A kind of beneficiation and smelting method of iron-encapsulated mixed copper ore
A mixed copper ore and packaged technology, applied in chemical instruments and methods, flotation, wet separation, etc., can solve the problems of high cost, high operation and maintenance requirements, and achieve the goal of solving difficult recycling, improving comprehensive utilization rate, The effect of reducing the amount of ore
- Summary
- Abstract
- Description
- Claims
- Application Information
AI Technical Summary
Problems solved by technology
Method used
Image
Examples
Embodiment 1
[0023] Embodiment 1: the mass percent composition of copper in the irony wrapped copper ore of the present embodiment is 1.0%, and the oxidation rate of copper is 70%; Taking the copper content in the iron wrapped copper mixed ore as 100%, The content of copper in iron minerals is 35%, and the iron minerals are hematite and limonite;
[0024] Such as figure 1 Shown, a kind of beneficiation and smelting method of iron-encapsulated mixed copper ore, concrete steps are as follows:
[0025] (1) Crush and grind the iron-coated mixed copper ore until the mass percentage of -74μm grain size accounts for 70%. In the mine plan, add 400g of vulcanizing agent (the vulcanizing agent is sodium sulfide), 300g of collector (the collector is butyl xanthate) and 30g of foaming agent (the foaming agent is No. 2 oil) in sequence to carry out a roughing operation To obtain the first roughing concentrate and the first roughing tailings, based on per ton of iron-encapsulated mixed copper ore, add...
Embodiment 2
[0030] Embodiment 2: the mass percent content of copper in the irony wrapped copper ore of the present embodiment is 1.4%, and the oxidation rate of copper is 79.2%; Taking the copper content in the iron wrapped mixed copper ore as 100%, The content of copper in iron minerals is 39.5%, and the iron minerals are hematite and limonite;
[0031] Such as figure 1 Shown, a kind of beneficiation and smelting method of iron-encapsulated mixed copper ore, concrete steps are as follows:
[0032] (1) Crush and grind the iron-coated mixed copper ore to a mass percentage of -74μm, which accounts for 75% of the mass percentage, and adjust the slurry to a mass percentage concentration of 35%. In the mine plan, add 550g of vulcanizing agent (the vulcanizing agent is sodium sulfide), 500g of collector (the collector is butyl xanthate) and 75g of foaming agent (the foaming agent is No. 2 oil) in order to carry out a roughing operation To obtain the first roughing concentrate and the first ro...
Embodiment 3
[0037] Embodiment 3: the mass percent composition of copper in the irony wrapped copper ore of the present embodiment is 1.8%, and the oxidation rate of copper is 87%; Taking the copper content in the iron wrapped copper mixed ore as 100%, The content of copper in iron minerals is 45%, and the iron minerals are hematite and limonite;
[0038] Such as figure 1 Shown, a kind of dressing and smelting method of iron-encapsulated mixed copper ore, concrete steps are as follows:
[0039] (1) Crush and grind the iron-coated mixed copper ore until the mass percentage of -74μm grain size accounts for 80%, and adjust the slurry to a mass percentage concentration of 40%, and the iron-coated mixed copper ore per ton In the mine plan, add 800g vulcanizing agent (the vulcanizing agent is sodium sulfide), 600g collector (the collector is butyl xanthate) and 100g foaming agent (the foaming agent is No. 2 oil) in sequence, and carry out a roughing operation To obtain the first roughing conce...
PUM
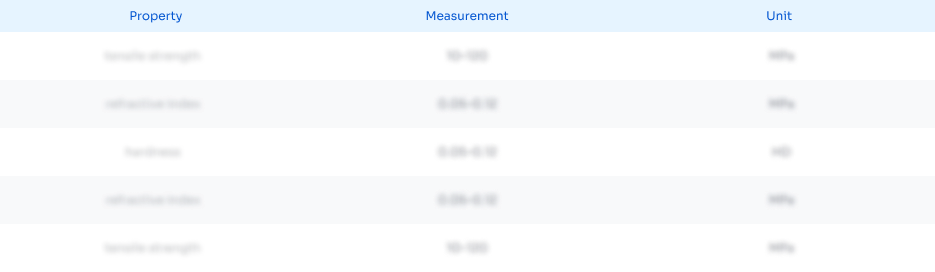
Abstract
Description
Claims
Application Information

- R&D
- Intellectual Property
- Life Sciences
- Materials
- Tech Scout
- Unparalleled Data Quality
- Higher Quality Content
- 60% Fewer Hallucinations
Browse by: Latest US Patents, China's latest patents, Technical Efficacy Thesaurus, Application Domain, Technology Topic, Popular Technical Reports.
© 2025 PatSnap. All rights reserved.Legal|Privacy policy|Modern Slavery Act Transparency Statement|Sitemap|About US| Contact US: help@patsnap.com