Broadband absorbing material based on frequency selective surface and sandwich structure design and preparation method thereof
A frequency-selective surface and interlayer structure technology, applied in the field of wave-absorbing materials, can solve the problems of limited electromagnetic wave attenuation ability and single form, and achieve the effects of adjustable and controllable wave-absorbing frequency, widening the application field, and easy operation
- Summary
- Abstract
- Description
- Claims
- Application Information
AI Technical Summary
Problems solved by technology
Method used
Image
Examples
preparation example Construction
[0038] In the field of low temperature (<400°C) application, the preparation method of the absorbing material includes: (1) When the dielectric layer is resin / polymer: according to the structural design plan, firstly use the compression molding process to prepare the upper and lower layers with a specific thickness. The lower medium layer, and then use the brushing process to periodically arrange and paste the FSS film on the inner surface of the medium layer, and finally achieve three-layer adhesion; (2) When the medium layer is a fiber-reinforced resin-based composite material / polymer-based composite material : Taking the two-dimensional (fiber cloth layer) prefabricated body structure as an example, according to the structural design plan, first determine the thickness of the upper and lower medium layers and the number of fiber cloth layers, and then carry out fiber cloth layering. Then the FSS film is periodically arranged on the surface of the corresponding layer of fiber...
Embodiment 1
[0042] (1) 300 mg of graphene oxide was placed in 300 mL of ethylene glycol solution for ultrasonic dispersion for 3 h to prepare a 1 mg / mL graphene oxide dispersion.
[0043] (2) Pour the uniform graphene dispersion into a polytetrafluoroethylene reactor, treat at 180° C., and keep warm for 12 hours.
[0044] (3) Take 10 mL of the hydroheated dispersion and slowly drop it into a vacuum filter bottle, dry it naturally, and remove the graphene film from the microporous filter. Repeat the above operations to prepare a series of identical graphene films.
[0045] (4) Put the composite film obtained by the above treatment in a muffle furnace (argon atmosphere), heat treatment temperature 600° C., keep it warm for 1 hour, and then cool down with the furnace.
[0046] (5) The upper and lower dielectric layers are all selected as molded epoxy resin boards, d 1 = 2.2mm, d 2 = 1.2 mm. The graphene film is pressed as figure 1 It is periodically coated on the lower dielectric board,...
Embodiment 2
[0049] (1) 300 mg of graphene oxide was placed in 300 mL of ethylene glycol solution for ultrasonic dispersion for 3 h to prepare a 1 mg / mL graphene oxide dispersion.
[0050] (2) Pour the uniform graphene dispersion into a polytetrafluoroethylene reactor, treat at 180° C., and keep warm for 12 hours.
[0051] (3) Take 10 mL of the hydroheated dispersion and slowly drop it into a vacuum filter bottle, dry it naturally, and remove the graphene film from the microporous filter. Repeat the above operations to prepare a series of identical graphene films.
[0052] (4) Put the composite film obtained by the above treatment in a muffle furnace (argon atmosphere), heat treatment temperature 800° C., keep it warm for 1 hour, and then cool down with the furnace.
[0053] (5) Pour polydimethylsiloxane resin (PDMS) into a mold of 180mm*180mm*3mm, and cure at high temperature to obtain d 1 = 3mm PDMS dielectric layer. The graphene film is pressed Figure 1 The arrangement shown is pla...
PUM
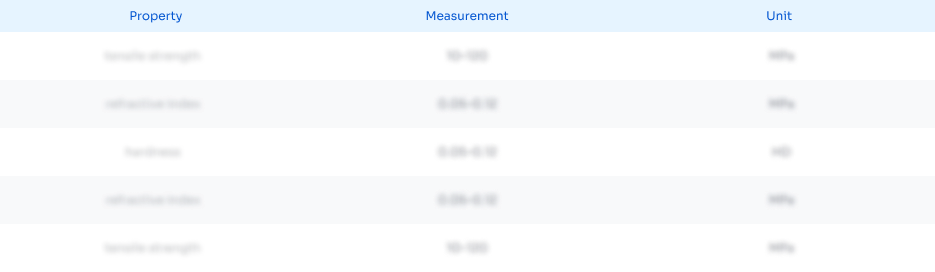
Abstract
Description
Claims
Application Information

- Generate Ideas
- Intellectual Property
- Life Sciences
- Materials
- Tech Scout
- Unparalleled Data Quality
- Higher Quality Content
- 60% Fewer Hallucinations
Browse by: Latest US Patents, China's latest patents, Technical Efficacy Thesaurus, Application Domain, Technology Topic, Popular Technical Reports.
© 2025 PatSnap. All rights reserved.Legal|Privacy policy|Modern Slavery Act Transparency Statement|Sitemap|About US| Contact US: help@patsnap.com