Glass fiber reinforced PPS/PEEK (Polyphenylene Sulfide/Polyether-Ether-Ketone) alloy and preparation process thereof
A glass fiber and alloy technology, applied in the field of glass fiber reinforced PPS/PEEK alloy and its preparation technology, can solve the problems of high fluidity, poor impact strength, difficult injection molding, etc., and achieve stress cracking resistance, excellent strength and The effects of rigidity and excellent processability
- Summary
- Abstract
- Description
- Claims
- Application Information
AI Technical Summary
Problems solved by technology
Method used
Image
Examples
Embodiment 1
[0025] Example 1: SEBS filled with 1Kg polyphenylene sulfide, 99Kg polyether ether ketone, 50Kg iron powder, 3Kg compatibilizer M3002, 5Kg silicone oil (the mass fraction of silicone oil is 5%), 0.2Kg aluminate coupling agent , 0.1Kg antioxidant N412S, 0.1Kg antioxidant N445, and 0.5Kg OP-180 were added to a high-speed mixer and mixed evenly at a high speed, and then 10Kg chopped glass fiber was added and mixed evenly at a low speed to obtain a mixed material. Then the mixed materials are melted, kneaded, extruded, cooled, dried, pelletized into pellets through a twin-screw extruder and then injected into products. Among them, the temperature of each zone of the twin-screw extruder and the screw barrel of the injection molding machine should be kept between 240ˉ310°C.
Embodiment 2
[0026] Example 2: SEB-g-MAH filled with 99Kg polyphenylene sulfide, 1Kg polyether ether ketone, 1Kg silicon carbide, 10KgHIPS, 30Kg fluorine oil (the mass fraction of fluorine oil is 50%), and 2Kg titanate coupling Agent NDZ-101, 1Kg antioxidant 1010, 1Kg antioxidant 168, and 3Kg calcium stearate were added to a high-speed mixer and mixed evenly at high speed, and then 200Kg chopped glass fiber was added and mixed evenly at a low speed to obtain a mixed material. Then the mixed material is melted, kneaded, extruded, cooled, dried, pelletized into pellets by a twin-screw extruder and then injected into products. Among them, the temperature of each partition of the twin-screw extruder and the screw barrel of the injection molding machine should be kept between 240-310°C.
Embodiment 3
[0027] Example 3: 60Kg polyphenylene sulfide, 40Kg polyether ether ketone, 30Kg graphite, 4KgPEEK-g-MAH, 20Kg silicone oil filled SEBS-g-MAH (silicone oil mass fraction is 25%), 2Kg aluminate Joint agent, 0.4Kg N412S, 0.4Kg antioxidant N445, 1Kg stearic acid, 0.5Kg light stabilizer were added to the high-speed mixer and mixed evenly at high speed, and then 80Kg chopped glass fiber was added and mixed evenly at low speed to obtain a mixed material. Then the mixed material is melted, kneaded, extruded, cooled, dried, pelletized into pellets by a twin-screw extruder and then injected into products. Among them, the temperature of each partition of the twin-screw extruder and the screw barrel of the injection molding machine should be kept between 240ˉ310°C.
PUM
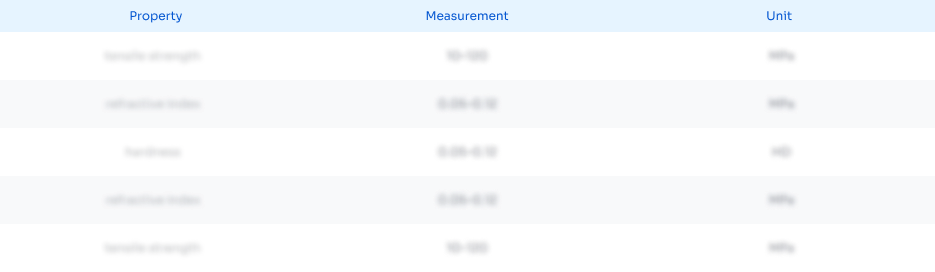
Abstract
Description
Claims
Application Information

- R&D
- Intellectual Property
- Life Sciences
- Materials
- Tech Scout
- Unparalleled Data Quality
- Higher Quality Content
- 60% Fewer Hallucinations
Browse by: Latest US Patents, China's latest patents, Technical Efficacy Thesaurus, Application Domain, Technology Topic, Popular Technical Reports.
© 2025 PatSnap. All rights reserved.Legal|Privacy policy|Modern Slavery Act Transparency Statement|Sitemap|About US| Contact US: help@patsnap.com