Resin diamond wire and preparation method thereof
A technology of resin diamond wire and resin, which is applied in the direction of manufacturing tools, stone processing equipment, fine working devices, etc., can solve the problems of restricting the performance of resin diamond wire, decrease of diamond holding force, poor effective cutting performance, etc., to achieve excellent holding force, The effect of improving wettability and improving cutting force
- Summary
- Abstract
- Description
- Claims
- Application Information
AI Technical Summary
Problems solved by technology
Method used
Image
Examples
Embodiment 1
[0046]The diamond powder with a D50 of 9.1 μm was subjected to plasma treatment under an oxygen atmosphere, the gas flow rate was 150L / h, the voltage was 30KV, the single treatment volume of the diamond powder was 5000ct, and the treatment time was 30min to obtain a modified diamond abrasive. A slurry was obtained by mixing 36% of polyimide resin, 25% of modified diamond abrasive, 15% of aluminum oxide and 24% of DMF. After the high-carbon steel wire busbar is coated with slurry through the mold, it is dried in a 300°C oven at a speed of 90m / min and wound up, and then post-treated at 220°C for 5h to obtain a resin diamond wire (denoted as S- 1). The morphology and structure of the resulting resin diamond wire can be found in figure 1 , figure 1 It is the topography diagram of the resin diamond wire S-1 obtained in this example.
[0047] Set up the control sample: prepare according to the above preparation process, the difference is that the diamond powder is not subjected t...
Embodiment 2
[0054] The diamond powder with a D50 of 9.1 μm was subjected to plasma treatment under an oxygen atmosphere, the gas flow rate was 150 L / h, the voltage was 20 KV, the single treatment volume of the diamond powder was 5000 ct, and the treatment time was 30 minutes to obtain a modified diamond abrasive. Mix 25% polyimide resin, 30% modified diamond abrasive, 20% copper powder and 25% DMF to obtain a slurry. After the high-carbon steel wire busbar is coated with slurry through the mold, it is dried in a 300°C oven at a speed of 90m / min and wound up, and then post-treated at 220°C for 5h to obtain a resin diamond wire (denoted as S- 2).
[0055] According to the cutting test method of Example 1, the obtained resin diamond wire S-2 was subjected to a cutting test, and the test results showed that the diamond shedding rate was 19%, and the diamond wear rate was 22%. It can be seen that the bond between the modified diamond abrasive and the resin is strong, the grip is firm, the dia...
Embodiment 3
[0057] The diamond powder with a D50 of 9.1 μm was subjected to plasma treatment in an oxygen atmosphere, the gas flow rate was 50 L / h, the voltage was 30 KV, the single treatment volume of the diamond powder was 5000 ct, and the treatment time was 30 minutes to obtain a modified diamond abrasive. 25% of polyimide resin, 30% of modified diamond abrasive, 20% of silicon carbide and 25% of DMF were mixed to obtain a slurry. After the high-carbon steel wire busbar is coated with slurry through the mold, it is dried in an oven at 250°C at a speed of 90m / min and wound up, and then post-treated at 200°C for 6 hours to obtain a resin diamond wire (denoted as S- 3).
[0058] According to the cutting test method of Example 1, the obtained resin diamond wire S-3 was subjected to a cutting test, and the test results showed that the diamond shedding rate was 18%, and the diamond wear rate was 22%. It can be seen that the bond between the modified diamond abrasive and the resin is strong,...
PUM
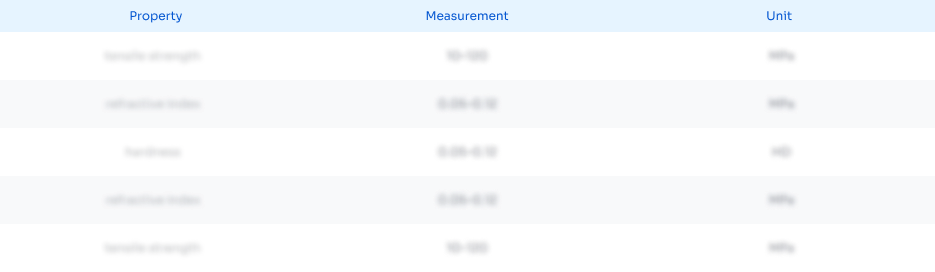
Abstract
Description
Claims
Application Information

- R&D
- Intellectual Property
- Life Sciences
- Materials
- Tech Scout
- Unparalleled Data Quality
- Higher Quality Content
- 60% Fewer Hallucinations
Browse by: Latest US Patents, China's latest patents, Technical Efficacy Thesaurus, Application Domain, Technology Topic, Popular Technical Reports.
© 2025 PatSnap. All rights reserved.Legal|Privacy policy|Modern Slavery Act Transparency Statement|Sitemap|About US| Contact US: help@patsnap.com