Method for preparing acetonitrile from lignocellulosic biomass material
A technology of biomass material and wood fiber, which is applied in the field of organic matter preparation to achieve the effect of low cost
- Summary
- Abstract
- Description
- Claims
- Application Information
AI Technical Summary
Problems solved by technology
Method used
Image
Examples
Embodiment 1
[0047] Embodiment 1: utilize different raw materials to prepare acetonitrile
[0048] In this example, acetonitrile was prepared by catalytic pyrolysis from cellulose, xylan, lignin, corncob, bagasse, rice husk, birch sawdust, sucrose, sorbitol and fructooligosaccharides as raw materials.
[0049] The reaction conditions are as follows: the reaction temperature is 600°C; the catalyst is HZSM-5 molecular sieve; ammonia gas is used as the carrier gas, and the carrier gas flow rate is 80mL / min; the mass ratio of raw material to catalyst is 1:1, and the results are shown in Table 1 below , and the GC spectrogram of the product acetonitrile obtained with cellulose as raw material is shown in the attached figure 1 .
[0050]
[0051] It can be seen from the results in Table 1 that various lignocellulosic biomass materials can produce acetonitrile with high selectivity, the selectivity of acetonitrile in liquid products can be as high as 88.5%, and the yield of acetonitrile can b...
Embodiment 2
[0052] Embodiment 2: utilize different temperature to prepare acetonitrile
[0053] In this embodiment, the influence of different reaction temperatures on the yield and selectivity of acetonitrile was tested.
[0054] The reaction conditions are as follows: the raw material is corncob powder; the catalyst is HZSM-5; ammonia is used as the carrier gas, and the carrier gas flow rate is 80mL / min; the mass ratio of raw material to catalyst is 1:1, and the results are shown in Table 2 below.
[0055]
[0056] It can be seen from the results in Table 2 that when the temperature is too low, for example, at 100° C., the desired product acetonitrile cannot be detected, that is, almost no reaction occurs. In the temperature range from 200°C to 1000°C, as the temperature increased from 200°C to 600°C, the yield of acetonitrile increased from 19.8% to 36.7%, and the selectivity of acetonitrile in liquid products increased from 72.4% to 86.2% while the temperature increased from 600°C...
Embodiment 3
[0057] Embodiment 3: utilize different catalysts to prepare acetonitrile
[0058] In this example, different catalysts were tested for catalytic pyrolysis of corncobs, and the catalysts used were HZSM-5, HY, BETA, MCM-41, SAPO-34, Al 2 o 3 、TiO 2 、MoO 3 / ZrO 2 , SO 4 2- / Fe 2 o 3 , sulfuric acid, nitric acid and hydrochloric acid.
[0059]The reaction conditions are as follows: the raw material is corncob; the reaction temperature is 600°C; ammonia is used as the carrier gas, and the carrier gas flow rate is 80mL / min; the mass ratio of raw material to catalyst is 1:1, and the results are shown in Table 3 below.
[0060]
[0061] As can be seen from the results in Table 3, all kinds of acidic catalysts have a good catalytic effect on the preparation of acetonitrile from corncobs, the yield of acetonitrile is above 30%, and the selectivity of acetonitrile in liquid products is above 73%.
PUM
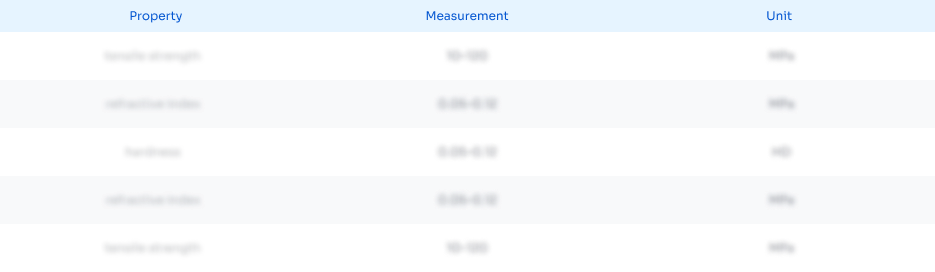
Abstract
Description
Claims
Application Information

- R&D
- Intellectual Property
- Life Sciences
- Materials
- Tech Scout
- Unparalleled Data Quality
- Higher Quality Content
- 60% Fewer Hallucinations
Browse by: Latest US Patents, China's latest patents, Technical Efficacy Thesaurus, Application Domain, Technology Topic, Popular Technical Reports.
© 2025 PatSnap. All rights reserved.Legal|Privacy policy|Modern Slavery Act Transparency Statement|Sitemap|About US| Contact US: help@patsnap.com