Method for preparing metal-matrix composite material by using recovering scrap metal through semi-solid state technology
A composite material and metal-based technology, which is applied in the field of preparing graphene-reinforced magnesium-based composite materials, can solve the problems of uneven dispersion of the reinforced phase, environmental pollution, poor bonding between the reinforced phase and the metal matrix interface, etc., and achieve good spheroidization effect, Composite and enhance interfacial bonding, beneficial effect of wetting
- Summary
- Abstract
- Description
- Claims
- Application Information
AI Technical Summary
Problems solved by technology
Method used
Examples
Embodiment 1
[0048] (1) add 0.18g graphene in the analysis alcohol of 150ml, 99.99%, utilize ultrasonic dispersion treatment 20min, make graphene disperse evenly, after processing, pure 59.82gAZ91D magnesium alloy chips are added in gained graphene alcohol solution, machine Stir (400rm / min) and ultrasonically disperse for 40 minutes at the same time, so that the AZ91D magnesium alloy chips and graphene are evenly mixed without layered precipitation;
[0049] (2) After filtering the mixed solution of graphene-AZ91D magnesium alloy chips prepared in the previous step, place it in CO 2 Dry in an atmosphere drying oven (RT+10°C) to obtain flaky graphene-reinforced AZ91D magnesium alloy composites;
[0050] (3) Put the crumb-shaped graphene-reinforced AZ91D magnesium alloy composite material in the mold, and move the mold equipped with the crumb-like graphene-reinforced AZ91D magnesium alloy composite material into the heating furnace, preheat to 300°C together, and keep warm for 10min , and t...
Embodiment 2
[0054] (1) Add 0.4gAl to 100ml, 99.99% analysis 2 o 3 (1μm), using ultrasonic dispersion for 20min to make Al 2 o 3 Evenly dispersed, after treatment, 59.6g of pure AZ31 magnesium alloy scraps were added to the obtained Al 2 o 3 In the alcohol solution, mechanically stir (500rm / min) and ultrasonically disperse for 60min at the same time, so that the AZ31 magnesium alloy chips and Al2O3 are evenly mixed without layered precipitation; the alcohol is 99.99% analytical alcohol;
[0055] (2) the Al obtained in the previous step 2 o 3 / AZ31 magnesium alloy chip mixed solution is filtered and placed in CO 2 Dry in an atmosphere drying oven (RT+10°C) to obtain scrap metal matrix composites;
[0056] (3) Chipping Al 2 o 3 Reinforced AZ31 magnesium alloy matrix composites are placed in the mold and filled with chip-like Al 2 o 3 The mold of the reinforced AZ31 magnesium alloy matrix composite material was moved to the heating furnace, preheated to 280°C together, kept for 20 ...
Embodiment 3
[0060] (1) Add 0.4gAl to 100ml, 99.99% analysis 2 o 3 (1μm), using ultrasonic dispersion for 20min to make Al 2 o 3 Evenly dispersed, after treatment, 59.6g of pure AZ31 magnesium alloy scraps were added to the obtained Al 2 o 3 In the alcohol solution, mechanical stirring (450rm / min) and ultrasonic dispersion for 80min at the same time make AZ31 magnesium alloy chips and Al 2 o 3 Mix evenly without stratification and precipitation; the alcohol is 99.99% analytical alcohol;
[0061] (2) the Al obtained in the previous step 2 o 3 / AZ31 magnesium alloy chip mixed solution is filtered and placed in CO 2 Dry in an atmosphere drying oven (RT+10°C) to obtain scrap metal matrix composites;
[0062] (3) Chipping Al 2 o 3 Reinforced AZ31 magnesium alloy matrix composites are placed in the mold and filled with chip-like Al 2 o 3 The mold of the reinforced AZ31 magnesium alloy-based composite material was moved to the heating furnace, preheated to 250°C together, kept for 5 ...
PUM
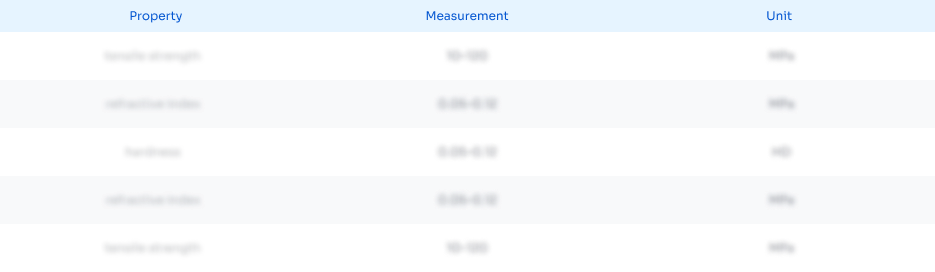
Abstract
Description
Claims
Application Information

- Generate Ideas
- Intellectual Property
- Life Sciences
- Materials
- Tech Scout
- Unparalleled Data Quality
- Higher Quality Content
- 60% Fewer Hallucinations
Browse by: Latest US Patents, China's latest patents, Technical Efficacy Thesaurus, Application Domain, Technology Topic, Popular Technical Reports.
© 2025 PatSnap. All rights reserved.Legal|Privacy policy|Modern Slavery Act Transparency Statement|Sitemap|About US| Contact US: help@patsnap.com