystyrene
A polystyrene, high-impact technology, applied in the field of polymer material preparation, can solve problems such as market expansion restrictions of polystyrene, and achieve the effects of stable and controllable product performance, simple ingredients, and excellent impact resistance.
- Summary
- Abstract
- Description
- Claims
- Application Information
AI Technical Summary
Problems solved by technology
Method used
Image
Examples
Embodiment 1
[0028] A method for preparing high-strength, high-impact polystyrene that integrates nano-nucleating agents and rigid body synergistic effects using mechanical blending technology, comprising the following steps:
[0029] a. Raw material pretreatment:
[0030] Dry the raw polystyrene pellets at 55°C for 4 hours, dry the nano-calcium carbonate at 130°C for 4 hours; dry A2520 at 130°C for 4 hours; take the lubricant pentaerythritol stearate for use ;
[0031] b. Ingredients and mixing:
[0032] The surface treatment of the nucleating agent is completed in a reactor (for example: a three-necked flask or a reaction kettle, the same hereinafter). Add nano-calcium carbonate and KH-550 (KH-550 is prepared as an ethanol solution with a concentration of 0.5% by mass percentage) that accounts for 0.2% of the mass of nano-calcium carbonate in the reactor; after stirring evenly, heat and reflux for 8 hours. Suction filtration and collecting the filter cake, drying and grinding the filt...
Embodiment 2
[0037] A method for preparing high-strength, high-impact polystyrene that integrates nano-nucleating agents and rigid body synergistic effects using mechanical blending technology, comprising the following steps:
[0038] a. Raw material pretreatment:
[0039] Dry the raw polystyrene pellets at 80°C for 4 hours, dry the nano attapulgite at 110°C for 4 hours; dry A2590 at 110°C for 4 hours; take the lubricant pentaerythritol stearate for use ;
[0040] b. Ingredients and mixing:
[0041] The surface treatment of the nucleating agent is done in the reactor. Add nano-attapulgite and 0.2% KH-550 (KH-550 is prepared as an ethanol solution with a mass percentage concentration of 0.5%) to the reactor; after stirring evenly, heat to reflux for 8 hours. Suction filtration and collecting the filter cake, drying and grinding the filter cake to obtain a surface-treated nucleating agent-surface-treated nano-attapulgite for use;
[0042] Take 92 parts by mass of dried raw polystyrene, 5 p...
Embodiment 3
[0046] A method for preparing high-strength, high-impact polystyrene that integrates nano-nucleating agents and rigid body synergistic effects using mechanical blending technology, comprising the following steps:
[0047] a. Raw material pretreatment:
[0048] Dry the raw polystyrene pellets at 80°C for 4 hours, dry nano-titanium dioxide at 110°C for 4 hours; dry the PMMA@NR core-shell resin at 110°C for 4 hours; take the lubricant pentaerythritol hard fatty acid ester for use;
[0049] b. Ingredients and mixing:
[0050] The surface treatment of the nucleating agent is done in the reactor. Add nano-titanium dioxide and KH-550 with a mass of 0.2% of the mass of nano-titanium dioxide to the reactor (KH-550 is prepared as an ethanol solution with a mass percentage concentration of 0.5%); after stirring evenly, heat and reflux for 8 hours. Suction filtration and collecting the filter cake, drying and grinding the filter cake to obtain a surface-treated nucleating agent-surface...
PUM
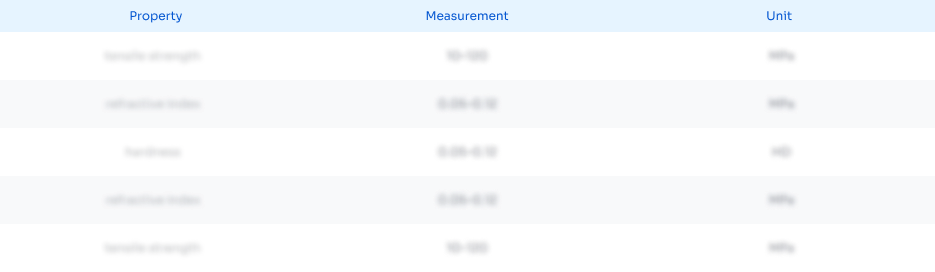
Abstract
Description
Claims
Application Information

- Generate Ideas
- Intellectual Property
- Life Sciences
- Materials
- Tech Scout
- Unparalleled Data Quality
- Higher Quality Content
- 60% Fewer Hallucinations
Browse by: Latest US Patents, China's latest patents, Technical Efficacy Thesaurus, Application Domain, Technology Topic, Popular Technical Reports.
© 2025 PatSnap. All rights reserved.Legal|Privacy policy|Modern Slavery Act Transparency Statement|Sitemap|About US| Contact US: help@patsnap.com