Manufacturing method of crankshaft high-performance alloy mold
A manufacturing method and high-performance technology, applied in the field of mold processing, can solve the problems of not meeting the requirements of high temperature resistance, hardness and shrinkage processing performance at the same time, single-component alloy steel performance improvement, poor high temperature resistance, and poor hardness performance. , to avoid the unstable properties of the mold, improve the overall processing performance, and improve the hardness
- Summary
- Abstract
- Description
- Claims
- Application Information
AI Technical Summary
Problems solved by technology
Method used
Examples
Embodiment 1
[0016] A method for manufacturing a crankshaft high-performance alloy mold, comprising the following steps:
[0017] (1) Initial smelting: Put carbon steel in a furnace to heat and melt, add carbon black to the molten steel, then refine at a constant temperature of 1214°C for 1.5 hours, then add mixed alloys for high-temperature fusion to obtain alloy molten steel;
[0018] (2) Forging: Cool the temperature of the furnace to 1173°C at a cooling rate of 11°C / min, keep the temperature at a constant temperature for 4.5 hours, and then refine at 917°C for 1.5 hours to obtain molten steel for forging;
[0019] (3) Casting molding: cast the forged alloy water, and keep the temperature at 916°C for 42min, then cool down at a rate of 6°C / min, and keep at 768°C and 643°C for 1.5h respectively, after processing and grinding, the alloy mold is made ;
[0020] (4) Quenching treatment: place the alloy mold in a high-temperature furnace for quenching treatment, treat it at 817°C for 2.5 ho...
Embodiment 2
[0026] A method for manufacturing a crankshaft high-performance alloy mold, comprising the following steps:
[0027] (1) Initial smelting: Put carbon steel in a furnace to heat and melt, add carbon black to molten steel, then smelt at a constant temperature of 1218°C for 2 hours, then add mixed alloys for high-temperature fusion to obtain alloy molten steel;
[0028] (2) Forging: Cool the temperature of the furnace to 1178°C at a cooling rate of 10-12°C / min, keep it at a constant temperature for 5 hours, and then refine it at 925°C for 2 hours to obtain molten steel for forging;
[0029] (3) Casting molding: casting the forging alloy water, and keeping the temperature at 928°C for 44min, then cooling down at a rate of 8°C / min, keeping at 775°C and 648°C for 2h respectively, after processing and grinding, the alloy mold is obtained;
[0030] (4) Quenching treatment: place the alloy mold in a high-temperature furnace for quenching treatment, treat it at 827°C for 3 hours, and th...
PUM
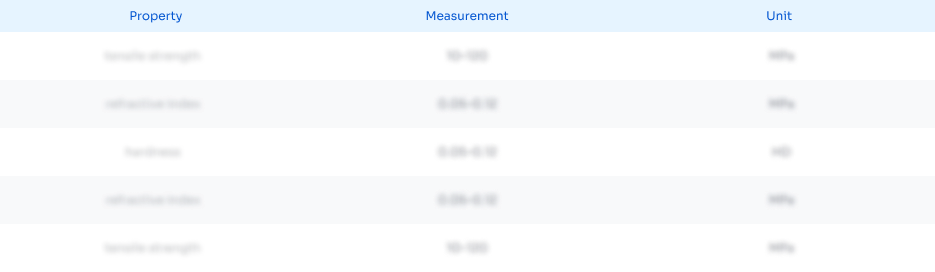
Abstract
Description
Claims
Application Information

- Generate Ideas
- Intellectual Property
- Life Sciences
- Materials
- Tech Scout
- Unparalleled Data Quality
- Higher Quality Content
- 60% Fewer Hallucinations
Browse by: Latest US Patents, China's latest patents, Technical Efficacy Thesaurus, Application Domain, Technology Topic, Popular Technical Reports.
© 2025 PatSnap. All rights reserved.Legal|Privacy policy|Modern Slavery Act Transparency Statement|Sitemap|About US| Contact US: help@patsnap.com